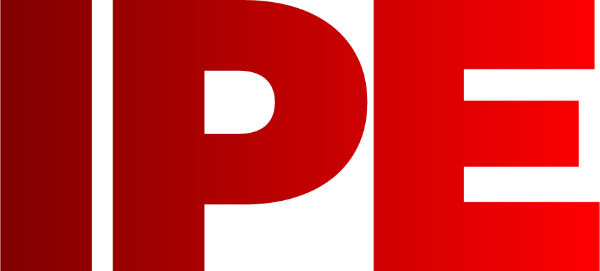
![]() |
Edward Lowton
Editor |
![]() ![]() |
Home> | Production Engineering | >Grinding and abrasives | >Blast room enables a perfect finsh |
Home> | Handbooks | >Manufacturing Matters Ireland | >Blast room enables a perfect finsh |
Blast room enables a perfect finsh
29 October 2018
A high-performance abrasive blasting system has been installed by Hodge Clemco within an existing chamber for surface preparation of steelwork for commercial trailers and vehicle bodies manufactured by Tiger Trailers in Cheshire.
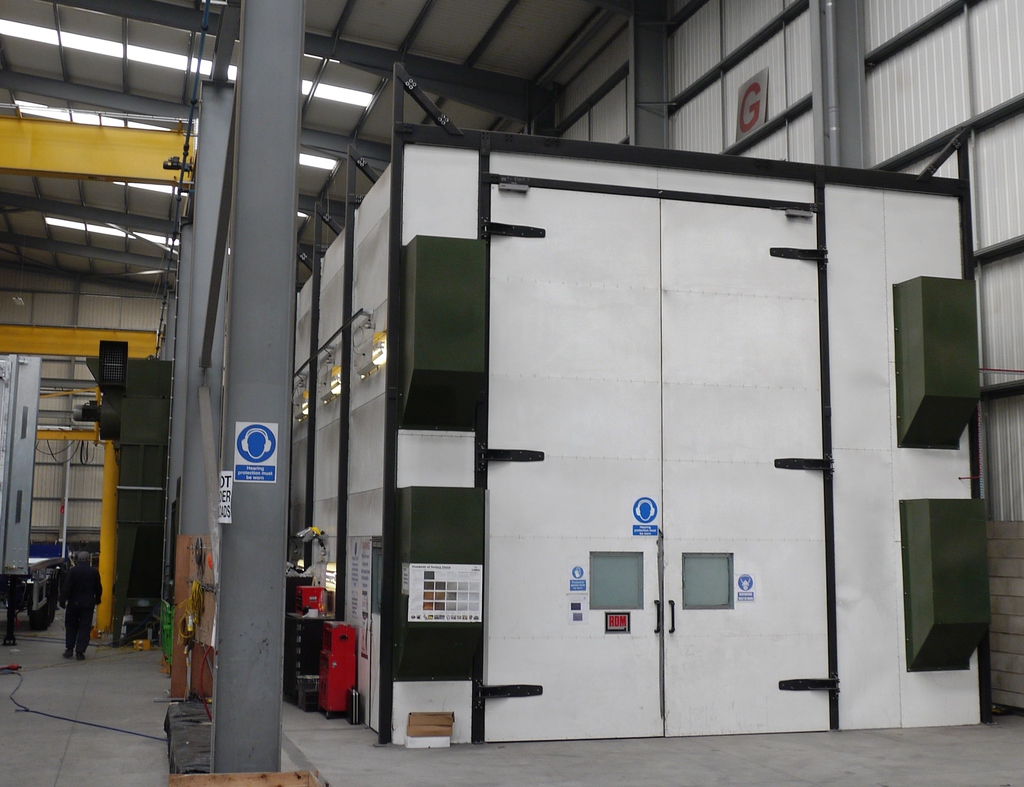
Originally the company used sub-contractors to prepare chassis and other steel parts on site before they were painted. With sales growing and a high standard of finish a priority, Tiger Trailers appointed Hodge Clemco to convert the preparation room into a self-contained blast-room with dust extraction and media recycling for use by its own staff.
The room, which is 20m long x 6m wide x 8m high, has been fitted with a complete air-flow and dust extraction system that operates at 14,000cfm to maintain clear visibility for operators. Two high-capacity machines with an expendable abrasive capacity of 300kg each are used for the blasting work and include large-bore pipework for efficient air-flow and large access plates for easy maintenance.
The media recovery system installed by Hodge Clemco consists of a hopper in the blast-room floor that feeds a separator system where contaminants, fines and dust are removed by an air-wash system and scalping drum. Clean abrasive is delivered continuously to a 10t-capacity storage hopper, which allows the two blast machines to work for long periods without interruption. The system has been designed to handle the chilled iron abrasive generally used. Dust is collected automatically for disposal.
The contract required close collaboration between Hodge Clemco and Tiger Trailers to minimise disruption and also included certified training for up to six Tiger personnel. After-sales service has maintained the system in optimum condition and dealt quickly with any problems, according to the company.
- Blast room upgrade
- Blast room installed
- Blast cabinets help upgrade aircraft maintenance facilities
- Bespoke blast cabinets boost finishing capacity
- New blast room installed
- Self-contained blast room
- Custom-built blast cabinet saves cost
- Low-dust abrasive
- Tipper body manufacturer upgrades finish quality
- Maintenance packages