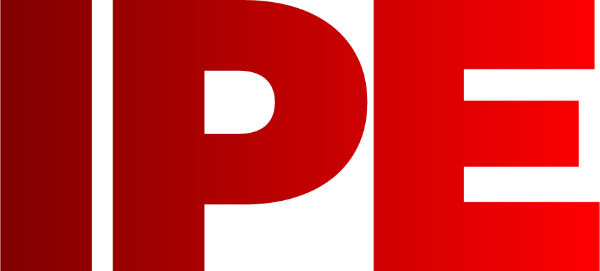
![]() |
Edward Lowton
Editor |
![]() ![]() |
Home> | Efficient Maintenance | >Condition monitoring | >Listen up: Improving leak detection |
Listen up: Improving leak detection
11 November 2024
Mark Bakker looks at how acoustic imaging cameras simplify the process of identifying and quantifying leaks
BEING ABLE to detect leaks is important in many applications, the more common examples being compressed air systems used in manufacturing plants. The costs in terms of downtime created by leaks are well-documented, but what are the best ways of a) locating them and b) quantifying them?
The first key factor is system pressure. Generally, the greater the system pressure the greater the leak, giving it a higher sound intensity, which helps to make it easier to detect. Secondly, the higher a system’s flow rate the greater the leak, also increasing sound intensity. The size and shape of the hole through which air is escaping should be considered together, because detection is affected by a hole’s shape and size.
Gas properties
The sound generated by the leak can also be influenced by the properties of the gases escaping. For example, Helium’s low density means that, when compared with compressed air, the sound pressure levels measured at the leak position will be lower.
Another factor is viscosity. Ambient temperature will affect both density and viscosity which will again influence sound pressure levels at the leak. As ambient temperature increases, the molecule kinetic energy increases, leading to increased sound intensity. Changing ambient temperature can affect the amount of acoustic energy absorbed by the atmosphere. For low frequencies and short distances, the impact of temperature on air absorption is negligible but for very high frequencies and long distances, the sound pressure level can be decreased significantly.
Humidity can impact sound pressure levels due to air absorption, particularly for very high frequencies and high humidity levels. Likewise, ambient pressure will have a direct bearing on the density of a gas which will in turn affect sound intensity at the leak. Because air density and gas pressure have similar but inverse effects on sound speed, ambient pressure makes no difference between the leak position's sound pressure level and that at the measurement position.
When a leak occurs in a pressurised system, the escaping gas (air) molecules will cause turbulence, which in turn causes rapid changes in pressure and flow velocity. Because these changes may be transmitted as sound waves, using acoustic imaging cameras can be the most effective means of detecting the location and intensity of the sound waves.
Consider all angles
The measurement angle can influence the effectiveness of a device’s ultrasonic sensors. Noisy environments are known to degrade the performance of narrowband ultrasonic sensors so using broadband sensors that operate in both audible and ultrasonic frequency ranges allows the operator to compensate.
Fluke ii900 and ii910 Acoustic Imagers have 64 microphones arranged in a specific array pattern, with a visible camera in the middle of the array to provide an image of the scene. The devices use complex algorithms to generate a sound map or image of the sound sources and then overlay the generated sound map on to the image.
Mark Bakker is field application engineer at Fluke
For more information:
Tel: +44 (0) 1603 256758
- Resilience is key for reliability programmes in 2023
- Save up to £4000 on Versiv copper and fibre testers
- Fluke Reliability Unveils Modular Shaft Alignment Solution to Boost Uptime and Cut Costs
- Advanced Atomization reduces reactive maintenance by 90%
- Advanced Wire Tracers deliver superior accuracy and safety
- Partnership brings connected workers to industrial MRO