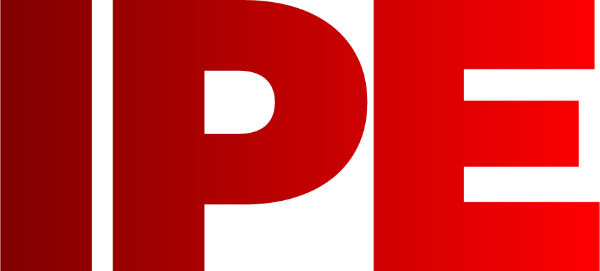
![]() |
Edward Lowton
Editor |
![]() ![]() |
Home> | Energy Management | >Compressors & ancillary equipment | >Expanding on ESOS to secure savings |
Home> | Plant, Process & Control | >Compressors and ancillary equipment | >Expanding on ESOS to secure savings |
Expanding on ESOS to secure savings
03 November 2014
Keith Findlay, AIRScan manager of Atlas Copco Compressors outlines steps he believes will help compressed air users fulfil the requirements of ISO 50001, meet the Energy Savings Opportunities Scheme (ESOS) obligations, and implement a pattern of good practice that can deliver financial benefits
By December 2015 all UK companies with 250 or more employees, or annual turnover in excess of £42m, must have completed a comprehensive audit of their energy use. The countdown has already been heeded by some firms; others remain unaware of the requirement, which has been introduced by the government under ESOS in response to the EU’s efficiency directive.
Every four years after the first audit, all aspects of energy use must be assessed and reported, including compressed air. While the ESOS initiative is a welcome step towards greater understanding of energy usage, it does not oblige participants to carry out improvements.
One strategy to both comply with the regulations and reap the benefits is to work proactively towards a more comprehensive, results-orientated voluntary framework for energy saving, such as the worldwide energy standard ISO 50001. This not only encourages practical improvement by requiring that an audit is carried out and recommendations are acted upon, but would automatically incorporate compliance with ESOS.
ISO 50001 comprises specific guidelines for different areas of energy. It is within these areas that specialist advice and coordinated activity can produce demonstrable savings. Under ISO 50001, for example, is ISO 11011, a worldwide standard introduced in 2013 for compressed air.
A compressed air audit carried out under ISO 11011 would assess the entire compressed air system. Data must be analysed, reported and documented along with an estimate of energy savings. The standard specifies that 'the overall goal of the assessment shall include identification of performance improvement opportunities in the compressed air system being assessed using a systems approach'. In doing so, it is possible to eliminate wasteful practices, leaks, artificial demand and inappropriate use.
Six steps of optimisation
The standard aims to create and maintain an energy balance between supply and demand, and to optimise storage and control. This proactive approach can be summed up by the 'six steps of optimisation' that Atlas Copco recommends for compressed air users. The process begins with a site visit to estimate potential energy savings based on an overview of the size and complexity of the plant. Next comes AIRScan, a detailed and objective compressed air audit . Potential savings are calculated based on an accurate measurement of current status using tools that quantify flow, pressure, electrical current input, ambient conditions, air quality, dew points and leakages.
Leaks are particularly damaging in terms of energy waste; a leakage point of just 5mm costs an estimated £3800 in wasted energy over a year.
The third step is to deliver a detailed report recommending system improvements, which are carried out under step four of the process.The priority is that the potential savings detailed in the audit are delivered as projected.
For example, in a recent project undertaken by Atlas Copco, a leakage detection programme instigated across a UK vehicle manufacturing plant identified leaks costing £102,000/year in lost energy. A similar programme conducted by the AIRScan team at a confectionery manufacturer, over the course of three days, pinpointed £31,000 worth of leaks that are now being repaired.
Process leaks also result in overspending on energy. These can be corrected by replacing production line equipment, for example, establishing greater control of pressure or shutting down systems when not in use.
Another energy-saving measure is the concept of energy recovery. After compression, air is often at a high temperature and before it can be distributed into the piping system and delivered to the process, heat has to be extracted. As much as 94% of the electrical energy used by an industrial air compressor is converted into heat, which can be redirected into process applications or for general heating purposes within the building, which can reduce reliance on external electricity and gas supplies.
Step five seeks to maintain optimised performance over the long term. With the introduction of a monitoring system such as Atlas Copco’s SMARTlink, energy performance can be continuously measured and assessed.
The sixth stage of the optimisation cycle involves repeating the original audit at regular intervals to ensure new saving opportunities can be identified and acted upon.
By following these six steps in a coordinated manner, compressed air users can not only begin to fulfil the requirements of ISO 50001 and meet ESOS obligations, they can implement a pattern of good practice that can deliver calculable financial and sustainability benefits year on year.
- Atlas Copco expands solid desiccant air dryer range
- Atlas Copco expands its vacuum solutions
- Plant complies with latest medical standards
- Authorised distributor
- Air for energy project
- New compressors boost energy savings
- Looking to the future
- VSD+ - Not just an evolution, it's a complete revolution
- On-site nitrogen generation
- 0% APR finance scheme