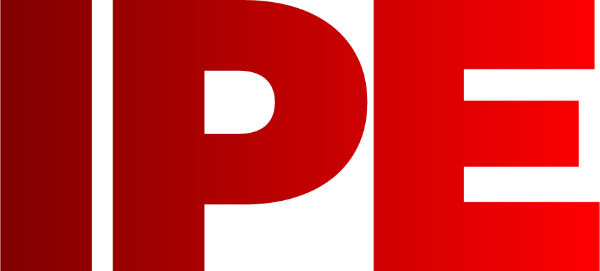
![]() |
Edward Lowton
Editor |
![]() ![]() |
Home> | Energy Management | >Compressors & ancillary equipment | >Compressors and heat recovery system |
Home> | Plant, Process & Control | >Compressors and ancillary equipment | >Compressors and heat recovery system |
Compressors and heat recovery system
03 December 2013
Five Atlas Copco water-cooled, rotary screw compressors are providing semiconductor manufacturer Nanium in Portugal with reliable, high-quality air, while an Atlas Copco ER900 heat recovery system enables the company to substantially reduce CO2 emissions and achieve energy savings.
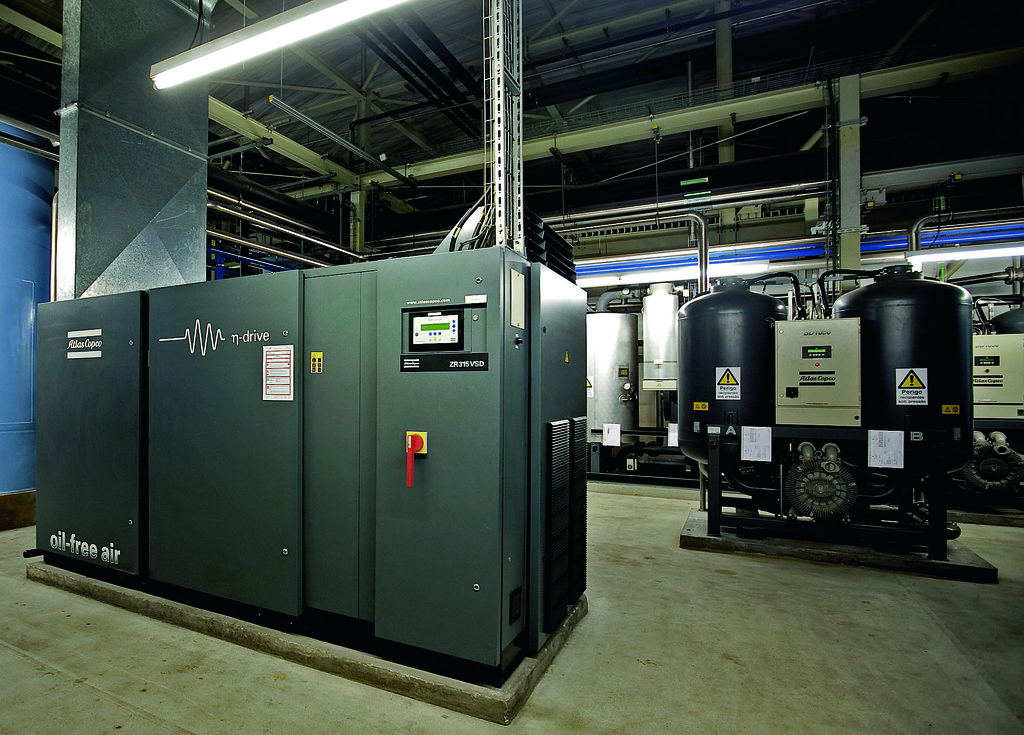
The compressors installed are three ZR 300s, one ZR 315 with variable speed drive (VSD), and one ZR 400. Each compressor is combined with a heated blower purge desiccant air dryer, or BD dryer, to obtain a high-quality dewpoint (PDP < -40C). Nanium also specified no oil and a low quantity of particles to standard ISO 8573 Class 0 to meet its strict standards.
An Atlas Copco ER 900 unit, a heated water management system for heat recovery in oil-free, water-cooled compressors, recovers heat in the form of hot water. Atlas Copco changed the company’s compressor to discharge its cooling water at about 80°C. Hot water is pumped to a heat exchanger, whose secondary circuit circulates return water to the boiler. As a result, primary energy gas input is dramatically reduced.
- Atlas Copco debuts new smart industrial air compressors
- Savings cover loan repayments
- Industrial air line manager
- Atlas Copco and Pennine Pneumatic Services Showcase pathway to Net Zero with energy efficient solutions at Water Equipment Show
- Industrial gas generation: Why the time is right to switch to on-site sourcing
- Plug-and-play energy recovery
- Energy savings for board maker
- Atlas addition
- Oil-free rotary screw blower
- Distributor appointed