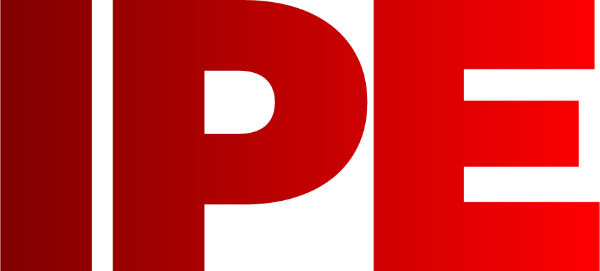
![]() |
Edward Lowton
Editor |
![]() ![]() |
Home> | Efficient Maintenance | >Events | >Smart maintenance for the smart factory |
Smart maintenance for the smart factory
27 November 2017
Few things can damage the financial stability of a manufacturing facility more than unexpected downtime. On average, manufacturers suffer with 30% or more downtime during their scheduled production time. However, there are ways to reduce the risk, as Andy Pye, contributing editor of IP&E, explains
The automotive industry has long been at the forefront of applying new automation technologies, but the industry is also at the forefront of industrial network modernisation. Downtime can cost up to £17,000 per minute.
Traditionally, industrial maintenance has been done on a fixed schedule, replacing items at constant intervals. Constant intervals do not take into consideration the unique circumstances of a machine being maintained, so although general purpose schedules are convenient from the viewpoint of ordering spares, they risk wasting money by replacing parts that are still operational.
Predictive maintenance, on the other hand, aims to get the most life out of equipment while minimising the risk of failure. Increasingly, it involves gathering large quantities of data. While some of this will be existing data, such as maintenance or warranty records, adding data sources such as sensors on the equipment will also be important to build the big picture.
Data challenge
One of the biggest challenges is gathering and interpreting unstructured data, such as free text in maintenance records, design specs, test data from failed equipment, or even comments on social media or Google searches. The most intelligent data analytical automation software will also provide graphical visualisation of production data and generate customised statistical reports.
Having collected all the data, the next step involves using data analytics to make sense of the data, and then figuring out predictive rules that will become the basis for a predictive maintenance model. Once the model is built, it must be tested and progressively refined. But a bad model is better than no model, albeit only marginally – and with progressive refinement via a continuous learning loop the model can be updated based on on-going results. For example, if a component fails after being used for a specific product run, pattern recognition can identify the stresses that are unique to that run that could have caused the failure.
Inside AWNC, the Toyota transmission plant in North Carolina, a recent upgrade includes a new MES, inventory management, predictive maintenance and quality systems that transmit all data for collection and analysis over a secure, Cisco-enabled Wi-Fi network.
Video data
According to test and measurement company HBM, video use is accelerating in data collection. Video cameras are already used in many test and measurement applications in addition to data collection with traditional tactile sensors.
“There is no longer any question that recording video data in parallel to tactile sensors or digital bus signals is becoming more and more attractive to users,” says Christof Salcher, product manager instrumentation at HBM. “Video supports traditional sensor data and is becoming a valuable source of additional information.”
- WBM extends partnership with Nineteen Group
- Western Business Media wins three major awards
- Conveyor and chain lubrication solutions for food and beverage applications
- Western Business Media shortlisted for 10 awards
- Who Would you Hire’ LIVE at Maintec
- Faraday Predictive Launch combined Condition Monitoring and Energy Monitoring systems
- Valuekeep launches a new analytics dashboard add-on to their offer
- Maintenance in the digital world
- IP&E Awards 2024 celebrates industry leaders and innovators
- One venue, two events, many reasons to visit
- New Testo Thermal Imaging Cameras and Special Money-Saving Maintec Offers!
- CNC Engineering - Engineering Excellence you can trust.
- SPM® High Definition - Bearing monitoring as you have never seen it
- Prevention is better than cure
- Kaba Door Systems will exhibit at easyFairs MAINTEC 2011
- JACOB (UK) number 1 for pipework systems.
- Going beyond the repairable asset
- Going beyond the repairable asset part #2 - how to balance cost with returns...
- Smooth running
- Maintec: Boost productivity with Parker