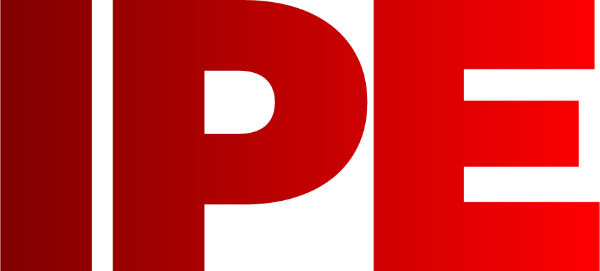
![]() |
Edward Lowton
Editor |
![]() ![]() |
Home> | Efficient Maintenance | >Reliability-centred maintenance | >Reliability strategy: New thinking required |
Reliability strategy: New thinking required
16 July 2018
More than 90% of the companies EMS Cognito comes across have a reliability strategy based simply on servicing the components of the machine. Here, the company explains why it believes a paradigm shift in thinking is required
Maintainers are excellent at repairing faults, rebuilding machines to a new standard and replacing components when they fail – that’s what they’ve been trained to do and not surprisingly, they do it well.
In continuous improvement circles, proponents of Total Productive Maintenance (TPM) often encourage this type of strategy leading to clean, shiny components and a boost to reliability – but one that falls far short of potential.
So how to reach the potential?
A paradigm shift in thinking is required. Instead of leaving maintainers to focus on components while production managers focus on production speed, health and safety managers on keeping people safe and quality managers on product quality, an integrated approach is required.
The light-bulb moment is when you take time to understand the process, its functions and the standards of performance you require in terms of safety, productivity and quality. Then you realise that reliability is not about components but about maintaining these functions to the required standard of performance – standards of performance that are set by you, your customers, regulators and legislative requirements.
Another amazing fact – in the vast majority of cases, the team responsible for defining the maintenance strategy (the maintenance department or the original equipment manufacturer) does not have a full understanding of the functions and standards of performance required from the process. Hence why most reliability strategies fall well short of their potential.
Accepting this paradigm shift in thinking opens the door to an integrated approach to redefining the requirements to maintain the process operating at the required standards. It’s an integrated approach that requires the involvement of all business functions representing safety, quality, production and maintenance.
That’s exactly what Lean RCM does. It recognises that reliability is rarely just associated with component failures but much more to do with maintaining the processes operating safely to supply customers with the product they want, when they want it, at the quality they expect.
Lean RCM is a best-practice methodology for improving process reliability bringing together the rigour of maintenance practice in the aircraft industry with the culture and efficiency of Lean Manufacturing.
What does Lean RCM achieve?
Lean RCM provides users with an integrated strategy that ensures processes perform at their desired levels of performance for the lowest cost possible. In addition to improvement in process availability, expect to see a 40% reduction in maintenance costs, up to 80% of the preventative maintenance tasks conducted with the process still operational and the majority of these tasks conducted by the equipment operators using lean management techniques and standard operating procedures.
It comes with an externally accredited qualification ensuring that practitioners and facilitators demonstrate the necessary competencies and high standards associated with such a world-class technique.
Having a qualification in Lean RCM demonstrates an understanding of this different approach to reliability and that you’ve been through that light-bulb moment. At the highest level of the qualification; Lean RCM Facilitators – transform the approach to reliability allowing businesses to reach the full potential other approaches do not achieve.
- Distribution
- RCM : The quest for easier implementation
- Strong cast for Maintec theatres
- Top tips to keep your belts in business
- Boosting the scope of shrink fits with engineering adhesives
- Advanced pump analysis proves invaluable
- Hydraulic equipment maintenance & improvement
- Keeping your diesel engine healthy
- Optimising machine reliability
- IP&E Live: Full line-up here!