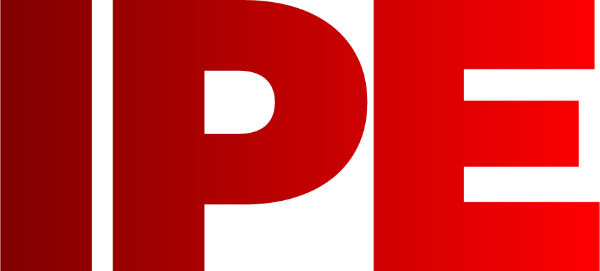
![]() |
Edward Lowton
Editor |
![]() ![]() |
Home> | Production Engineering | >Grinding and abrasives | >Blast room boost to finishing standards |
Home> | Handbooks | >Manufacturing Matters Ireland | >Blast room boost to finishing standards |
Blast room boost to finishing standards
17 October 2017
Freyssinet, a manufacturer, of bridge bearings and other structural components, has invested in a self-contained blast-room from Hodge Clemco as part of a project to upgrade finishing processes at its West Midlands, UK, premises.
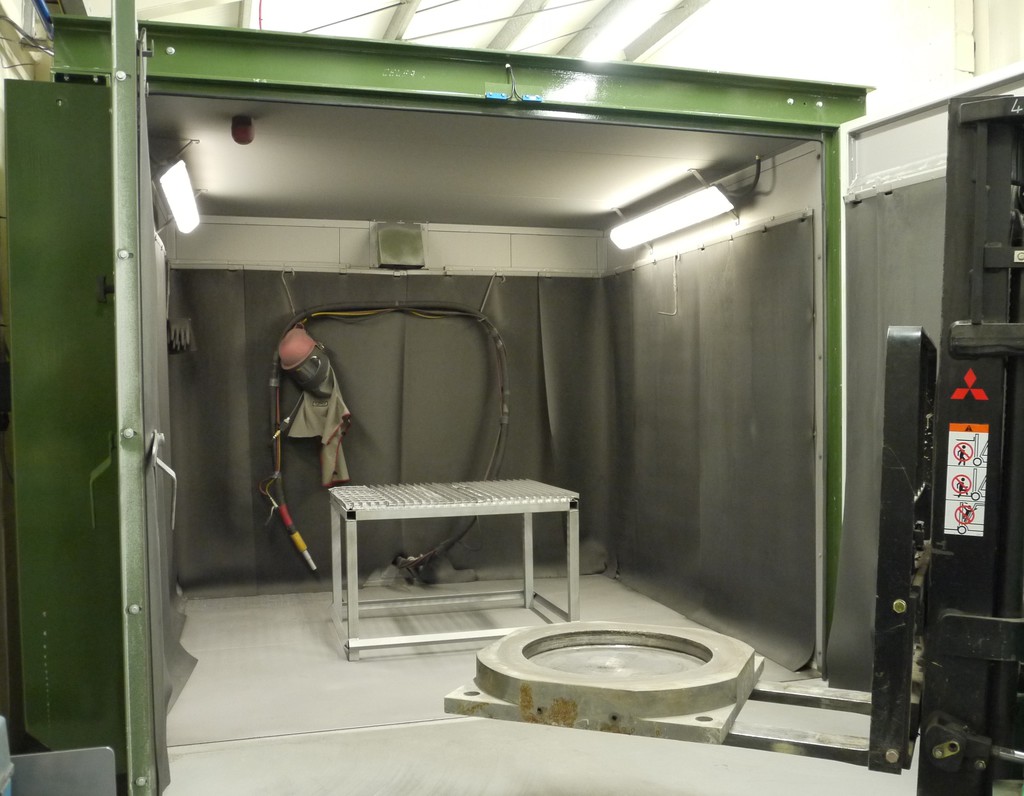
Freyssinet counts the Highways Agency, local authorities and major contractors and property developers among its clients and supports a wide range of products and services with an in-house engineering design team. The company has specialised for many years in bridge bearings and post-tensioning systems, which are often exposed to adverse weather and other potentially damaging conditions for long periods.
After machining, the high-grade steel components are typically protected with an aluminium base-coat and four coats of marine paint. The Hodge Clemco blast-room has been designed to enable the company to produce the SA2.5 to SA3 surface profile essential for long-term adhesion of the base-coat. This is achieved using chilled iron abrasive at 8-9 bar pressure.
The blast-room is designed for machined components weighing up to 2t to be carried in manually or by lift truck. The 3x3m chamber has walls and roof manufactured from double-skin mild steel plate filled with Rockwool slab, which provides effective acoustic insulation. Air inlet ducts and exhaust points around the chamber ensure effective dust extraction and air ventilation equivalent to approximately 3.6 air changes per minute.
To recover abrasive, an operator sweeps used material into a large floor hopper from where it is fed to a separator system that removes contaminants, fines and dust. A high-pressure fan assists recovery of the heavy metallic abrasives used. Clean abrasive is finally returned to a storage hopper that automatically refills the blast machine.
The blast cleaning machine is a high-production direct-pressure unit with a large inspection cover for easy access. It feeds a 3/8in. (10mm) ID tungsten-carbide-lined nozzle with a fail-safe dead-man’s handle that maintains maximum blasting velocity, uniform abrasive distribution and high work-rate in the long term.