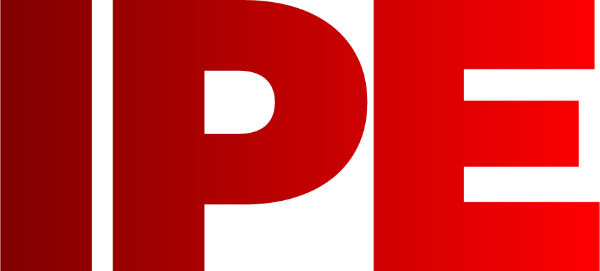
![]() |
Edward Lowton
Editor |
![]() ![]() |
Home> | Plant, Process & Control | >Cooling equipment | >Thermal fluid system |
Home> | Plant, Process & Control | >Process heating | >Thermal fluid system |
Thermal fluid system
25 July 2013
AIM Composites has installed a Babcock Wanson Thermal Fluid System into its facility in Waterbeach, Cambridgeshire to heat and control the cooling of a new press that produces lightweight panels and mouldings for the transport sector.

Existing presses at the site were steam fed and water-cooled but the company found the system to lack the precise controllability it required. A Babcock Wanson TPC1500B Thermal Fluid Heater was chosen to provide the heating, coupled to a purpose-designed control loop to cool the system against a predetermined profile. A single fluid is used throughout the system for ease of operation and maximum efficiency.
Control of the complete heat/cool cycle is achieved using a bespoke temperature control unit and dedicated software, also designed and installed by Babcock Wanson. The menu-driven software allows up 50 heating/cooling profiles to be uploaded and stored in its memory, with each profile offering up to six temperature ramp and dwell stages. A simple menu-driven selection then allows the process to run completely automatically.
This provides a high degree of flexibility, and the minimal need for operator involvement allows greater speed and repeatability of the process. All data is stored in the controller for download and review as required.
David Drewry, technical director for AIM Composites says: "Converting to thermal fluid heating and cooling has resulted in a reduction in process cycle time by up to 30%. Other benefits include reduced maintenance costs, reduced energy costs (replacing three steam boilers by one thermal heater) and an increase in available floor area (removal of the boiler house and old cooling system)."
- Rental service
- Babcock Wanson UK introduces DCT regenerative oxidisers and solvent recovery systems
- Factory installs thermal fluid heaters
- Training course for coil boiler operators
- TPC-B Thermal Fluid Heater
- Babcock Wanson launches new electric thermal fluid heaters
- Babcock Wanson acquires Steam Plant Engineering
- BWD Series of Fire Tube Steam Boilers
- Full steam ahead with carbon cuts
- Drake Extrusion awards process heating order to Babcock Wanson