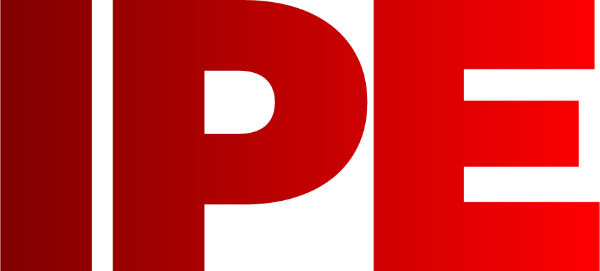
![]() |
Edward Lowton
Editor |
![]() ![]() |
Home> | Handbooks | >AirUser | >Efficiency gains in vacuum technology |
Home> | Energy Management | >Compressors & ancillary equipment | >Efficiency gains in vacuum technology |
Home> | Plant, Process & Control | >Compressors and ancillary equipment | >Efficiency gains in vacuum technology |
Efficiency gains in vacuum technology
16 September 2021
In addition to representing the interests of the UK compressed air industry, the British Compressed Air Society (BCAS) is the only trade association in the UK dedicated to low pressure and vacuum distributors, manufacturers and end users. Here, the Society explains more about vacuum systems.
IT IS estimated that, on average, there may be one vacuum pump for every three compressors installed on a production site. With such a high number of units installed, BCAS has a key role to play in helping advise industry on how to achieve best performance and low operating costs from these critical production components.
Evaluating risk
Air movement provided by vacuum pumps is a vital component of many critical industry processes. Yet, while customers have demanded increased performance from their compressed air solutions, which have helped drive the development of improved energy efficiency and sophisticated control, vacuum pump technology has often been seen as a commodity product.
While the product manufacturing process is scrutinised in great detail, ancillary processes and utilities, such as vacuum systems can sometimes be omitted, often due to a misunderstanding regarding potential risk.
For example, the majority of vacuum pumps currently in use in the food and beverage sector are oil lubricated and under normal operation, there should be no – or very little – oil discharge from these units. However, in certain circumstances where there is a poor maintenance regime or the use of non-genuine spare parts, excessive amounts of oil could be discharged from the exhaust, which could constitute a hazard both to final product quality and operational safety.
This is an area where BCAS members can advise and assist food companies with the pre-requisite programme (PRP) and process air strategy alongside HACCP implementations, taking into account whether the exhaust air comes in to direct or in-direct contact with the food substance.
Improving efficiency
Historically, vacuum pumps often were found to be operating at the minimum performance level without any real consideration for energy performance. Ironically, they would often under-perform compared with state-of-the-art compressors that were operating far more efficiently on the same site.
Today, thanks to industry-led demand for increased efficiency and sustainability, next-generation, robust vacuum pump systems are being manufactured to the same level of quality and reliability as those of compressors.
The latest vacuum pumps have been designed from the outset to enable operators to become more efficient by lowering the cost of ownership, increasing sustainable productivity and enhancing final product quality.
In the operating pressure range 0.5 to 500mbar(a), high-efficiency can be achieved with oil-sealed rotary screw systems, whereby two screw elements rotate at slow speeds, enabling the pump to run at a sound level as low as 69dB(A).
Such silent operation allows installation close to the point of use, with the added benefit of minimum pipework connections and a corresponding reduction in energy losses resulting from pressure drop.
These units offer superior performance against benchmarked oil-sealed and dry vane vacuum pump technologies and, with variable speed drive options, can realise up to 50% savings in energy costs compared with dry vane operating equivalents. As an added energy-saving bonus, there are facilities for process heat recovery from individual pump units.
By looking at all air movement demands collectively, whether for compressed air or vacuum applications, plant operators can realise considerable improvements in terms of cost- and energy-efficiency, plant uptime and system integrity. What is more, rapid advances in energy-saving technologies promise even greater productivity benefits for the future.
Through its Low Pressure and Vacuum Committee, BCAS aims to ensure safe practices are adopted. This can be through the correct application of vacuum and blower technologies as well as influencing the introduction or adaptation of BSI and ISO standards to continue to drive up safety and efficiency across the industry.
Further information about how to specify a vacuum system for your application can be found on the Knowledge Base on the BCAS website at: www.bcas.org.uk/knowledge-base/vacuum-pump-technology.aspx
- Training initiatives: An air of confidence
- Taking an energy-first approach to compressed air system design
- Maintenance best practice for compressed air
- BCAS welcomes its new president
- Providing stability in uncertain times
- Staying abreast of directive changes
- Tackling compressed air energy consumption with the new 10% Taskforce
- Easier investment in compressed air skills training
- Balancing act
- Best practice for sensor calibration