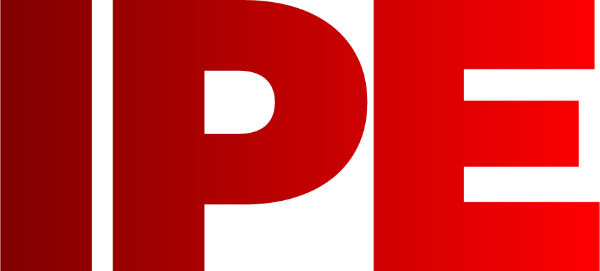
![]() |
Edward Lowton
Editor |
![]() ![]() |
Home> | Energy Management | >Boilers and burners | >Integrated solution |
ARTICLE
Integrated solution
25 January 2013
A recent example of an integrated project undertaken by WellmanWulff describes activities at the Shell green site in widnes, home to the Mersey Valley Processing centre. WellmanWulff successfully manufactured and inst
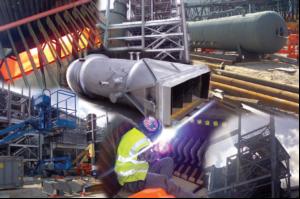
A recent example of an integrated project
undertaken by WellmanWulff describes
activities at the Shell green site in widnes,
home to the Mersey Valley Processing
centre.
WellmanWulff successfully manufactured and installed a heat recovery steam generator (HRSG), a type of waste heat recovery unit, and associated equipment as part of a complex sludge incinerator plant.
The need was driven by United Utilities implementing a complete revamp of its dewatering plant.
The total project, known as Shell Green - Stream 3 Joint Venture - has been lead by Veolia and Costain. The objective was to design and install a stationary fluidised bed combustor, waste heat boiler, steam turbine and flue gas cleaning system.
WellmanWulff 's responsibility lay with ensuring the integrated plant took the waste heat gas from the fluidised bed incinerator, and passed it through a two-pass boiler producing 16,000kg/h of steam at 40bar, at a temperature of 400°C. This superheated steam is then used to generate electrical power via a steam turbine.
WellmanWulff also manufactured and installed a large economiser, steam drum, electro static precipitator and ash silo system. In the final phases of the process, the flue gases enter the ESP, where most particulates from the gas stream are removed.
WellmanWulff successfully manufactured and installed a heat recovery steam generator (HRSG), a type of waste heat recovery unit, and associated equipment as part of a complex sludge incinerator plant.
The need was driven by United Utilities implementing a complete revamp of its dewatering plant.
The total project, known as Shell Green - Stream 3 Joint Venture - has been lead by Veolia and Costain. The objective was to design and install a stationary fluidised bed combustor, waste heat boiler, steam turbine and flue gas cleaning system.
WellmanWulff 's responsibility lay with ensuring the integrated plant took the waste heat gas from the fluidised bed incinerator, and passed it through a two-pass boiler producing 16,000kg/h of steam at 40bar, at a temperature of 400°C. This superheated steam is then used to generate electrical power via a steam turbine.
WellmanWulff also manufactured and installed a large economiser, steam drum, electro static precipitator and ash silo system. In the final phases of the process, the flue gases enter the ESP, where most particulates from the gas stream are removed.
MORE FROM THIS COMPANY
OTHER ARTICLES IN THIS SECTION