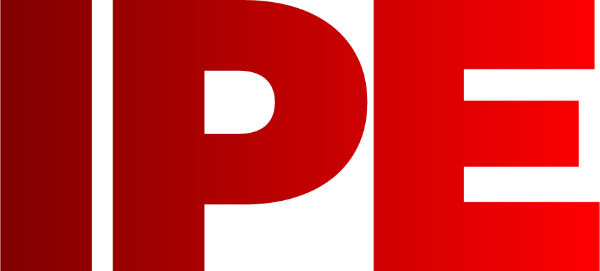
![]() |
Edward Lowton
Editor |
![]() ![]() |
Home> | Handbooks | >AirUser | >Navigating the ISO 8573 air quality standard |
Home> | Energy Management | >Compressors & ancillary equipment | >Navigating the ISO 8573 air quality standard |
Home> | Plant, Process & Control | >Compressors and ancillary equipment | >Navigating the ISO 8573 air quality standard |
Navigating the ISO 8573 air quality standard
30 September 2021
In a typical compressed air system, there are a wide range of contaminants that require treatment if the system is to operate safely, efficiently and cost effectively. Here, Roy Brooks outlines the basic principles of ISO 8573, the international standard for air purity (quality).
Selecting the right compressed air treatment equipment is essential as it can affect everything from maintenance schedules to the ongoing costs associated with achieving the required standards.
The BCAS Best Practice Guide 104 gives details of the 10 main contaminants that typically need to be removed from compressed air or reduced to acceptable levels. These tend to be combined into three distinct categories: particles (including viable and non-viable microbiological organisms), water and oil. ISO 8573-1 refers to the main contaminants in this format.
When selecting purification equipment, it is important to note that contaminants will be in one of three different phases (states of matter). For example, water and oil in a compressed air system will be found in liquid form, as an aerosol (fine mist) and in a vapour (gaseous) phase and a different purification technology will be required depending upon the phase of the contaminant.
Different standards
Depending on application, there are number of different compressed air standards and best practice guidelines which can assist you.
ISO8573 series is the most commonly used standard for compressed air (excluding breathing air or medical air). It is made up of nine separate parts. Part 1 refers to air purity (quality), while parts two to nine provide details on the equipment and methodology to be used to measure for different contaminants in a compressed air system (and meet the air purity (quality) classifications shown in part one).
These include:
• ISO 8573-2:2018 – Specifies the test method for oil aerosol content
• ISO 8573-3:1999 – Specifies the test method for measuring humidity
• ISO8573-4:2019 – Specifies the test method for particle content
• ISO8573-5:2001 – SpecifIes the test method for oil vapour and organic solvent content
• ISO8573-6:2003 – Specifies the test method for gaseous contaminants
• ISO8573-7:2003 – Specifies the test method fir viable microbiological contaminant control
• ISO8573-8:2004 – Specifies the test for solid particle content
• ISO8573-9:2004 – Specifies the test method for liquid water content
• ISO8573-1 – International Standard Relating to Compressed Air Purity (Quality) ISO8573-1 provides guidance on specifying the air purity (quality) required for the entire compressed air system and/or for individual usage points, based upon application requirements. It specifies the amount of contamination allowable in each cubic metre of compressed air and, as mentioned above, should not be used in isolation, but should be used in conjunction with parts 2 to 9 , to ensure that comprehensive indicative testing and/or validation has taken place.
In addition, there are specific requirements for compressed air such as HTM02-1 for medical and surgical air and HTM2022 for medical gas pipelines and dental air.
BS EN 12021:2014 is the standard for breathable quality compressed air, indicating maximum permitted contaminant levels for BA both in the UK and the EU.
Defining air purity requirements
Whether designing new systems, or reviewing existing systems, the first step should be to define the precise compressed air purity (quality) requirements that the application requires.
A robust air sampling policy should be implemented to ensure that accurate measurements are recorded, whether that uses full or partial flow sampling. Full flow sampling is typically employed where the testing equipment can measure at the system’s or the sample point’s flow rate. Alternatively partial flow sampling can be used where the test equipment has a maximum flow rate lower than the flow rate at the sample point.
To achieve the degree of air purity (quality) specified by ISO8573-1, a careful approach to system design, commissioning and operation must also be adopted.
Best practice is to treat compressed air prior to entry into the distribution system and at critical usage points and application, to ensure that contamination already in the distribution system is removed.
Purification equipment should ideally be installed where the air is at the lowest possible temperature, i.e., downstream of air receivers, but also protected from freezing. Point-of-use purification equipment should be installed as close as possible to the application.
To allow correct sizing and selection of purification equipment, make sure you have the following operating parameters to hand:
• Maximum compressed air flow rate into the filters/dryer
• Minimum operating pressure into the filters/dryer
• Maximum operating temperature into the filters/dryer
• Maximum ambient air temperature where the equipment is to be installed (required for some dryer technologies)
• Required dewpoint (dryers).
Individually, each of the primary operating parameters can influence product sizing; collectively, they can have a major impact on product sizing and performance.
Many manufacturing plants only need a proportion of the compressed air to be treated to a very high purity (quality). In these cases, excellent savings are achievable by treating all the generated air to the minimum acceptable level and improving the purity (quality) to the desired level at the usage point.
If most of the compressed air is needed at a high purity (quality), it can make sense to treat all the compressed air to the level required by the highest purity (quality) application.
BCAS workshop
Companies wishing to learn more about the air quality regulations can benefit from BCAS’s blended learning workshop for ISO 8573: http://bit.ly/BCAS-ISO8573, which is now available with 25% off course fees for customers of BCAS members*.
The course is aimed at typical industrial compressed air applications operating at low pressure, with a range between 7 and 20 bar g and provides guidance on the differences between indicative testing and air quality verification, which is a key component of compliance with the ISO 8573 standard.
Learners complete a self-study e-learning module followed by a virtual classroom with a BCAS tutor to help cement their learning and help them understand the most frequently asked questions. The course is completed with an online examination leading to the BCAS certificate in ‘Understanding ISO 8573 – The Compressed Air Quality Standard.’
Roy Brooks is technical development officer for the British Compressed Air Society (BCAS)
* The free associate membership and 25% discount offer is only available to end-user customers of BCAS members. Trade customers are not eligible for the offer.
For more information, visit: https://www.bcas.org.uk/
- Cold weather warning
- New standard targets energy performance
- BCAS apprenticeship standard coming soon
- Working safely with compressed air
- Navigating a shifting landscape: The UK compressed air industry's resilience
- Ashley Quarterman joins BCAS as new executive director designate
- Providing stability in uncertain times
- Changing behaviour to help cut energy consumption
- Update on compressed air standards & regulations
- BCAS urges industry to consider nitrogen as an alternative to CO2