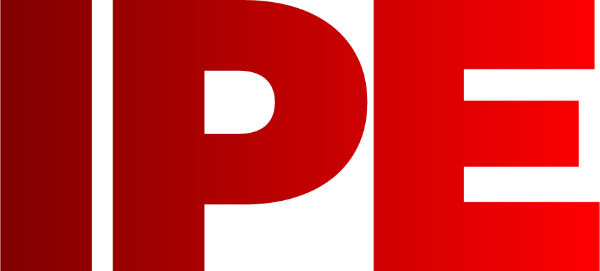
![]() |
Edward Lowton
Editor |
![]() ![]() |
Home> | Handling and Storing | >Conveyors | >Keeping cheese on the move |
Keeping cheese on the move
10 April 2017
When a cheese producer in Israel needed to connect its up-level processing area to the floor levels of the end of line environment, a spiral conveyor was considered a suitable solution both for throughput and gentle product handling. However, the challenge for a spiral conveyor was the minimum space available between the construction beams in the various floors which was too narrow for conventional spirals.
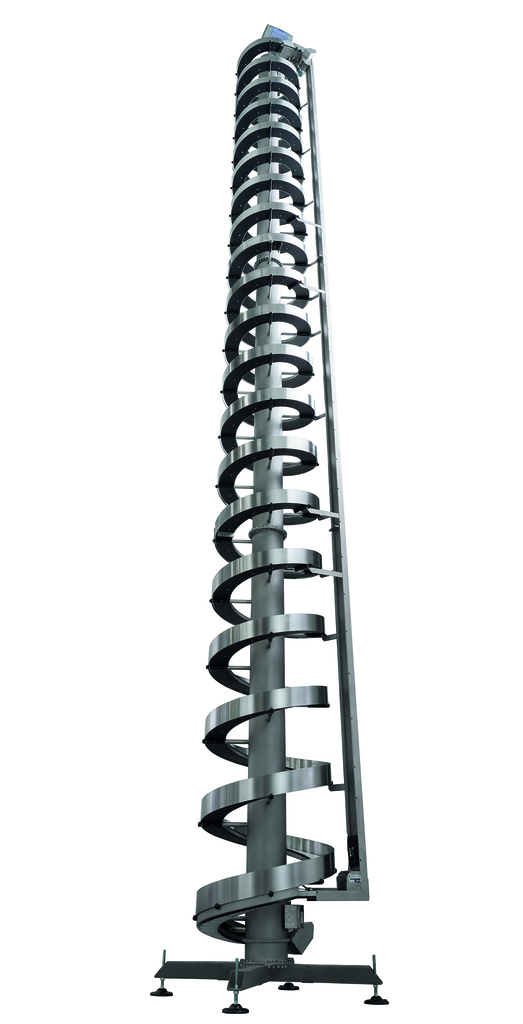
Vacuum packed cheese blocks needed to be transported downwards at a rate of 40 per hour without damaging the plastic and losing any product lifetime. However, because of the enormous de-elevation required, traditional conveyors were not an option. Platform elevators could also not be used because of their low throughput capacity.
The solution chosen was an AmbaFlex SpiralVeyor SVs platform which has a 140mm wide belt and only requires a diameter of 1240mm. This machine comes from the Spiralveyor SlimLine programme.
The total elevation required 19.5 spiral windings; the patented Triple-E conveyor belt technology with 100% rolling friction makes such a number of windings possible in one go with one belt.
The customer was very happy that AmbaFlex could fulfil all the requirements without any comprises such as the number of winding to de-elevate, the compact build required, the speed, and good product handling. And on top of all that, the solution comes with a full, stainless steel, welded frame which does not trap any dirt and contains no soft metals like aluminium – a must to withstand the aggressive cleaning detergents used in the dairy industry.