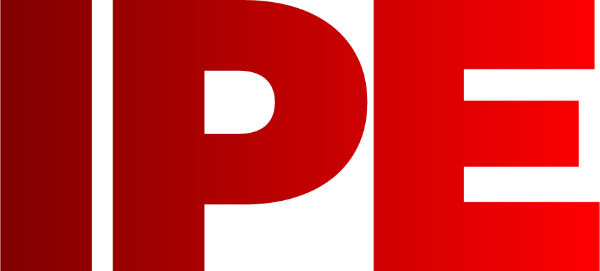
![]() |
Edward Lowton
Editor |
![]() ![]() |
Home> | Production Engineering | >Deburring equipment | >Carbon infrared oven saves time and space |
ARTICLE
Carbon infrared oven saves time and space
17 April 2013
A carbon infrared oven from Heraeus Noblelight has helped Stoelzle Flaconnage to achieve faster curing of organic paint sprayed onto perfume bottles. Its installation has saved space compared with an alternative hot air oven at the Knottingley glass manufacturing plant.
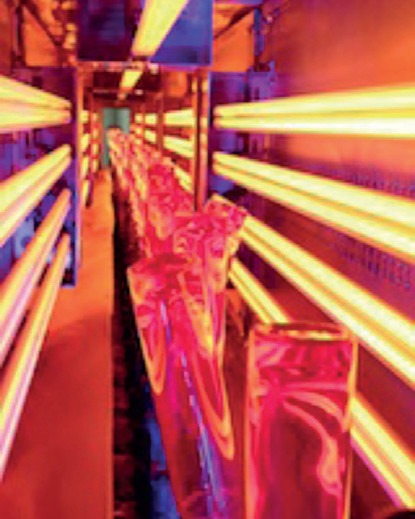
A carbon infrared oven from
Heraeus Noblelight has
helped Stoelzle Flaconnage to
achieve faster curing of
organic paint sprayed onto
perfume bottles. Its
installation has saved space
compared with an alternative
hot air oven at the Knottingley
glass manufacturing plant.
When it was decided to adapt a mothballed ceramics spraying machine to provide additional organic paint spraying capacity, it was realised that there was insufficient space for a conventional warm air oven.
Also, Stoelzle engineers wanted paint drying times to be cut to match increased production line speeds.
Tests at the Heraeus Application Centre showed that using carbon infrared, coatings on glass containers delivered at a line speed of 4.4m/min, could be cured in 90s. A five zone oven now sits over the conveyor system.
Each zone consists of two side infrared modules and one top module. The twin tube, carbon infrared emitters have a response time of less than 2s, so the oven can be quickly switched off when there are gaps in the line.
When it was decided to adapt a mothballed ceramics spraying machine to provide additional organic paint spraying capacity, it was realised that there was insufficient space for a conventional warm air oven.
Also, Stoelzle engineers wanted paint drying times to be cut to match increased production line speeds.
Tests at the Heraeus Application Centre showed that using carbon infrared, coatings on glass containers delivered at a line speed of 4.4m/min, could be cured in 90s. A five zone oven now sits over the conveyor system.
Each zone consists of two side infrared modules and one top module. The twin tube, carbon infrared emitters have a response time of less than 2s, so the oven can be quickly switched off when there are gaps in the line.
MORE FROM THIS COMPANY
- IR heating systems
- Compact infrared print dryer
- Faster glass tempering
- Fast response infrared heating system
- Heating systems on show
- Air rinsing for jam pots
- Sealed for outdoor use
- Chocolate moulds get pre-heat treat
- Line speed boosted
- Carbon infrared emitters halve drying times for screen-printed T-shirts
OTHER ARTICLES IN THIS SECTION