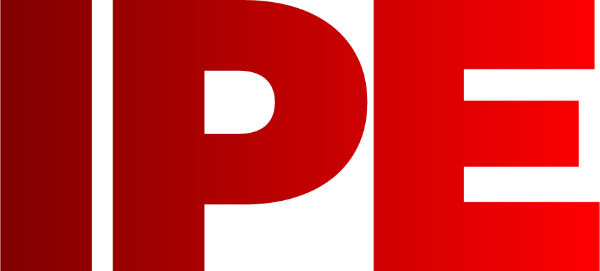
![]() |
Edward Lowton
Editor |
![]() ![]() |
Home> | Production Engineering | >Machine Shop Equipment | >5-axis productivity flows for Rivercircle |
5-axis productivity flows for Rivercircle
01 August 2024
Since the purchase of its first 5-axis machine almost five years ago, Rivercircle been impressed by the efficiency advantages

PETERBOROUGH-BASED special-purpose machinery manufacturer Rivercircle has invested in two AXILE G8 5-axis machining centres, available in the UK and Ireland from the Engineering Technology Group (ETG). Rivercircle installed its first AXILE G8 in 2021 with the second machine arriving in September last year.
The company is also heavily involved in the toolmaking industry for automotive, pharmaceutical and medical applications. It is the machining of pre-hardened tool steel and larger components in this department of the business that has brought the addition of the two AXILE G8 machining centres.
"We bought our first 5-axis machine about five years ago," said Jonathan Theobalds, MD at Rivercircle. "We were one of those companies that has had 3-axis CNCs for many years and we had been to all the shows and looked rather enviously at the 5-axis machines, but we couldn’t see one at a price point for us. Eventually we dived in with our first one and then almost surprising to us, 18 months later we introduced a second machine.
Covering both 5- and 3-axis work
“The initial foray into 5-axis machines was a big leap for us but we very quickly learnt that actually having a 5-axis machine doesn’t mean that you have to have 5-axis work on the machine all of the time. Our traditional 3-axis work can be done more efficiently and effectively on a 5-axis machine," Theobalds continued.
"The important thing for our business regarding the selection of the machine was we needed something with power, strength and rigidity. We are machining hardened and pre-hardened tool steel, so we need that capability to get a lot of metal removal quickly at the beginning and then move into the fine delicate cavity work."
Turning to one of the big advantages of investing in the AXILE G8 machine, Theobalds stated: "With a 5-axis machine you are not doing multiple setups, so if we can strap the billet to the machine once and do all the heavy-duty coring-out work and then use the same machine for the delicate finishing, there is a huge efficiency advantage for us there. When we selected our original 5-axis, this gantry construction was very important. This gives us strength and rigidity and we are not compromising surface finishes on fine machining or cycle times on heavy cutting."
Capacity is key
The move from a previous manufacturer to the AXILE brand was down to capacity - as very few machines can match the versatility, flexibility and speed of the AXILE G8 whilst holding up to 1350kg on the bed. The smaller 5-axis machines have a capacity limit in the realms of 650kg, half the billet size that can be held in the AXILE G8.
"As machine builders ourselves, we really appreciate how the AXILE machines are built. The Y-axis has twin spindles and twin drives the tilting B-axis has a motor on each side - it’s not just driven from one side," Theobalds concluded. "This gives the machine excellent rigidity and accuracy. Furthermore, the AXILE has a powerful spindle with 20,000rpm and high pressure through spindle coolant. This allows both heavy-duty roughing and high-speed finish machining."
For more information:
Tel: +44 (0) 1926 818 418
- Twice the output
- Transitioning from manual to CNC machining
- UK welcomes Nakamura-Tone turning centre
- Reduce machine tool buying risk
- Mitsubishi sparks productivity gains for Go Tools
- Fifth Nakamura powers productivity at Velden
- On track for record year
- Making the fastest….faster!
- ETG to present fastest Nakamura yet at EMO
- Showroom success
- Driving additive manufacturing forward
- Protecting workers from fumes and dust
- Mobile laser hardening robot helps boost efficiency
- Reusable industrial clamp
- Devices for TIG welding added
- Daylight quality lighting
- Thin film conversion coatings
- 3D printing used for Kew's dragons
- Tool order
- Customised blast cabinet upgrades armature repair