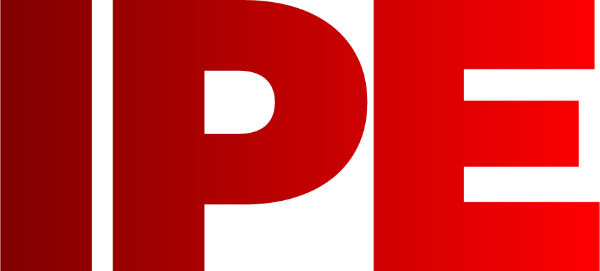
![]() |
Edward Lowton
Editor |
![]() ![]() |
Home> | Efficient Maintenance | >Maintenance management software | >Cloud-based solution: An asset for port |
Cloud-based solution: An asset for port
26 October 2015
Port Otago operates a primary deep-water, export-based container terminal at Port Chalmers in New Zealand’s far south. With outstanding facilities and a committed team in place, the company wanted to replace a basic asset management system whose lack of functionality and non-integration with other critical business systems created inefficiencies
Bob Smillie, maintenance manager at Port Otago, explains: "Our asset performance data was always incomplete, with information in various locations. This made it difficult to develop any meaningful evaluation in a consistent manner.
"It was also time-consuming to generate and update the reports we required, and interpreting inconclusive data was a complex and frustrating task. When predicting maintenance activities such as asset or component replacements, technical staff often had to rely on their instincts and experience to formulate lifecycle data decisions.”
Port Otago also found it challenging to obtain detailed breakdowns of costs: "It was often difficult to obtain adequate data on key metrics, which we needed for maintenance reports,” adds Smillie. "The data we had only provided a high-level view, making our analysis sketchy at best.”
Port Otago also lacked a reliable inventory management system: for example, spare parts were not catalogued when they were purchased, which gave the business no ability to track usage or guide forward purchasing decisions.
"It was common to place orders for a component from a European supplier only to discover, just a few days later, that we needed additional items or different quantities from the same company,” says Bob Smillie. "Random direct purchasing activities were widespread, increasing costs and impacting our ability to reliably plan and coordinate work activities. This was especially a problem when our work required the operation to commit to planned maintenance downtime of critical business assets.”
Cloud-based solution
Following an analysis of available enterprise asset management software and potential support partners, Port Otago worked with IBM business partner, BPD Zenith, to deploy New Zealand’s first implementation of the BPD Zenith MaxiCloud solution. This is based on IBM Maximo Asset Management software, running in a cloud environment.
"BPD Zenith’s expertise was vital to this deployment,” says Bob Smillie. "In addition to finding a supplier, I wanted to achieve a reliable partnership model where we could work closely to drive significant change across the business through modern and aligned systems and processes. My aim was definitely a journey with a collaborative partner rather than an event with a one-time supplier.
"BPD Zenith’s approach and the MaxiCloud solution allowed us to take advantage of all the benefits of a widely used enterprise asset management solution to deliver high asset availability, combined with reliable and predictable performance – and best practice-focused system development opportunities. It was a strategic approach to our future – without the need to hire additional support resources to manage it.”
From reactive to predictive
Maximo has enabled Port Otago to make significant progress towards its goal of a modern inventory base supported by streamlined usage reporting to reduce ad hoc purchasing.
"We’re forecasting significant cost-savings and improvements to productivity,” says Smillie. "Our maintenance crew can approach routine planned tasks with the confidence that the necessary spares are available, which is quite a change from our previous process.”
The initiative has already started to reverse Port Otago’s previous ‘planned versus reactive maintenance’ work mix – from an estimated 30% planned vs 70% reactive to 60% planned vs 40% reactive. This will result in substantial cost and organisational savings.
Safety compliance has also been improved by Maximo’s work order system. "Many of our assets have significant statutory maintenance requirements because they include critical lifting gear and operate within a complex mix of heavy mobile and fixed assets and people,” says Bob Smillie.
"Our planned work order documentation now include references to known area hazard warnings, coloured hazard warning pictograms, detailed safe operating procedures references and attachments, as well as PPE reminders – providing our staff with total work packages and added confidence in the outcomes across the business. In the unlikely event of a failure or incident, Maximo can quickly provide detailed maintenance history report data to add to an investigation.”
Port Otago plans to develop its Maximo abilities out on the port, giving its employees access to work orders, inventory, and the raising of service requests from portable mobile tablets.
Geoff Plunket, CEO, Port Otago, says: "Maximo gives us a range of organisational advantages, such as a greater ability to demonstrate statutory compliance, increasingly accurate visibility over critical asset behaviours, and a more predictable, efficient, and safer organisation. The increased insights about the health of our business greatly improve our strategic decision-making abilities.”
- Value-driven solutions
- Mobile reporting
- The role of maintenance and asset management in optimising plant performance
- Operational experience
- Real Asset Management
- Mobile CMMS solution
- Maintaining visitor satisfaction
- Helping to ensure visitor satisfaction
- Busy end to year
- AWE Achieves Greater Program Risk Control and Boosts Productivity with Infor EAM