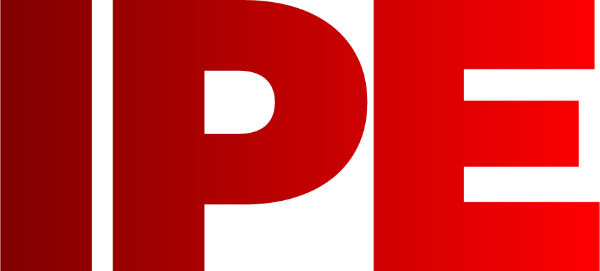
![]() |
Edward Lowton
Editor |
![]() ![]() |
Home> | Production Engineering | >Cables, connectors and energy chains | >Cable management: Less is more approach |
Cable management: Less is more approach
07 August 2014
While robots are becoming more complex and machine reliability is increasing, the methods used to attach and guide cables have not always followed suit, as Justin Leonard, director, igus, explains
Most experts agree that one of the top mistakes is underestimating cable management issues. During a conference hosted by the Robotic Industries Association, a group of leading system integrators cited cable issues as the number one reason for downtime in robotics cells. Headaches range from tangled and corkscrewed cables, to complete breaks that cause downtime, lost revenue and damaged reputations.
The 'less is more' approach to cable management is a best practice that robotics engineers and integrators can apply. It centres on cable management systems for six-axis robots, including cables, hoses, tubing and connectors, in three separate sections.
Most current systems try to keep the cables on a six-axis robot static while everything operating around them is dynamic. Using one, long restrictive cable package prevents movement in sync with the robot; restrictions stress cables, which accelerates failure. Often technicians bind cables with excessive dress packs (protective coverings on cables), cable ties, and even duct tape to minimise tangling, but such solutions can cause corkscrewing and failure.
I believe that the key to longer-lasting cables is to consider a six-axis robot as three separate sections: the sixth to third axis; the third to second axis; and the second to first axis. Each section needs a minimal dress pack, strain relief with service loops, and a junction box that contains and protects electrical connectors joining the cables.
Use of a strain relief mechanism can eliminate stresses and extend the service life of a moving cable. This strain relief may consist of standard elements such as tie wrap plates or clamps. Engineers should ensure the cables are in the neutral axis, not touching the inner or outer radius of the cable management system.
Separating the dress pack into three shorter sections prevents it from wrapping, catching or snagging on machines and minimises stress on cables and hoses. This approach can be applied to any six-axis robot, regardless of manufacturer or application.
In addition, it is imperative that six-axis robots use dynamic cables designed for continuous flexing. Two key features to take into account are torsion-resistance and shielding. Constant movement on shielded cables can make the shield break down. Use unshielded, high-flex cables whenever possible. If this is not an option, consider special 'torsionable' cables.
Corrugated or flexible-tubing is one option for protecting cables on six-axis robots and is available in a range of sizes and styles. It has superior tear resistance at connection points and a long service life, even with reverse-bend cycles. However, it has minimal torsion resistance, and can only be fixed at two points with a defined length. The tubing can stretch as the robot moves, which puts undue stress on cables. Tooling interference sometimes occurs because there is no control path for movement.
An enclosed dress pack mounts directly to the robot and is available in multiple configurations. It uses corrugated tubing installed inside a plastic-reinforced housing to protect cables. The system’s spring-loaded design minimises catch and pinch points. However, due to the completely enclosed housing, cable maintenance can prove difficult, and because it is not modular, the entire unit must be replaced if one component breaks.
Robotic cable carrier systems are at the core of the 'less is more' approach, and can be used universally for six-axis robots. The system mounts directly to the robot and is available in multiple configurations. Like an enclosed dress pack, it has a spring-loaded design that minimises catch and pinch points. However, robotic cable carriers come equipped with strain relief options to extend the service life of the cables; cables can also be quickly added or removed without dismantling the system. The defined bend radius of a robotic cable carrier protects cables from exceeding their maximum bend radius.
The limitations of the system include minimal resistance to high-concentration acids and caustic chemicals, and the inability to handle circular movements with heavy loads.
Robotic cable carriers are well suited for welding robots in tight areas, multiple-tool applications, material-handling jobs, and de-burring operations. For added flexibility, they come in a fully enclosed, pull-through design for easy cable access, or as a lightweight, low-cost system for applications that do not require cables to be completely enclosed.
Ideally, a robotic cable carrier system should allow sufficient clearance inside the cable carrier for electrical cables, pneumatic hoses and tubing for other media. This compensates for relative forces between cables and hoses. Cable carrier suppliers normally provide this data. For instance, general rules of thumb for the line of robotic cable carriers from igus include: total cable and hose diameters must not exceed 60% of the carrier diameter, leave at least a 10% clearance between any two cables or hoses, and cables and hoses need to move freely inside the carrier.
The 'less is more' approach also eliminates some safety concerns within a robotics cell. Cables are able to move more freely, but are protected and guided so that they will not injure workers.
I believe the ideal cable carrier management system should guide cables in one continuous path, eliminate loose and unmanaged cables, control the bend radius of cables to avoid pinching, have the ability to quickly add or remove cables, and be available as a fully enclosed design for extremely harsh environments.
- Bearing material endures harsh environments
- Designed to stand out
- Bearing answers to common questions
- Long-lasting solutions for e-chain applications
- Slew ring bearing
- Latest catalogue
- AI helps more companies access robotics: New chatbot advisor for RBTX.co.uk
- Cable range extended
- Additional material joins knife edge roller range
- Antibacterial material for bearings