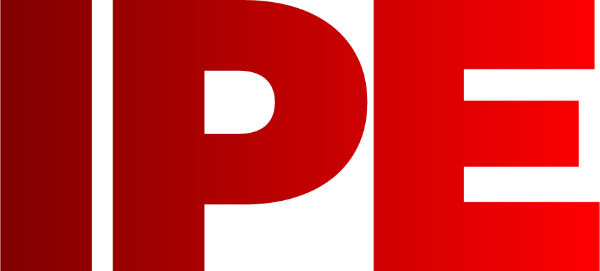
![]() |
Edward Lowton
Editor |
![]() ![]() |
Home> | Plant, Process & Control | >Seals and sealants | >Science behind seal selection |
ARTICLE
Science behind seal selection
04 March 2013
Correct seal geometry and materials selection allows engineers to specify highly effective sealing solutions into retrofit applications, not only ensuring continued operation but increasing efficiency and reliability, says Mick Holland, general manager of ERIKS Sealing Technology
Correct seal geometry and materials selection allows engineers to specify highly effective sealing solutions into retrofit applications, not only ensuring continued operation but increasing efficiency and reliability, says Mick Holland, general manager of ERIKS Sealing Technology
Seal durability is dependent on many factors and even the best components will deliver a shorter operating life than the components they protect, especially in harsh operating environments where temperatures and contamination run at high levels. However, continued innovation over recent years has delivered enhanced component design and material properties that are worthy of closer examination.
Application, thermo-chemical and mechanical criteria must be considered to ensure optimal selection when specifying a seal. Thermochemical criteria such as temperature and media govern material selection. Elastomers used as seal materials are typically compounds containing both the base polymer and many other ingredients that affect material properties either in use or manufacture. Additives in high performance modern lubricants and oils may result in chemical degradation of traditional sealing materials, for example leaching out plasticisers. Material compounds are continually developed to ensure reliable operation, in accordance with advances in other technologies.
Temperature is an important parameter when considering seal material, since each has its own optimum range.
Operating outside of that range can cause thermal stress that will harden an elastomer and cause it to crack — heat ageing is a more common cause of failure in nitrile rubber than wear. However, if the mechanical criteria allow, upgrading to a PTFE (polytetrafluoroethylene) seal can extend the thermal limit of a seal to meet such demands. PTFE is a thermoplastic with an operating temperature that typically ranges between - 70 and 200°C (and in some applications can reach 260°C). The high temperature resistance, wide compatibility with chemicals and low friction profile of PTFE has enabled the use of this material as a successful sealing material in many applications, including food and beverage, chemical, pharmaceutical, machinery and automotive.
Mechanical application criteria such as dynamic motion, pressures, surface finish, abrasion and geometry constraints may be mitigated through the use of correct seal geometry. For example, in rotary seals, where higher shaft speeds are exhibited, the permissible pressure differential across the seal becomes smaller.
Increased shaft speed produces greater frictional heat generation, but so too does pressure applied to the seal as more of the lip surface is forced against the shaft. Since too much friction can result in faster wear and shorter seal and shaft life, design variations that help offset these negative effects of higher shaft speeds need to be built into the seal. These design enhancements can include reducing the radial load of the seal lip, upgrading the sealing material to one that can handle higher temperatures, or optimising the shaft sealing surface.
To maintain high equipment availability, the use of appropriate seals is essential as a means of preventing leaks and defending machinery against the ingress of common contaminants such as dust and dirt. With a wide range of specialised seals now available, each with a unique set of features, understanding the function of a seal in any given application is essential if engineers are to increase the performance and extend the service life of industrial machinery, while also reducing maintenance costs in the process.
Once thermo-chemical and mechanical criteria have been satisfied engineers must still ensure regulatory compliance, such as FDA compliance in the food and pharmaceutical industries, demanding upto- date knowledge of elastomer and polymer specific legislation. To extract the full efficiency benefits that can be achieved by optimising a sealing system, it may be best to partner with an experienced seal supplier who understands and responds to challenges across industry. ERIKS, for example, can offer an unbiased service in matching the seal to the application and help you make the most of today's sealing solutions.
Seal durability is dependent on many factors and even the best components will deliver a shorter operating life than the components they protect, especially in harsh operating environments where temperatures and contamination run at high levels. However, continued innovation over recent years has delivered enhanced component design and material properties that are worthy of closer examination.
Application, thermo-chemical and mechanical criteria must be considered to ensure optimal selection when specifying a seal. Thermochemical criteria such as temperature and media govern material selection. Elastomers used as seal materials are typically compounds containing both the base polymer and many other ingredients that affect material properties either in use or manufacture. Additives in high performance modern lubricants and oils may result in chemical degradation of traditional sealing materials, for example leaching out plasticisers. Material compounds are continually developed to ensure reliable operation, in accordance with advances in other technologies.
Temperature is an important parameter when considering seal material, since each has its own optimum range.
Operating outside of that range can cause thermal stress that will harden an elastomer and cause it to crack — heat ageing is a more common cause of failure in nitrile rubber than wear. However, if the mechanical criteria allow, upgrading to a PTFE (polytetrafluoroethylene) seal can extend the thermal limit of a seal to meet such demands. PTFE is a thermoplastic with an operating temperature that typically ranges between - 70 and 200°C (and in some applications can reach 260°C). The high temperature resistance, wide compatibility with chemicals and low friction profile of PTFE has enabled the use of this material as a successful sealing material in many applications, including food and beverage, chemical, pharmaceutical, machinery and automotive.
Mechanical application criteria such as dynamic motion, pressures, surface finish, abrasion and geometry constraints may be mitigated through the use of correct seal geometry. For example, in rotary seals, where higher shaft speeds are exhibited, the permissible pressure differential across the seal becomes smaller.
Increased shaft speed produces greater frictional heat generation, but so too does pressure applied to the seal as more of the lip surface is forced against the shaft. Since too much friction can result in faster wear and shorter seal and shaft life, design variations that help offset these negative effects of higher shaft speeds need to be built into the seal. These design enhancements can include reducing the radial load of the seal lip, upgrading the sealing material to one that can handle higher temperatures, or optimising the shaft sealing surface.
To maintain high equipment availability, the use of appropriate seals is essential as a means of preventing leaks and defending machinery against the ingress of common contaminants such as dust and dirt. With a wide range of specialised seals now available, each with a unique set of features, understanding the function of a seal in any given application is essential if engineers are to increase the performance and extend the service life of industrial machinery, while also reducing maintenance costs in the process.
Once thermo-chemical and mechanical criteria have been satisfied engineers must still ensure regulatory compliance, such as FDA compliance in the food and pharmaceutical industries, demanding upto- date knowledge of elastomer and polymer specific legislation. To extract the full efficiency benefits that can be achieved by optimising a sealing system, it may be best to partner with an experienced seal supplier who understands and responds to challenges across industry. ERIKS, for example, can offer an unbiased service in matching the seal to the application and help you make the most of today's sealing solutions.
MORE FROM THIS COMPANY
OTHER ARTICLES IN THIS SECTION