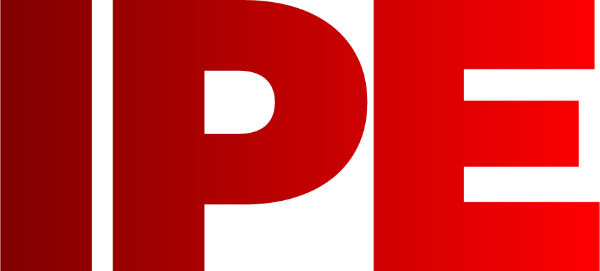
![]() |
Edward Lowton
Editor |
![]() ![]() |
Home> | Energy Management | >Compressors & ancillary equipment | >Keep control of the fourth utility |
ARTICLE
Keep control of the fourth utility
25 January 2013
It is often wrongly assumed that compressed air is a free source of power; the reality, of course, is that the only air that is free is the air that we breathe. Here, Malcolm Crossley, sales manager - Air Treatment, Parker
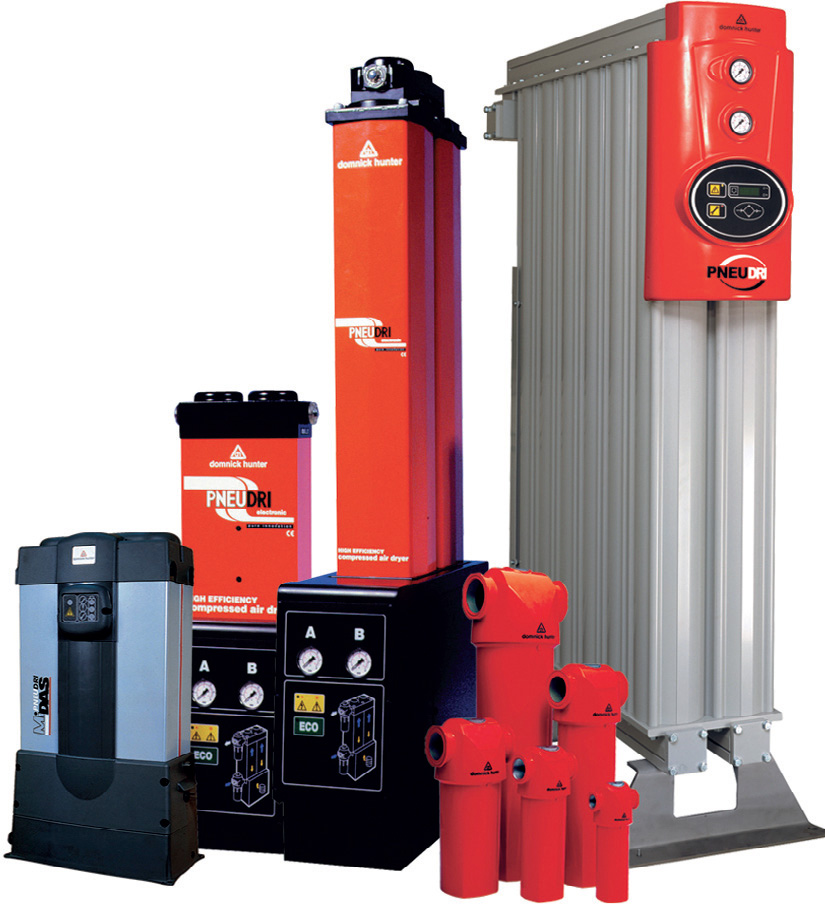
It is often wrongly assumed that compressed air is a free
source of power; the reality, of course, is that the only air
that is free is the air that we breathe. Here, Malcolm
Crossley, sales manager - Air Treatment, Parker Sales UK -
offers some simple guidance on energy saving
Outlined below are some of the key areas on which to focus to ensure that a compressed air system is operating as efficiently as possible.
Leaks A major contributing factor to energy wastage in compressed air systems is air leakage. According to the Carbon Trust 'an average leak rate for a well maintained system should be around 5 to 10% of air generated to leakage. However it is noted that in unmanaged systems it can be as much as 40 to 50% of the generated output'.
Leaks can occur in multiple places. A quick win for maintenance personnel is to simply walk the line and listen. Look for leaks in obvious areas such as:
Pipework Fittings, flanges and manifolds Hoses, couplings and tubing Worn out system components. Misaligned tubing
Maintain system components for leak free operation. Look for worn out seals on cylinders and valves. Use the spares kits that most manufacturers supply and change the seals on system components as part of routine action. With new installations, specify manufacturers who are placing the emphasis on developing system components with the latest seal technology to reduce leaks.
In line filters In any compressed air system one of the key factors in reducing energy demands is effective filtration. In line filters essentially protect system components from contaminants in the airline. This ensures optimum machine uptime due to less frequent breakdowns. However with filtration there are factors that need to be considered to ensure energy efficiency: Specify the right size filter: If the filter unit is too small for the airflow required then the pressure drop would be greater, thus energy costs will be higher.
Specify the right level of filter: Examine your application, what level of filtration do your system components require? Install a filter that matches those specification requirements.
Proactively maintain filters: While performing the job that they are intended to do, filter elements will become clogged with contaminants. This means pressure loss. In too many situations operators simply turn up the pressure via a regulator.
However this is a wasteful use of energy; on average filters should be changed every 12 months.
Energy efficient dryers Dryers are often installed in compressed air systems to minimise problems of corrosion and microbiological growth created by water vapour in the air stream. This is especially important if high quality air is required, for example, in food or pharmaceutical manufacturing. Dryers can use large amounts of energy (especially if they are poorly maintained). Indeed, drying costs can sometimes be 80% of total operational costs.
There are a number of different types of dryer available. One of the most efficient types uses adsorption technology. An adsorption, or desiccant dryer, consists of two desiccant filled chambers, one drying the air while the other is undergoing regeneration, with a small volume of dried air from the drying chamber being used as purge air. Recent systems, such as modular PNEUDRI desiccant air dryers from Parker, are now fitted with Dew point Dependent Switching (DDS). This effectively eliminates unnecessary desiccant regeneration cycles and ensures that energy consumed is directly proportional to the actual airflow, temperature and moisture loading - not the rated capacity of the dryer. This provides energy savings, which can be in excess of 60%.
Compressed Air pipework: In older airline installations galvanised steel is heavily used. An inherent problem with producing compressed air is that the compressor introduces water into the airline, thus causing rust and restricting air flow.
This causes the compressor to work harder to supply the extra flow needed.
In new installations and for retrofitting, aluminium pipe, that doesn't rust, is increasingly being considered. Aluminium can sometimes be seen as a more expensive alternative. However Parker has introduced a Transair energy efficiency calculator to show the over-time return on investment that its Transair pipe systems can deliver with respect to reduced energy costs.
By addressing the factors above, and with the implementation of a proper on-going planned and preventive maintenance programme, cost savings are achievable.
Outlined below are some of the key areas on which to focus to ensure that a compressed air system is operating as efficiently as possible.
Leaks A major contributing factor to energy wastage in compressed air systems is air leakage. According to the Carbon Trust 'an average leak rate for a well maintained system should be around 5 to 10% of air generated to leakage. However it is noted that in unmanaged systems it can be as much as 40 to 50% of the generated output'.
Leaks can occur in multiple places. A quick win for maintenance personnel is to simply walk the line and listen. Look for leaks in obvious areas such as:
Pipework Fittings, flanges and manifolds Hoses, couplings and tubing Worn out system components. Misaligned tubing
Maintain system components for leak free operation. Look for worn out seals on cylinders and valves. Use the spares kits that most manufacturers supply and change the seals on system components as part of routine action. With new installations, specify manufacturers who are placing the emphasis on developing system components with the latest seal technology to reduce leaks.
In line filters In any compressed air system one of the key factors in reducing energy demands is effective filtration. In line filters essentially protect system components from contaminants in the airline. This ensures optimum machine uptime due to less frequent breakdowns. However with filtration there are factors that need to be considered to ensure energy efficiency: Specify the right size filter: If the filter unit is too small for the airflow required then the pressure drop would be greater, thus energy costs will be higher.
Specify the right level of filter: Examine your application, what level of filtration do your system components require? Install a filter that matches those specification requirements.
Proactively maintain filters: While performing the job that they are intended to do, filter elements will become clogged with contaminants. This means pressure loss. In too many situations operators simply turn up the pressure via a regulator.
However this is a wasteful use of energy; on average filters should be changed every 12 months.
Energy efficient dryers Dryers are often installed in compressed air systems to minimise problems of corrosion and microbiological growth created by water vapour in the air stream. This is especially important if high quality air is required, for example, in food or pharmaceutical manufacturing. Dryers can use large amounts of energy (especially if they are poorly maintained). Indeed, drying costs can sometimes be 80% of total operational costs.
There are a number of different types of dryer available. One of the most efficient types uses adsorption technology. An adsorption, or desiccant dryer, consists of two desiccant filled chambers, one drying the air while the other is undergoing regeneration, with a small volume of dried air from the drying chamber being used as purge air. Recent systems, such as modular PNEUDRI desiccant air dryers from Parker, are now fitted with Dew point Dependent Switching (DDS). This effectively eliminates unnecessary desiccant regeneration cycles and ensures that energy consumed is directly proportional to the actual airflow, temperature and moisture loading - not the rated capacity of the dryer. This provides energy savings, which can be in excess of 60%.
Compressed Air pipework: In older airline installations galvanised steel is heavily used. An inherent problem with producing compressed air is that the compressor introduces water into the airline, thus causing rust and restricting air flow.
This causes the compressor to work harder to supply the extra flow needed.
In new installations and for retrofitting, aluminium pipe, that doesn't rust, is increasingly being considered. Aluminium can sometimes be seen as a more expensive alternative. However Parker has introduced a Transair energy efficiency calculator to show the over-time return on investment that its Transair pipe systems can deliver with respect to reduced energy costs.
By addressing the factors above, and with the implementation of a proper on-going planned and preventive maintenance programme, cost savings are achievable.
MORE FROM THIS COMPANY
- Parker releases high-performance automation controller based on IEC61131-3....
- Maintec: Boost productivity with Parker
- Free drive configuration software
- Simple alternative to PLCs
- Pneumatic solution for control valves
- Simple solutions secure savings
- Strategic collaboration
- Condition monitoring app
- VSD range extended
- Compact drive range extended
OTHER ARTICLES IN THIS SECTION