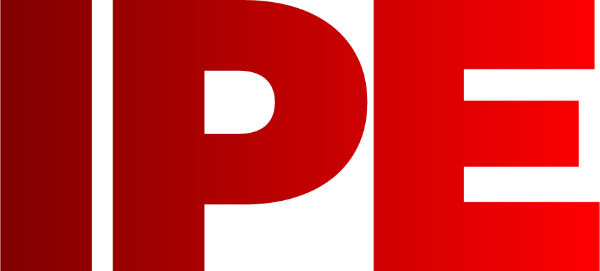
![]() |
Edward Lowton
Editor |
![]() ![]() |
Home> | Efficient Maintenance | >Reliability-centred maintenance | >Hydraulic equipment maintenance & improvement |
Hydraulic equipment maintenance & improvement
27 July 2020
Fugro, the world’s leading geo-data specialist, has worked with Bosch Rexroth for over a decade to ensure it has the best hydraulic systems and software solutions on board its geotechnical drilling vessel, the Fugro Synergy. Now, they are working together again in order to better prepare for the future
The Fugro Synergy vessel has been in operation since 2009, and is primarily used to drill into the seabed in order to analyse whether it can be safely used as a foundation for structures like wind farms or oil rigs. This ship was built to be effective in the harshest conditions, and Bosch Rexroth provides the drives and controls for operating under these circumstances. During the operation, motion compensation of the vessel at sea is one of the drive and control challenges we faced. Two long stroke Heave Motion Compensator cylinders in combination with a compensating accumulator and intelligent software ensures that the drilling operation remains steady and accurate even when waves increase in size.
As the ship has been operational for ten years, a full service of the hydraulics system and associated software is required. It has been performing reliably for the entire time, so the main focus of the service and maintenance is to ensure another decade of smooth operation. However, as the vessel is in dry-dock, this presents a great opportunity to look at ways to improve the system even further.
"A full recertification process is necessary every ten years, and this is to ensure that the vessel continues to comply with the DNV GL standards," says Mark Timmermans, Account Manager at Bosch Rexroth. "Fugro then asked us what we would recommend for the hydraulics system going into the future. Generally speaking, they want another ten years of smooth operation, improve up-time, and more specifically asked for some alterations to improve the existing setup."
Planned maintenance
An overhaul and exchange program for the main hydraulic pumps is in place as part of planned maintenance, and all these activities require good cooperation of the Boxtel service shop and service technicians on board. Fugro also requested that Bosch Rexroth look into a way to fix the level of noise coming from some parts of the ship, along the main hydraulic pressure lines. So, as part of the overall maintenance, Bosch Rexroth are implementing a solution.
“As part of the 10-year survey, we’re replacing all seals, bearings and wear parts of the hydraulic components,” adds Mark. “We are ensuring that everything is operating as it was when it was new, but now with the benefits of all the software updates we’ve implemented over the years. The hydraulics system was still in very good shape thanks to the competence and care of the crew on board the Fugro Synergy, but this was the right time to replace these parts. It’s a more complex task to reduce the noise level, but we are solving it together with Fugro by changing the entire layout of the pressure lines, and installing noise dampeners.”
Although the system was still performing according to expectations, the replacements are necessary in order to extend lifetime under the harsh offshore conditions. This process ensures that there will be no surprises or problems in the years to come. However, as the vessel was in dry dock for a number of weeks, it was the perfect opportunity to modernise further and introduce “smart maintenance” solutions.
“Previously, if there were software issues, we would have to send out a Bosch Rexroth engineer,” explains Mark. “So jointly, we decided to install additional software making remote access of the control system possible. This means if there’s an issue we can analyse it much quicker, without the need to travel wherever the ship may be. In addition to this, we are implementing a data logger to monitor and analyse the system over longer periods as a basis for predictive maintenance in the future. These additions can help to optimise the operational efficiency for longer periods, and we’re happy to be able to innovate alongside a partner like Fugro.”
- Maintenance in the digital world
- Offshore developments
- Inside intelligence helps boost maintenance
- Interactive communication platform
- Prepare for new directive
- Industry 4.0 ready guidance platform
- Oil analysis: Helping boost machine uptime?
- Bosch Rexroth - Visit us on stand 22, Maintec
- Online hydraulics catalogue
- Too much maintenance remains reactive
- Distribution
- Reliability strategy: New thinking required
- RCM : The quest for easier implementation
- Strong cast for Maintec theatres
- Top tips to keep your belts in business
- Boosting the scope of shrink fits with engineering adhesives
- Advanced pump analysis proves invaluable
- Keeping your diesel engine healthy
- Optimising machine reliability
- IP&E Live: Full line-up here!