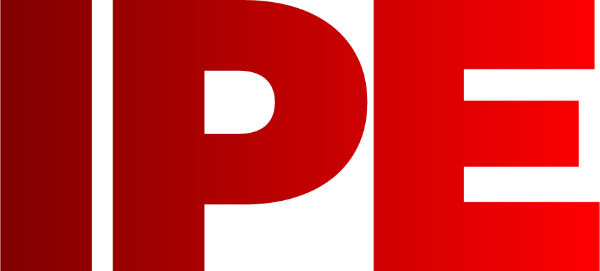
![]() |
Edward Lowton
Editor |
![]() ![]() |
Home> | Efficient Maintenance | >Thermography | >The key to effective maintenance strategy |
Home> | Efficient Maintenance | >Vibration monitoring | >The key to effective maintenance strategy |
The key to effective maintenance strategy
04 January 2023
Forward-thinking organisations do not want to be in a reactive maintenance cycle, and more maintenance professionals are now recognising the value of a proactive approach - rewarding prevention of the maintenance issue rather than the reactive hero, explains Gary Harvey

WHILE THERE are an array of digital technologies that can be deployed to assist in predictive maintenance, there are also some key elements such as periodic condition monitoring that are fundamental to a successful maintenance strategy and can still play their part for many organisations at the intermediate stage of maintenance maturity.
Employing condition monitoring tactics can help reduce plant downtime by around 40%, extend asset life by 30%, and halve maintenance spend and machine failures - so can you afford not to implement them?
Vibration analysis plays a vital role
Vibration analysis is a vital element of condition monitoring which helps in the detection of potential machine failure or component demise, allowing engineers to replace or repair machinery or parts before breakdown - thus avoiding downtime and extending asset life by negating further damage as a result of the malfunctioning or deteriorated part.
Regular vibration monitoring and analysis will help in the identification of unusual vibration activity which may signal the imminent failure of that part, so it really should be a part of the predictive maintenance strategy for any manufacturing operation.
Vibration analysis can be used to determine the health of bearings, identify misalignment of components or machine imbalances – as well as detect issues such as loose bolts or fasteners that are easy to address, but which can cause equipment failure if left.
Devices such as wireless vibration sensors are a great way to capture data, are easy to install and can send data to dashboards on relevant software platforms that can do the analysis for you.
But increasingly, many organisations are opting for solutions providers to carry out this element of condition monitoring for them, removing the responsibility and hassle of in-house vibration analysis equipment training. Outsourcing offers peace of mind that machine monitoring is being handled, allowing plant operators to get on with other business critical tasks.
Oil condition monitoring is also key in maximising equipment life and warning of potential faults. Oil degradation contamination and wear products all give useful information about oil and machine health, and this is why oil monitoring should not be side-lined.
Thermal imaging helps prevent failures
Using thermal imaging technology to help detect heat fluctuation which can signal imminent equipment failure has been a tried and tested maintenance tactic for decades - and the technology continues to evolve to become easier to handle and use. There is even now a trend for this technology to be being built into other instruments or be attached to everyday devices such as smartphones - making the technology ever more accessible.
However, with energy efficiency being a key environmental consideration - coupled now with a major financial consideration as the cost of energy soars - thermal imaging also has a part to play in energy saving.
Thermal imaging technology can be used to identify where equipment is getting hot (signalling both imminent failure and potential overuse of energy), and help fine-tune processes to optimise the line, thus minimising energy consumption. At a time when energy prices are only going one way, and there’s no sign of an energy price cap for businesses, this is a condition monitoring element with many benefits.
There is a growing cohort of organisations turning to managed solutions to get their maintenance programmes up and running - or take them to the next level. Whether you're one of these organisations turning to solutions providers, or you want to be self-sufficient in these activities, ensuring that the equipment or services being used deliver best practice is a factor not to be underestimated.
Gary Harvey leads the Field Services team for RS’ Maintenance Solutions
For more information:
Tel: 03457 201201
- Digitisation of the end-to-end maintenance supply chain
- Automation & control portfolio
- Reinforcing support for maintenance engineers
- RS releases Industry In Motion 2023 Maintenance Engineering Report
- Reaping the benefits of the evolution of sensor technology
- Unlocking dormant data improve maintenance decision-making
- Lockout equipment
- DesignSpark Mechanical launches
- Effective energy management holds infinite benefits for industrial operators
- RS releases Performance in Focus 2024 Maintenance Engineering Report in partnership with IMechE