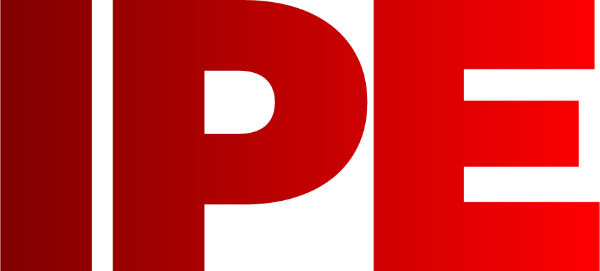
![]() |
Edward Lowton
Editor |
![]() ![]() |
Home> | Plant, Process & Control | >Pneumatic equipment | >Drain your condensate, not your air |
ARTICLE
Drain your condensate, not your air
25 January 2013
To understand the scale of the problem, a typical 170m3/hr (100 cfm) screw compressor operating for 4,000 hours at normal European ambient temperatures will produce and pour around 10,000 litres (2,200 gallons) of damaging oily, acidic compressor condensate into the system.
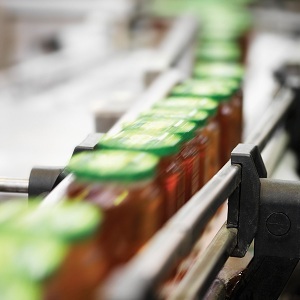
To understand the scale of the problem, a typical 170m3/hr (100 cfm) screw compressor operating for 4,000 hours at normal European ambient temperatures will produce and pour around 10,000 litres (2,200 gallons) of damaging oily, acidic compressor condensate into the system.
Condensate drains are used to remove this liquid; however, escaping air from inefficient or partially open drains is often the biggest single source of wasted energy in a compressed air system. For example, a system using a single timed drain could lose approximately 3.7m3/hr (2.18cfm) of air. Over a full year of continuous operation this equates to an air loss of approximately 32,498m3 (1,142,669ft3).
In energy terms, this drain would consume 3,581KW of energy every year.
The cost effective solution to these problems are the Parker ED3000 series “zero air loss†condensate drains that have been designed to eliminate this form of energy wastage.
Additionally, the oily, acidic condensate removed from the compressed air system needs to be disposed of in a legal and responsible manner.
Parker ES2000 series oil/water separators effectively reduce the oil concentration to legally permitted levels. This allows the larger volume, up to 99.9% of the total condensate to be safely discharged to your drains, leaving only a small amount of oil to be disposed of legitimately and economically.
Condensate drains are used to remove this liquid; however, escaping air from inefficient or partially open drains is often the biggest single source of wasted energy in a compressed air system. For example, a system using a single timed drain could lose approximately 3.7m3/hr (2.18cfm) of air. Over a full year of continuous operation this equates to an air loss of approximately 32,498m3 (1,142,669ft3).
In energy terms, this drain would consume 3,581KW of energy every year.
The cost effective solution to these problems are the Parker ED3000 series “zero air loss†condensate drains that have been designed to eliminate this form of energy wastage.
Additionally, the oily, acidic condensate removed from the compressed air system needs to be disposed of in a legal and responsible manner.
Parker ES2000 series oil/water separators effectively reduce the oil concentration to legally permitted levels. This allows the larger volume, up to 99.9% of the total condensate to be safely discharged to your drains, leaving only a small amount of oil to be disposed of legitimately and economically.
Related articles
MORE FROM THIS COMPANY
- Annual filter element replacement is vital
- Compressed air drying solutions for every application
- The OIL-Xplus ADVANTAGE – taking energy saving to the next level
- Queen's Award
- Energy savings promised
- Can high performance air dryers be environmentally friendly?
- Effective compressed air filters are vital for machine performance
- Escaping air:Major drain on resources
- Easy access to effective compressed air treatment solutions for rail operators
- Energy saving
OTHER ARTICLES IN THIS SECTION