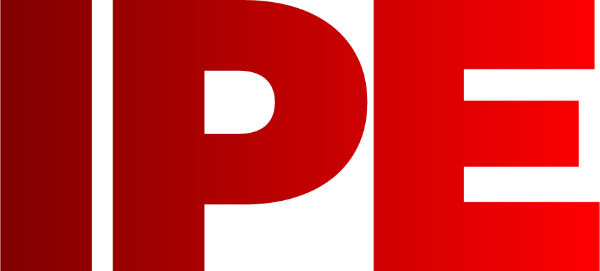
![]() |
Edward Lowton
Editor |
![]() ![]() |
Home> | Plant, Process & Control | >Pumps | >Pumps succeed in battle against blockages |
Pumps succeed in battle against blockages
06 December 2018
Non-flushable items continue to cause waste water companies immense problems with sewerage systems becoming inundated with laminations of wipes combined with fats and greases. The man hours and costs associated with manually lifting pumps and clearing the blockages has been known to total £10million.
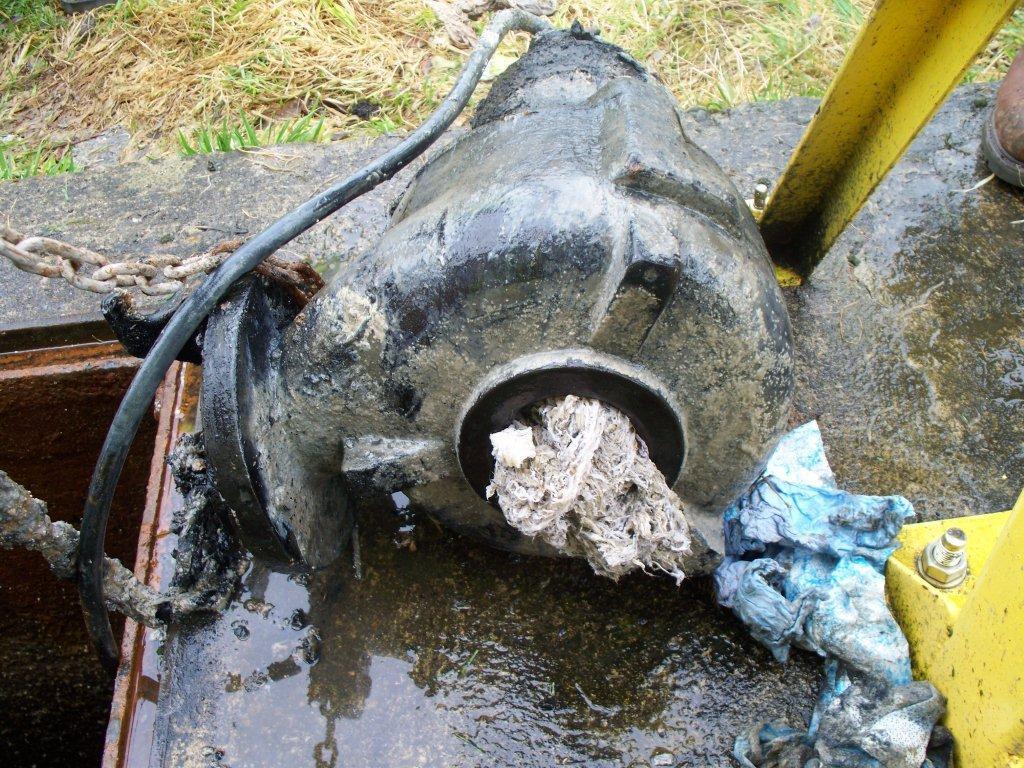
Non-flushable items continue to cause waste water companies immense problems with sewerage systems becoming inundated with laminations of wipes combined with fats and greases. The man hours and costs associated with manually lifting pumps and clearing the blockages are eye-watering. For example in one region alone North West Water, the costs have been estimated at around £10m per year.
Through their experiences with a number of the UK’s water companies in dealing with blocked sewers, Huntingdon based P&M Pumps the UK distributor for Vaughan Chopper Pumps, has succeeded in providing a solution by replacing failing submersible pumps.
For example, at Anglian Water’s pumping station in Cambourne two Vaughan 30kW / 1460rpm SE6W chopper pumps were specified to handle flows up to 400m3/hr at heads of 17.8. A simple and quick retro fit was all that was required utilising all the existing installation hardware and this provided an effective solution to prevent blockages and instances of drains ‘backing-up’.
The innovative design of the Vaughan Chopper pump makes it particularly effective in the most challenging solids pumping applications that cause other solids handling pumps to fail when faced with the challenge of non-flushable items. The seal design on Vaughan submersibles has proven to be reliable and durable assisted by the patented upper cutter design. Stray solids that may be trapped within the mechanical seal chamber are shredded and removed by the impeller pump out vanes turning against the upper cutter.
In addition, solids are then chopped by the cupped and sharpened impeller blades turning across the cutter bar, creating a smooth ‘slicing effect’ enabling the conditioned slurry to be easily pumped upstream through the piping system without plugging.
Finally, a centered nut with a tooth cuts stringy materials that tend to wrap at the pump inlet and where non-fibrous hard solids are present there is the option for a (removable) disintegrator tool which agitates and breaks up large solids to prevent suction blockage.
- Health Check Package offered
- Achilles UVDB membership
- Chopper pumps handle lab waste
- Mixing in some savings
- Pumps take no prisoners at hmp peterborough
- Pumps meet challenge of corrosives
- 'Shop window' for pump firm
- Chopper pumps
- Vaughan chopper pumps offer a solid solution
- Mixing to maximise anaerobic digestion process