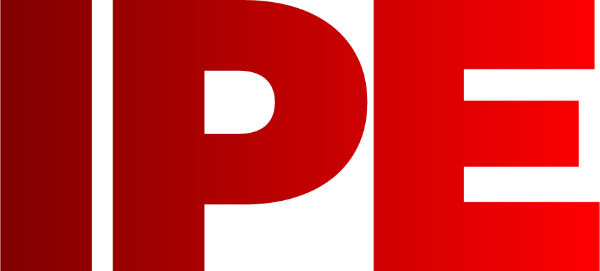
![]() |
Edward Lowton
Editor |
![]() ![]() |
Home> | Production Engineering | >Welding | >Quality as the burning issue |
Quality as the burning issue
12 February 2024
Hot active plasma technology has helped Audi significantly reduce cleaning costs where metal sheets have to be prepared for stud welding

AUTO MANUFACTURER Audi has been using Acerios hot active plasma technology from Fronius on thin aluminum body parts for the last two years. Acerios has substantially reduced cleaning costs in those areas where metal sheets have to be prepared for stud welding.
"In the worst case, the failure of a ground stud connection can bring a vehicle to a complete stop," said engineer Daniel Rudolph, technology developer responsible for joining and lightweight construction at Audi AG. "In building the Audi A8, we fit numerous ground studs and have to make sure that every single one is perfectly connected. We go to great lengths to meet the quality requirements."
This is because the quality of every stud weld critically depends several factors, including the surface characteristics. Contamination by drawing oils and dry lubricants - as used in metal forming - can lead to a defective joint.
Clean flash unsuitable on thin sheets
The problem of contamination can often be solved with the stud welding unit itself. This involves supplying a burst of current (clean flash) upstream of the actual welding process, which cleans the welding surface. However, this approach is not practicable for aluminum sheets less than 2 mm thick, as the heat input is too high and the sheet would burn through during the welding process. Other problems include the fact that pores can occur with this process, which negatively affect the weld seam quality.
One such part at Audi is the bulkhead of the Audi A8. This is made of aluminum sheet alloy (6xxx) and is only 1.5 mm thick at those points where ground studs are welded: "In the first few years after series production began, the whole part had to be chemically cleaned and pickled, which was both time-consuming and expensive," explained Rudolph. "That was the only way we could definitely guarantee the requisite 100% quality of the stud welded joint."
In 2017, Audi was about to build a new production line for the fifth generation A8. It wanted to find a way around the complex chemical cleaning process. Fronius’ hot-active plasma (HAP) technology offered a possible solution.
Local cleaning with plasma is the solution
Treating surfaces with Acerios hot active plasma (HAP) technology from Fronius has many advantages. Using a stream of shielding gas, the arc plasma is formed into a flame with a core temperature of up to 1,000° Celsius. This triggers thermal and chemical processes which ensure that material surfaces are locally cleaned of organic residues and film impurities with pinpoint accuracy. At the same time, the surface is activated. With Acerios, the arc is created between the plasma nozzle and the tungsten electrode of the welding torch, which means that a ground earth connection to the workpiece is not required. As a result, non-metallic materials can also be cleaned with hot active plasma.
The technicians responsible for the A8 line finally decided to use Acerios in a robot cell that had enough free downtime to clean two areas measuring 12 sq cm each. "This meant the available time was even sufficient to increase the Acerios burning duration to six seconds per welding spot. As a result, the distance between the welding torch and the workpiece is 30 mm. And we can then lower the current to 120 A without any loss of cleaning effect," stated Jürgen Kolbenschlag, welding expert from the A8 body shop.
"This saves on wearing parts," which Audi initially replaced after 10,000 cleaning points. It became apparent that the wear limits were far from being reached. The replacement cycle was therefore continually extended. By the middle of 2021, the wearing part limit had still not been reached - despite 25,000 cleaning points having been set.
For more information:
Tel: +43 7242 241 0
- CMT upgrade for TPS/i Robotics power source
- Date set for 'Open House'
- Added functionality
- Cool & gentle charging
- Customised data documentation
- Charge cooler, drive further
- Fronius UK to host Back to the Future of Welding event
- Charger collaboration
- Love at second sight
- Supermarket chain chooses charging technology