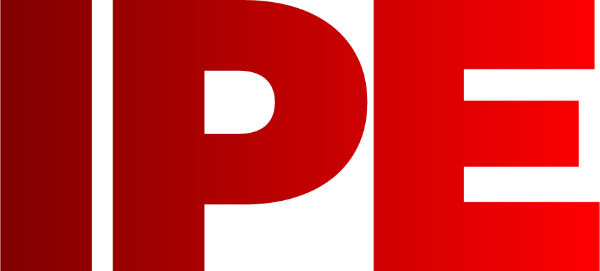
![]() |
Edward Lowton
Editor |
![]() ![]() |
Home> | Plant, Process & Control | >Pumps | >Reaping rewards of pump repairs |
Reaping rewards of pump repairs
19 August 2013
ERIKS has carried out a pump repair plan for a major UK automotive manufacturer that has resulted in an annual energy saving of about £4000. The plan, which included pump repairs conducted with Henkel, has also achieved a CO2 saving of 28t in the first year.
The story began when Eriks evaluated the efficiency of one of the automotive company’s pumps. This was a 22kW ELPO, which handles process water for a metalwork pre-treatment process prior to body coating. The pump was found to be under-performing by at least 30% against the manufacturer’s original test data.
The unit was dismantled and all components examined for wear. The examination revealed that the pump was heavily corroded and the impeller worn, burred and imbalanced. In addition, the mechanical seal had seized and the pump was out of alignment with the motor. There were further problems in that the volute was cut-water worn, the bearings showed evidence of fretting and corrosion and the motor was not inverter rated.
To improve pump efficiency, a repair programme was conducted by Eriks and Henkel, who have formed a partnership to assure best practice in pump repair. The partnership combines Eriks proven engineering expertise with Henkel’s experience and know-how in ceramic and energy-saving coatings. Using this shared experience, the two companies are able to provide repairs that are undertaken to the highest standards of workmanship.
The repair work was conducted at Eriks’ EMS Workshop in Southampton. Some of the components required coating with Henkel’s Loctite polymer composites so the first step was to steam clean these parts to remove any residue and salts. Castings, impellers and volutes are all subject to wear due to corrosion, erosion, cavitation and mechanical damage and all can be effectively and economically repaired with Henkel’s Loctite surface engineering products. Parts were then blasted to achieve a surface roughness of 75 microns.
With this preparation work completed, the treatment of surfaces began. The substrates were pre-treated with Loctite 7515 to prevent corrosion and improve adhesion between the metal parts and the polymer composites. Loctite 7117 was applied as a 'hold coat' to smooth surface imperfections and provide an efficient key for the thicker layers required to return the pump to its original dimensions. Loctite 7226 was used as the build coat to replace many years of wear and provide a tough surface, resistant to future wear. A further layer of Loctite 7117 was applied over Loctite 7226 to create a smooth finish, which will reduce friction within the pump and improve its energy efficiency.
To complete the repair work, the pump was fitted with new bearings and both oil and mechanical seals. The impeller was dynamically balanced, the pump re-assembled and a new 22kW high efficiency motor fitted. Motor and pump were then fitted to the bedplate and laser aligned.
With the repair work completed, a second performance test was carried out to measure the improvements that had been achieved. It was found that the remedial work had restored the pump to original specification, increasing its efficiency by 30%.
An estimated energy reduction of £3936 was calculated for the first year alone (calculated at £0.08/kWh at 12h/day with an 80% load). It was therefore clear that the cost of the repair, which amounted to £5542, would soon be recovered and that substantial savings would follow. Over a five-year period, this accrues to an energy saving amounting to £19,680. On carbon emission, the annual saving is 28t.
The repair work provided a tough protective coating to protect parts against attack. By applying Loctite polymer composites coatings and compounds, the treated surfaces benefit from good wear resistance against abrasion, erosion, corrosion and chemical attack, plus efficient adhesion. By restoring the worn surfaces, the repair work has extended part life, increased component efficiency, cut replacement costs and reduced spare part inventory.
On one pump alone, the manufacturer has made significant savings in costs and emissions and is now evaluating the potential energy savings that could result from further repair programmes.