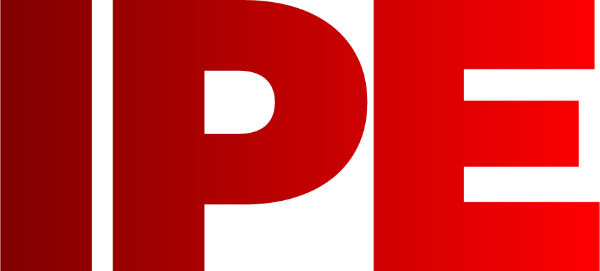
![]() |
Edward Lowton
Editor |
![]() ![]() |
Home> | Plant, Process & Control | >Compressors and ancillary equipment | >Compressed air cleaning: reaching ISO 8573 |
Compressed air cleaning: reaching ISO 8573
02 February 2022
Contaminated air can cause machinery failure and can present a health risk to workers and consumers alike. Purification to ISO 8573 is required, writes Steve Smith

THE PROBLEM is simple: contaminated compressed air can cost companies thousands of pounds each year. Over time compressed air equipment becomes gummed up with a corrosive mixture of dirt, oil and water. But where does it come from?
Your compressor is its own contaminator: a 236 l/s (500 cfm) compressor, running 24 hours a day, produces 327 litres of water (72 gallons) every day. In Britain, the average humidity is 50% to 80%. Pump British air through a system for long enough and you’ll soon be picking up lots of water (not to mention the water that gets into plants from rain-sodden boots, dripping jackets and saturated umbrellas).
Then there’s dust. It’s everywhere. There is no getting away from dust anywhere outside the cleanest medical or microchip manufacturing cells. In the countryside you’ll find an average concentration of dust to air-volume of 15 mg/m3 (going up to 50 mg/m3). In the city it averages 30mg/m3 (going up to 100 mg/m3). In industrial areas, as you might expect, this rockets to an average of 100 mg/m3 (going up to 500 mg/m3). And in large plants you’re looking at an average of 200 mg/m3 (going up to 900 mg/m3).
That’s what’s happening in the air but the story of concentration inside compressors is even worse: dust, industrial pollution, and natural entities such as pollen, bacteria and viruses, can be multiplied by a factor of eight compared with atmospheric contamination. If you were in a facility with 140 million particles of dust/m3 then your compressed air contamination will be running at 1,120 million particles of dust/m3.
Eliminating the contaminants
Compressed air is treated by filtration and drying (with different methods including refrigeration air drying, adsorption drying and membrane drying). High efficiency filters can remove up to 99.99999% of bulk water and oil. That’s a lot of decimal places but it’s not some throwaway slogan on the side of a bottle of bleach, each decimal point has a significant story to tell. If you have 140 million contaminant particles, at 99.9999% filter efficiency, you are still left with 140 contaminant particles (see chart). As we have become increasingly aware over the last two years: microscopic particles in miniscule concentrations can cause worldwide disruption, destruction and death. Decimal points matter.
Refrigerant air dryers work by drying air to a pressure dew point of +3C. Adsorption dryers take this dew point down to as much as -70C – moist air is dried as it flows over a hyrgroscopic substrate (silica gel, for instance) which becomes saturated with adsorbed water.
Finally, membrane dryers are used for “point of use” dehydration of compressed air (and, because the membrane dryer is not oxygen depleting, it is also excellent for breathing air application). Air from the compressor and receiver is passed through a centrifugal separator and 0.01 micron filter before reaching the membrane dryer, which has a pressure duew point of +7C. Membrane dryers are typically used for analytical equipment, in paint and bodyshops, for medical or dental air or in pneumatics and robotics.
Getting the right information
Filtering and drying compressed air isn’t just about saving money on machine maintenance and preventing factory downtime. It’s a legal obligation if we’re to meet ISO8373 – The Air Quality Standard. Handy information can be found at the British Compressed Air Society (BCAS) website (www.bcas.org.uk) where you will find Best Practice Guide 104 “The Filtration and Drying of Compressed Air”. The standard itself, ISO 8573.1:2010 – to give it its full designation – was compiled by various international industry associations and bodies, including BCAS.
Steve Smith is managing director of HiLine Industries
www.hilineindustries.com
01283 533 377
- Plug & play dryers
- Condensate cleaners ensure full legal compliance
- Hi-Line Tundra Dryers Even More Efficient
- Energy-efficient compressed-air drying
- Hi-line boosts environmental credentials with switch to R513a
- On-site N2/02 generation
- Zero ozone depleting potential with Tundra refrigerant air dryers
- Digital dewpoint display
- Zero loss desiccant air dryers
- Heatless pressure swing dryers
- MAT - Modular Air Trolley
- Belt drive compressors
- Monitors compressors
- Plugging the skills gap
- Compressor range
- Modular dryer design
- Accurate diagnosis
- Plant complies with latest medical standards
- Hertz Kompressoren UK launches HSC D direct drive air compressor range
- Filter elements tested to ensure air quality