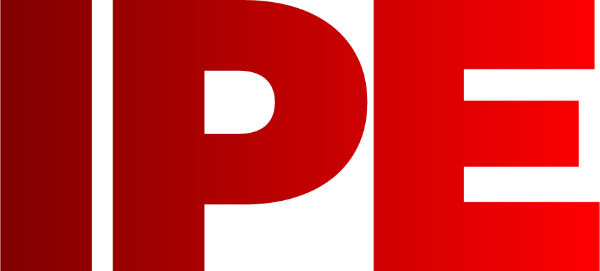
![]() |
Edward Lowton
Editor |
![]() ![]() |
Home> | Efficient Maintenance | >Reliability-centred maintenance | >Strong cast for Maintec theatres |
Strong cast for Maintec theatres
02 October 2018
The Reliability Dialogue theatre forms part of the educational content of Maintec 2018. Here, Andy Pye, the event's senior editorial consultant, reviews the aims of the theatre and reveals the objectives of a behind-closed-doors round table discussion
Running alongside the impressive list of keynote and blue chip speakers in the Maintec Insights theatre is the Reliability Dialogue theatre.
The sessions in this theatre are short (25 minute) panel discussions involving three or four key participants, many of whom are show exhibitors, or speakers from Maintec Insights sessions running alongside. In this tight timeframe, each participant is allowed a brief presentation of around 3 to 5 minutes, with the remaining time dedicated to a Q&A session.
Questions will be taken from the floor, or previously submitted by readers of the supporting publications, including this one. Of course, discussions may continue unmoderated following the closure of the official session, or where exhibitors are involved, back at the company stand.
To make the discussions ever more relevant, a limited number of visitors will be accepted, by prior arrangement, onto the Reliability Dialogue panels.
Details of how to ask a question, or to apply to be a participant, are given in the box at the end of the article.
The Reliability Dialogue Sessions
Tuesday 6th November
Rail and transport, 11.15 to 11.40
We are all accustomed to trains being replaced by buses due to Planned Engineering Works. How is disruption to services minimised, as the rail companies fight to maintain vehicles and tracks on which they run?
Track maintenance machines have become increasingly automated, but certain areas still require the strength and attention of trained operators. The Internet of Trains enables metros, passenger and freight services to use sensors, Machine2Machine learning, the Big Data analytics, cloud computing and other tech to gather and analyse information from a wide variety of sources and data streams. This benefits not just IT, but also engineering, maintenance, signalling, communications, ticketing and on-board experience.
Asset maintenance strategies, 13.05 to 13.30
Maintaining machines and equipment at optimal performance levels can be a constant battle. Asset Maintenance Management describes the continuous process improvement strategies for improving the availability, safety, reliability and longevity of physical assets (systems, facilities, equipment and processes).
With a plethora of different strategies to address, upkeep of critical assets can be daunting when it comes to determining which strategy is most cost-effective and successful in the long run. Are you in reactive mode? Should you follow a pre-determined schedule? Should you wait until there is a clear deviation? Does preventive maintenance do more harm than good?
From Condition Monitoring to Predictive Maintenance, 14.05 to 14.30
Regular maintenance is good - but it can be costly if parts are replaced or repaired at the wrong time. Particularly in just-in-time production, outages and production downtimes can have a devastating impact, which quickly affects many other parts of the value chain and ultimately company performance and its asset. Predictive maintenance uses an array of sensors and intelligent components to expand options for detection and visualisation of operational data. All data is available for quick evaluation on site and is used to detect wear and irregularities during operation long before damage or downtime occur.
Energy utilities, 15.05 to 15.30
What systems are available for energy utilities to minimise the risk of failure and maximise equipment lifetimes in the most cost-effective way, increasing reliability? Such approaches should include elements of predictive maintenance and preventive maintenance to prioritise maintenance where it will be most effective. It should also combine asset condition data (such as oil analysis, device testing, thermography, and visual inspection) with real-time operational data.
Wednesday 7th November
The digital factory, 11.15 to 11.40
A digital factory uses digital technology for modelling, communications and to operate the manufacturing process. This arrangement of technology allows managers to configure, model, simulate, assess and evaluate items, procedures and system before the factory is constructed. Downtime should be minimised because predictive maintenance procedures, based on historical and real-time data for each piece of equipment, automatically address incipient problems before a breakdown.
Gathering and managing data, 13.05 to 13.30
This session looks at typical Industry 4.0 devices used to gather data from processes. What type of data should be gathered? How should Big Data be handled, and where should it be stored - locally, in the Cloud, or in the "Fog"?
Although the IoT is currently driven by connecting field devices to the cloud, there are limitations. Most IoT implementations are about connecting to - and doing all of the processing in - the cloud. Although this can work for the consumer IoT, for Industrial IoT systems not everything can take place in the cloud.
The other major issue confronted with cloud computing is security and privacy. Since the cloud systems have been located with the Internet, user requests, data transmission and system responses need to traverse many intermediate networks depending on the distance between the users and systems. When customer data is in a public cloud, there is a risk of them being compromised of their integrity and confidentiality.
Fog computing refers to extending cloud computing to the edge of the network of the enterprise. Also known as Edge Computing (or Fogging), it facilitates the operation of compute, storage and networking services between end devices and cloud computing data centres. By handling the services that make up the Internet of Things (IoT) at the network edge, data can in many cases be processed more efficiently than if it needed to be sent to the cloud for processing.
Remote measurement, 14.05 to 14.30
The use of Industry 4.0 compliant devices means that remote facilities, such as substations and water supply facilities, no longer have to be physically visited to monitor their performance. Remote Measurement products are used by companies and authorities that need to measure and monitor aquatic environments, machinery and equipment, and weather conditions.
Remote Measurement systems gather measurement data in locations where infrastructure is lacking. This is possible because measurement data is sent by satellite or mobile telephony networks from devices on site, many with their own power supply.
We look at examples in use today and consider how their use might be extended.
Maintenance with robots, 15.05 to 15.30
Robots are useful in providing a means of inspection of locations which are hazardous for humans to inspect, or difficult for them to access. Robotics is playing an increasing part in maintenance of such installations as nuclear facilities, and wind turbines, while drones can fly above cranes and look down with sophisticated visual and thermal cameras to see what might be going strong. When and where is the investment justified?
Round table discussion
On the evening of the first day at Maintec, and shortly after the close of the exhibition, I shall be chairing a behind-closed-doors round table discussion involving invited key senior maintenance specialists from users and suppliers in the manufacturing and process sectors.
The key theme to be explored during the session will be Overall Equipment Effectiveness (OEE). The discussion will consider the effect on OEE of predictive maintenance, including the advent of Industry 4.0 devices, and in particular, how the concepts relate to the SME community in the UK.
The 'Six Big Losses' which affect OEE are:
- Planned downtime
- Minor stops
- Production rejects
- Breakdowns
- Speed loss
- Rejects on start up
The session, which will last about 90 minutes, will be audio recorded, transcribed, edited and published subsequently in the relevant Western Business Publishing titles.
The sponsor for this session is Festo, who will provide a panel member. Also providing a panel member will be Bosch Rexroth, sponsor of the Reliability Dialogue and Maintec Insights theatres. Other confirmed panel members to date include representatives of exhibiting companies SSG Insight, EMS Cognito and SPM Instruments. We are in the process of adding further panel members.
At a similar event two years, the slow uptake of the SME community of Industry 4.0 technologies was highlighted: at the time, Chris Greenough, commercial director of Salop Engineering, a manufacturer of pressings and assemblies based in Shrewsbury, and president of Shropshire Chamber of Commerce, said: “Digitisation has been pushed through the large OEMs and first tier companies and that hasn’t filtered down to the SMEs. Yet, this is where the biggest potential improvement is.”
Adam Payne managing director of TCM UK, which specialises in lean manufacturing strategy and 3D printing, added: “It is recognised – as Chris says, it is easy to roll it out to the OEMs, they have the investment and teams. But it is the manufacturing SMEs that can make the biggest difference – they can get so much out of it – energy savings, remote monitoring. Therefore, we need to see a proper manufacturing policy, which involves everyone, so we all get to the same end goal.”
Justin Leonard, director at Igus, manufacturer of cables, cable assemblies and plastic bearings, caught the mood of the discussion at the time, saying “With SMEs, we need to approach Industry 4.0 in small steps. For example, we can introduce smart products that can indicate how long they are going to last (say, warning 50%, 75% of the way through the lifetime). Users of these products don’t have a lights-out factory, but they are already using Industry 4.0 technology, they just don’t realise it.”
How have things changed since? Unfortunately, while 80% of UK manufacturers say industry 4.0 will be a reality by 2025, only 11% expect to be ready to capitalise on it, according to information recently released by the recently launched Green Technology Task Force (London, 12th September 2018).
Steve Brambley, chief executive of GAMBICA, the Trade Association for Instrumentation, Control, Automation and Laboratory Technology, and a Tech Task Force member, said: “Smart technology can be used to reduce energy consumption, eliminate waste and decrease carbon emissions. As well as being environmental imperatives, these are important goals for the UK’s long-term competitiveness.”
In launching the scheme, Claire Perry, Minister of State at the Department for Business, Energy and Industrial Strategy, emphasised that the UK has a long history of brilliant ideas, but is less successful in holding onto the intellectual property (IP).
***BOX COPY***
How to take part in Reliability Dialogue
Submit a question: If you have a question you would like to be debated at one of the Reliability Dialogue sessions, please email it to Andy Pye at [email protected]. It would be best to ask the question in person – and be there to hear the answer – so please indicate if you intend to be present at the session. We will contact you if we intend to use your question.
Why not take part? Or go a stage further! If you are planning to attend Maintec and have a maintenance story to share with other visitors during the Reliability Dialogue, you could be accepted onto one of our panels. Just contact Andy on [email protected]. In this case, if accepted, we will ask you for a guarantee of attendance, but will pay reasonable travelling expenses in return.
- Health increases wealth
- Remote monitoring in the oil industry
- IP&E Awards showcase industrial excellence
- The benefits of centralised lubrication systems
- Ultrasound solutions for predictive maintenance
- Time for a dialogue on safety
- Dates announced for Maintec 2018
- InVMA acquires the Intellectual Property and Assets of IoT communications company AMIHO Technology Limited
- Valuekeep establishes a partnership with g3p consulting
- Smart maintenance for the smart factory
- Distribution
- Reliability strategy: New thinking required
- RCM : The quest for easier implementation
- Top tips to keep your belts in business
- Boosting the scope of shrink fits with engineering adhesives
- Advanced pump analysis proves invaluable
- Hydraulic equipment maintenance & improvement
- Keeping your diesel engine healthy
- Optimising machine reliability
- IP&E Live: Full line-up here!