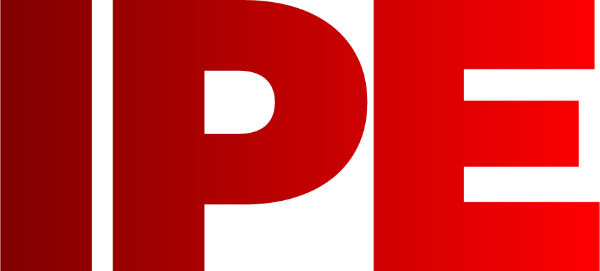
![]() |
Edward Lowton
Editor |
![]() ![]() |
Home> | Production Engineering | >Paints and applicators | >Coating matters |
Coating matters
27 May 2015
Specialised coatings enhance the surface of metals and other substrates to solve wear, corrosion, lubrication and release problems. Andrew Courtney from Surface Technology examines the challenges posed by different operating environments and the impact on the choice of a suitable surface coating
To start with I'm going to look at the automotive industry – considering multiple lightweight materials, high temperatures and low lubrication
Previously the internal combustion engine was manufactured from cast iron, forged steels and die-cast aluminium alloys. Heat treatment, coupled with the use of white metal or bronze bearings, provided the wear surfaces.
Today, modern engines must last for longer distances whilst adhering to emission regulations. To reduce fuel consumption lighter engines are required; this introduced a much wider range of materials requiring coatings to overcome any wear, corrosion and friction problems.
Preventing friction in low lubrication areas
Piston rings, skirts and pins are often coated with hard wearing, low friction coatings to aid initial running-in followed by long-life performance. This is due to the lower oil lubrication levels associated with cold engine starts and the reduced amount of lubricant permitted to reach the combustion chamber. The use of ceramic coatings is increasing and high temperature thermal spray or vacuum application methods can be used.
Preventing corrosion of lightweight and sophisticated materials
Increased use of bio fuels has increased corrosion problems of fuel input systems, however there are a range of thin coating solutions. Along with improved engine performance and tyre design, there has resulted in a need for better braking systems. The move to open spoke alloy wheels and consequently more visibility has also required the improvement of anti-corrosion coatings and appearance of the brake callipers. The use of aluminium callipers has increased and these require hard anodising to improve external corrosion protection
Surface Technology specialist ductile zinc nickel plating, for example, is now also used on fluid delivery pipework and air suspension systems, the key benefit being its malleability. This offers manufacturers improved production efficiencies, reduced complexity and working capital through component standardisation.
Components in door latches, seat belt mechanisms, under bonnet and seat adjustment assemblies must be coated to provide corrosion resistance, noise reduction and friction performance. Vehicles increasingly have multiple motors containing Neodymium/Iron/Boron magnets which, while very powerful magnetically, are also susceptible to corrosion. Surface Technology has a range of coatings that can overcome this, ranging from its proprietary TriCem coating to heat cured coatings designed to cure at temperatures that leave the magnetic performance of the various alloys unaffected.
Preventing wear in tight tolerances and high temperatures
Turbo chargers need tight tolerances between the rotors and a fluoropolymer coating can overcome this. Surface Technology has a range of options. Turbo rotors in high performance engines can be coated with polymers such as filled PFA.
Brake pistons require coating with precise thickness, low friction and brake fluid resistant coatings to protect the seals. This particularly applies to high performance vehicles where the temperature of the assembly can become high enough to cause the coatings containing lubricating particles to soften in contact with the brake fluid. Surface Technology uses higher temperature resins to overcome this.
High volume production machinery
Keeping production equipment up and running is a priority for engineers and plant personnel working in high volume food manufacturing environments. Surface release is a core challenge for bakery equipment, with reduced non-stick properties leading to inefficient production and increased, costly, downtime for material cleaning.
Consistently efficient stainless steel dough and divider hoppers are essential to maintain production however the non-stick properties deteriorate with use. Reducing oil in bread production is encouraged, providing health and safety benefits while minimising costs. Armourcote 1530, for example, has proven successful for enhancing stainless steel surfaces while protecting against surface wear.
Thermal spray alternatives
Hard chrome withstands friction, extreme temperatures and corrosion whilst operating at optimum levels and has been a mainstay of industrial coatings in industry. However, the safeguarding EU and US regulations mean that hard chrome plating is incurring rising costs and extensive regulation and its use will be restricted under the REACH directive.
An emerging solution to this problem, is High Velocity Oxy-Fuel Spray (HVOF), a thermal spray coating process that gaseous fuels, generally to protect against wear. In turn this solution provides benefits around, but not restricted to, wear behaviour, no hydrogen embrittlement and higher ductility for lower microcracking tendancy.
Surface Technology has extensive experience in thermal spray coatings used successfully for both OEM component manufacturing and repair applications for a wide range of industries.