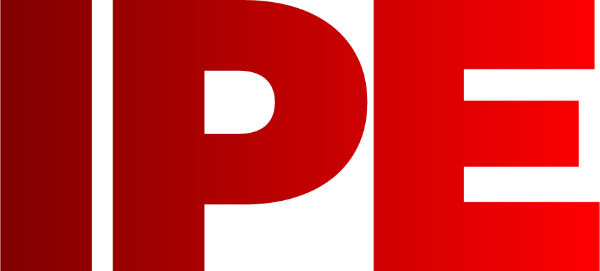
![]() |
Edward Lowton
Editor |
![]() ![]() |
Home> | Efficient Maintenance | >Thermography | >Enhancing efficiency with thermography and acoustic imaging |
Enhancing efficiency with thermography and acoustic imaging
07 October 2024
Identifying potential issues before they escalate into costly problems is crucial, and both thermography and acoustic imaging have a key role to play, says Jason Cargill

AS UK industry gets to grips the challenge of rising energy costs, it’s worth reiterating the important role of thermography and acoustic imaging in the maintenance process.
Thermography enables early detection of equipment issues, identifying potential faults such as overheating components, electrical or insulation problems, and preventing costly breakdowns and downtime.
Acoustic imaging can swiftly pinpoint compressed air and gas leaks in industrial settings, facilitating rapid diagnosis and repair, helping prevent energy waste and enhancing operational efficiency.
"The world has changed significantly in recent years. Reducing energy costs is at the forefront of everyone’s mind right now," said Jason Cargill, technical sales specialist at Teledyne FLIR.
"We’re in a very different business context now. People have to be even more careful with their investments, and, reflecting this, it’s important to highlight the ROI associated with our solutions."
Reducing costs and avoiding downtime
One example of this is the new FLIR Si2 Pro. Since its launch in March, the industrial acoustic imaging camera has "generated a lot of interest" at trade expos, Cargill reports.
"Leaks in compressed air and vacuum systems can lead to considerable costs, together with operational disruptions, but detecting them can be challenging," he explained. "This is where an acoustic imaging camera like the FLIR Si2 Pro is ideal, allowing businesses to proactively detect leaks and avoid unnecessary downtime."
One of the standout features of the FLIR Si2 Pro is its ability to quantify different types of gas, including compressed air, CO2, helium, ammonium, methane, hydrogen, argon, and natural gas.
"Gases used in the production process can represent a significant expense for businesses, so tackling leaks can have a positive impact on their bottom line," Cargill added.
Additionally, repairing leaks can help increase the equipment lifespan. "Leaks mean that you have to increase the output of your compressed air machinery to produce enough air for your system. This leads to a scenario where the machinery is overworked, reducing its service life," he added. "Our solutions help reduce energy costs, but there are also cost savings through reducing wear on equipment."
Improving efficiency
Teledyne FLIR's software solutions can also play an important role in helping to improve the overall efficiency of maintenance processes, while mitigating human error.
Cargill highlights FLIR Route Creator which allows users to upload a pre-planned route with a list of the assets they need to inspect at each location to their camera.
"The camera can be given to a maintenance technician and they just need to follow the instructions on the screen,” he stated. "The camera will offer on-screen text to guide the user to the next asset or inspection point to be inspected."
Meanwhile, the Reference Imaging function allows users to utilise images from previous inspections to ensure consistency over time.
"With thermography, it’s important to try and replicate the conditions from previous inspections," Cargill observed. "Reference Imaging allows you to overlay a ghost image from the previous inspection onto your new image making the process much more straightforward, helping the user to maintain a similar distance and position to that with which the previous image was captured."
For more information:
- High performance thermal camera
- New portable PS DUO from Teledyne GFD detects two gases simultaneously
- At a lower price
- Machine vision USB3 camera features Sony Pregius S sensor
- Thermal camera includes inspection route software
- Enhanced images
- Advanced features at entry level
- Streamlines thermal image analysis
- Detecting defects on solar cells
- Education discount package