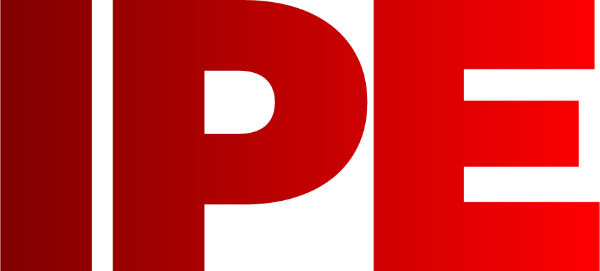
![]() |
Edward Lowton
Editor |
![]() ![]() |
Home> | Efficient Maintenance | >Condition monitoring | >Getting started with condition-based maintenance |
Getting started with condition-based maintenance
07 February 2025
By leveraging real-time data and targeted monitoring techniques, Condition-Based Maintenance enables proactive decisions that reduce downtime, cut costs, and enhance asset reliability, says Amber Hart

MAINTENANCE IS often seen as a necessary expense, but Condition-Based Maintenance (CBM) offers a way to turn it into a strategic advantage. By using real-time data to drive maintenance decisions, CBM focuses on actual asset health - preventing issues before they disrupt operations and reducing overall costs. If you’re ready to make maintenance a proactive part of your strategy, here’s how to begin.
1. Pinpoint the Right Assets to Monitor
Effective CBM starts with identifying your most critical assets - equipment whose failure would most impact production or incur high repair costs. Focusing on these high-priority assets ensures that your resources are invested where they’ll bring the best return. Review past maintenance data and failure patterns to target assets that will benefit most from CBM.
2. Choose the Best Monitoring Techniques
Different assets require tailored monitoring techniques to detect early signs of failure:
- Vibration Analysis: Ideal for rotating machinery, this technique reveals imbalances, misalignments, and bearing issues.
- Temperature Monitoring: High temperatures in bearings, motors, and electrical components often indicate wear. Infrared thermography or sensors can detect overheating before it escalates.
- Pressure Monitoring: Essential for hydraulic and pneumatic systems, pressure sensors identify leaks, blockages, or performance issues.
- Oil Analysis: Lubrication quality can signal early signs of wear or contamination, allowing timely intervention.
By applying the appropriate monitoring techniques to each asset, CBM captures the most relevant data to inform maintenance actions.
3. Integrate Data with a CMMS
To make the most of your condition data, a Computerised Maintenance Management System (CMMS) is essential. SSG Insight’s Agility CMMS, for example, centralises data and makes it actionable for maintenance teams:
- Automated Alerts: Pre-set thresholds trigger alerts, enabling maintenance teams to respond promptly.
- Condition-Based Scheduling: Rather than servicing assets on a fixed schedule, maintenance is scheduled only as needed, optimising resource use.
- Trend Analysis: Historical data stored in the CMMS supports predictive insights, helping teams identify patterns and make data-driven decisions about asset health.
4. Set Baselines and Thresholds
Collecting data is only the beginning; establishing baselines and acceptable thresholds for parameters like vibration, temperature, pressure, and oil quality is essential. Historical data and manufacturer guidelines help define these thresholds, allowing you to turn data into actionable insights.
5. Start Small and Train Your Team
Begin with a pilot program focused on a few key assets to demonstrate CBM’s value and refine practices before a broader rollout. Training ensures the maintenance team understands condition data, responds to alerts effectively, and integrates CBM into daily routines.
Conclusion
Condition-Based Maintenance shifts your organisation from reactive repairs to a proactive, data-driven approach. By focusing on critical assets, selecting the right monitoring techniques, and integrating with a robust CMMS, CBM helps you optimise maintenance, minimise downtime, and make asset reliability a competitive advantage.
Amber Hart is head of new business at SSG Insight
For more information:
Tel: +44(0) 1924 200344
- Webinar program
- Do you need to maximise production uptime and get the best performance from your assets?
- Software firm confirms event partnership for Maintec 2019
- Growth Plan4 SoftSols
- Agility Health Check
- SSG Insight releases Agility9 smart dashboard
- Seamless end-to-end solution
- Affordable flexible maintenance management with Agility
- Ready for 4.0
- Dynamic map & drawing overlay