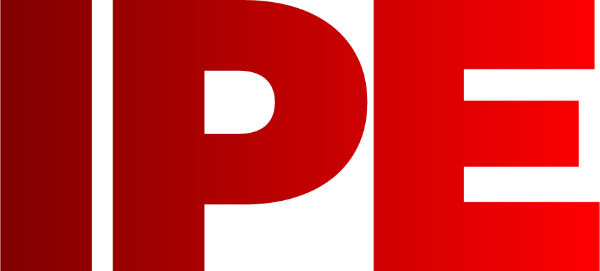
![]() |
Edward Lowton
Editor |
![]() ![]() |
Putting energy into data
29 November 2018
Businesses operating across the oil and gas industry are waking up to the potential of big data and the role it can play in improving efficiency and reduce maintenance costs. Charlotte Stonestreet looks at some of the digital success stories as well as developments in conventional technologies
There is no doubt that the oil & gas sector has faced recent challenges, with falling prices and a lack of investment, however over the years the industry has been a major contributor to the Treasury (paying almost £330 billion in production tax since the 1970’s), provided hundreds of thousands of skilled jobs, formed a vibrant supply chain servicing oil and gas activity at home and abroad, and made a key contribution to the UK’s security of energy supply.
In Oil & Gas UK’s Business Outlook 2018, Chief Executive Deirdre Michie points outfit the sector is adapting to the demanding business environment and, as a result, is now in a more competitive position
“The UK offshore oil & gas industry has improved it’s resilience, been reshaped and we are beginning to see a revival in activity,” says Michie. “There are still challenges, of course, to sustain this improved outlook, even in the short term.
“Drilling in just one area in our supply chain that reminds under intense pressure because of a shortage of global capital, but we are making the best of the opportunities we have. Unit operating costs have been halved and we are in a much more competitive and efficient basin that we have been for years.
“We need to maximise the potential of existing fields, as well as actively explore for new oil and gas because the investment decisions we make today are key to how much we will be producing in the years to come.”
Big data
Like many other sectors, the Oil & Gas industry is waking up to big data and the way in which it can help improve efficiency and reduce maintenance costs. Indeed, a joint study by the UK oil and gas industry’s Technology Leadership Board, the Oil & Gas Technology Centre and the Oil and Gas Authority (OGA) has found that adopting data analytics and digital technologies for asset maintenance and operations could increase production and lower maintenance costs worth £1.5 billion annually to the UK Continental Shelf (UKCS).
The failure of critical equipment offshore, such as gas compression, oil export, power and water injection systems, resulted in lost production of around 110 million barrels of oil equivalent on the UKCS in 2017.
The study investigated how data from topsides production and operations equipment is currently being used, and can help sustainably improve production efficiency and maintenance planning, reducing operational costs.
More than 60% of the study’s participants reported that adequate data infrastructure is in place, with extensive sensor coverage across offshore assets and ‘good to excellent’ transmission and data storage capabilities.
A small number of North Sea and international operators are already benefitting from data analytics technologies, with case study examples including a 65% reduction in system outages and annual maintenance savings of more than £1 million per year on a single system.
However, the application of data analytics is not widespread and consistent across the industry or individual organisations. There is a lack of awareness as to what digital technology is available and, more importantly, the potential value it can deliver to a business. There is also a perceived high cost of implementing such technologies, and risk aversion to their deployment.
Furthermore, other industries, like power and utilities, and aviation, are more advanced than the oil and gas one, and have been using data analytics to transform the way they manage their assets, demonstrating large efficiency gains.
Adopting data analytics and digital technologies across the basin could deliver a 25% improvement in the reliability of critical equipment and systems and a 15-20% reduction in overall maintenance spend, resulting in an estimated £1.5 billion of value to the UKCS per year.
Recommendations to overcome these barriers, include:
– Assign ownership of these findings to the appropriate industry groups, like the Asset Stewardship Task Force (ASTF) and the Production Efficiency Task Force (PETF), to ensure an industry-wide understanding on how digital technologies can deliver value to UKCS operations;
– Issue the industry with a standard methodology for assessing their data analytics technology maturity and engage the industry leadership on opportunities to close the gaps;
– Through the OGA, engage operators on the deployment of digital technologies at their UKCS assets as part of their Technology Plans.
Advanced analytics
Further afield, BP has successfully deployed Plant Operations Advisor (POA), a cloud-based advanced analytics solution developed with Baker Hughes, a GE company, across all four of its operated production platforms in the deepwater Gulf of Mexico.
The move comes after an initial deployment of POA proved the technology could help prevent unplanned downtime at BP’s Atlantis platform in the Gulf. The technology has now been successfully installed and tested at BP’s Thunder Horse, Na Kika and Mad Dog platforms – and it will continue to be deployed to more than 30 of BP’s upstream assets across the globe.
“BP has been one of the pioneers in digital technology in our industry, and co-development of Plant Operations Advisor with BHGE is a key plank of modernizing and transforming our upstream operations,” said Ahmed Hashmi, BP’s global head of upstream technology. “We expect the deployment of this technology not only to deliver improvements in safety, reliability and performance of our assets, but also to help raise the bar for the entire oil and gas industry.”
Built on GE’s Predix platform, POA applies analytics to real-time data from the production system and provides system-level insights to engineers so operational issues on processes and equipment can be addressed before they become significant. POA helps engineers manage the performance of BP’s offshore assets by further ensuring that assets operate within safe operating limits to reduce unplanned downtime.
Now live across the Gulf of Mexico, POA works across more than 1200 mission-critical pieces of equipment, analysing more than 155 million data points per day and delivering insights on performance and maintenance. There are plans to continue augmenting the analytical capabilities in the system as POA is expanded to BP’s upstream assets around the globe.
BP and BHGE announced a partnership in 2016 to develop POA, an industry-wide solution for improved plant reliability. The teams have built a suite of cloud-based Industrial Internet of Things (IoT) solutions that have been tailor-fit for BP’s oil and gas operations.
“The partnership between BP and BHGE has resulted in a unique set of capabilities that quickly find valuable insights in streams of operational data,” said Matthias Heilmann, president and CEO of Digital Solutions and chief digital officer for Baker Hughes, a GE company. “Together, we are creating leading-edge technologies to automate processes and increase the safety and reliability of BP’s upstream assets. As we extend the solution globally, this will become the largest upstream Industrial IoT deployment in the world when complete.”
Cybersecurity
With increased digitalisation comes increased need for cybersecurity. According to recent research conducted by Ponemon Institute on the state of cybersecurity in the U.S. oil and gas industry, deployment of cybersecurity measures in the industry isn't keeping pace with the growth of digitalisation in oil and gas operations. Just 35 percent of survey respondents rate their organisation's OT cyber readiness as high. Sixty-eight percent of respondents say their organisation experienced at least one cyber compromise, while 61 percent say their organisation's industrial control systems protection and security is not adequate.
Addressing this, Siemens and leading provider of industrial control system (ICS) cybersecurity solutions, PAS Global, have entered into an agreement to provide fleet-wide, real time monitoring for control systems, providing customers with the deep analytics required to identify and inventory proprietary assets, and the visibility to detect and respond effectively to attacks across the operating environment.
The Siemens-PAS global strategic partnership bridges the visibility gap for distributed, legacy control assets to provide a comprehensive view into fleet security. Focused on gathering detailed configuration data down to the sensor, the Siemens-PAS partnership will enable customers to secure proprietary systems in multi-vendor environments – guarding against cyber attacks as well as unauthorised engineering changes.
Condition monitoring
Operators of oil and gas platforms need to continuously monitor their sites’ ambient condition status through parameters such as gas concentration levels, differential pressures and temperatures. Mobile explosion-proof detectors and transmitters allow such measurements to be made at various different key locations on the platform and then be re-positioned as required. The readings from these instruments are switched and recorded via an explosion-proof central controller. These pre-existing detectors and central controller enclosures will typically already have glanded conduit access points. Because of the stringent requirements of explosion-proof equipment, users need to avoid making any modifications to such certified equipment.
In order to save valuable installation time and to maximise location flexibility of such a mobile detection system onto an oil or gas platform installation, HARTING offers an exposion-proof connection solution with the compact Han Ex 4A cable-to-cable connector system, a product that can be retrofitted without compromising the equipment’s Ex certification compliance. Because all detectors are provided with pre-fitted connector cable ends, they are supplied to site fully pre-tested, which ensures fast pluggable installation.
Automation, security & safety
ABB’s innovative security, monitoring and communications technology has been installed on the 1,850 km Trans-Anatolian Natural Gas Pipeline (TANAP). The first phase, ‘Gas to Eskisehir’ officially opened in early summer 2018 ahead of schedule. ABB provided the security, telecommunications, SCADA main control room, containerized equipment rooms and has installed the fiber optic cable along the pipeline to contribute to this achievement.
As part of the project and for the first time in a subsea water crossing, ABB has installed a fiber optic leak detection and subsea pipeline monitoring system detecting events such as anchor drag. Over 4,000km of fiber optic cable has been installed across challenging terrain and during difficult weather conditions. Both control and telecommunication systems data are carried along the fiber optic cable that runs the length of the pipeline. It provides a vast communications infrastructure capable of handling extremely large volumes of data and is the longest system of its kind in the world.
ABB has also been responsible for installing a single comprehensive integrated security system, which monitors the external and internal CCTV cameras and the perimeter intruder detection system of every site. This pipeline intrusion detection system covers every meter of pipeline. Incorporating over 1,300 cameras and 650 access control points, this is the largest integrated security system that ABB has installed to date. The TANAP Project brings natural gas produced from Azerbaijan’s Shah Deniz-2 gas field, and other areas of the Caspian Sea, primarily to Turkey, but also on to Europe for the first time. TANAP, along with the South Caucasus Pipeline (SCP) and the Trans-Adriatic Pipeline (TAP), form the elements of the Southern Gas Corridor. The TANAP pipeline is scheduled to complete June 2019.
Per-Erik Holsten, managing director Oil, Gas & Chemicals ABB said: “TANAP engineers were embedded within our own ABB team, helping to identify key priorities and resolve issues as they arose. This close collaboration between us ensured that the project ran smoothly - in fact ahead of schedule and on budget. With the TANAP pipeline running the entire length of Turkey and across mountainous terrain, this was no small feat. It’s been a truly joint effort to produce first gas."
Energy efficient
WEG has recently announced that, as standard, it is now offering explosion-proof induction motors in the W22Xd series. This includes all motors over the full stated power range, which conform to the IE classification standards, up to and including energy efficiency class IE4. Special applications – including explosion-proof motors – are currently exempt from the motor efficiency regulations and this series, which combines reliable explosion protection with maximum efficiency, is now one of the most energy efficient series available on the market
“Particularly in energy-intensive industries such as chemical, oil/gas or mining, where very large facilities with, in some cases, thousands of motors often operating 24/7, energy efficiency is a decisive factor for reducing operating costs and CO2 emissions”, says Detlef Wortmann, business development manager at WEG.
“Energy costs for electric motors account for 95 to 97 per cent of total life cycle costs, depending on the application. This means that investments in energy-efficient drives usually have a very short return on investment. Thanks to the low operating costs, companies with explosion-proof motors in the W22Xd series can reduce their costs by 20 to 40 per cent compared to conventional approaches.”
To make this energy-saving drive solution available for hazardous areas, WEG utilised the innovative housing design of the W22 standard induction motors.The W22Xd housing design features an advanced cooling system with an aerodynamic concept that both reduces noise levels and significantly improves heat dissipation. The sturdy housing with integrated mounting feet, allows the explosion-proof motors to be deployed in even the most demanding applications and minimises both vibration and noise emissions.
Multi-turn encoder
Sensata Technologies has launched what is reported to be the first explosion proof stackable multi-turn encoder for use in oil and gas applications.
The new encoder, BEI Sensors’model MAAX, is ATEX and IECEx certified to operate in explosive environments and features a Profibus output in a bespoke, stackable package. CANopen and SSI outputs are also available. The MAAX provides up to 16 bits of resolution as well as up to 16 bits of turns by mechanical counting. The product operates directly in Zone 1 environments without the need for an accompanying Intrinsic Safety barrier.
Absolute multi-turn encoders like the MAAX are the ideal position sensing solution for oil and gas applications such as Drawworks, top drives and pipe handling equipment where working conditions are extreme. The stackable and explosion proof design makes for a simple installation wherever encoders are mounted in tandem to provide multiple signals for redundancy or when data sharing is desired. The Profibus interface simplifies system set up as it allows for daisy chaining products together without the need for running a control cable from the panel to each individual component.
- Shuttles or stackers?
- One-in one-out system for red tape confirmed
- World first for additive aerospace manufacturing
- Mental health warning signs employers need to look out for
- Leading the way for the mobile robot takeover
- Rapid fan maintenance for bakery
- A driving force for quality control
- Questar demonstrates predictive maintenance solution
- INEOS paves way for shale gas development
- Assessing the order of events
- No related articles listed