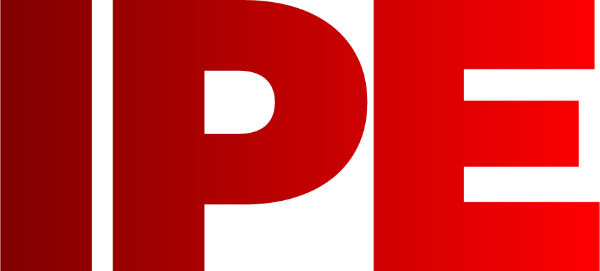
![]() |
Edward Lowton
Editor |
![]() ![]() |
Home> | Handling and Storing | >Batteries and chargers | >Charger collaboration |
Home> | Handbooks | >IPE Ireland | >Charger collaboration |
Charger collaboration
01 July 2016
For the past two years, car maker Audi has employed chargers made by Austrian specialist Fronius to charge the traction batteries used in its 2,000 electrically powered forklift trucks at its headquarters in Ingolstadt in Bavaria.

Thanks to their innovative Ri charging process, as well as extending the service life of the batteries the chargers are said to reduce power consumption and CO2 emissions, helping Audi to meet its target of reducing emmissions by 25% by 2018.
Audi and Fronius have been working together for several years, explains Logistics planner Ferstl: “Fronius approached us when they began developing the new chargers to see if we would be interested in collaborating with them. This gave us the opportunity to put our own ideas and requirements on the table and incorporate them into the design process.”
During the Ri charging process the charging current and voltage do not follow a fixed characteristic, but reflect the internal resistance (Ri) of the battery, which in turn depends on its age, temperature and state of charge. This makes every charging cycle unique meaning energy loss is much lower and warming of the battery is kept to a minimum.
- Switch between filler wires on the torch
- Battery-powered system for mobile welding
- Platform for advancements
- Open house announced
- Fit for the future with smart robot welding technology
- Battery charging modernised
- Cool & gentle charging
- Efficient weld properties for MIG/MAG, TIG and MMA tasks
- CMT upgrade for TPS/i Robotics power source
- Charging technology boost battery availability