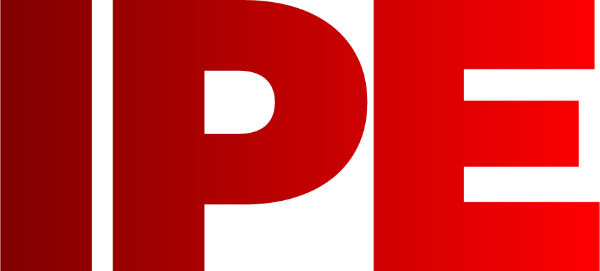
![]() |
Edward Lowton
Editor |
![]() ![]() |
Home> | Plant, Process & Control | >Process heating | >Choosing the right heat exchanger for anaerobic digestion |
Choosing the right heat exchanger for anaerobic digestion
31 July 2024
In the simplest terms, a heat exchanger is like a radiator, designed to heat (or cool) one material from another. However, a wide variety of types and designs are available, meaning that finding the most suitable type of heat exchanger for your application is not always simple, explains Matt Hale

HEAT EXCHANGERS can play a key role in anaerobic digestion (AD) and other energy applications, and all but the most basic heat exchangers are created to a bespoke brief, designed to take into account the material/s being heated or cooled, the heating or cooling medium, the amount of product being processed, product velocity, risk of fouling and a host of other factors. However, over the years some standard design types have emerged (as well as more specific types) and understanding the differences between these can make the specification process less of a mystery.
In this article, we guide you through the main types of heat exchanger produced by HRS and what applications each is best suited to.
Corrugated tube heat exchangers
HRS offers two types of corrugated tube heat exchangers for anaerobic digestion:
- Double tube heat exchangers
- Multitube heat exchangers
Double tube heat exchangers consist of a tube within a tube and are among the most versatile corrugated tube heat exchangers. The HRS DTI Series is a true counter current heat exchanger for industrial use and is ideal for thicker solutions and light sludges. The HRS DTR Series is based on the DTI but has been adapted for direct energy recovery (product vs product), in particular in sludges with low viscosity. The tube is removable for easier and faster cleaning, reducing operational downtime when processing high fouling products such as sludge heating/cooling and pasteurisation, digester heating and sludge-to-sludge heat recovery.
Multitube heat exchangers are the simplest design and carry the product in more than one interior tube, while the service fluid flows through the surrounding shell. The HRS K Series is a complete stainless-steel shell and tube heat exchanger designed for general applications featuring low- to medium-viscosity materials.
Specifically designed for exhaust gas cooling and thermal recovery applications, the HRS G Series passes the exhaust gases through the interior tubes while the service fluid flows through the surrounding shell. The G Series is for heat recovery from cogeneration exhaust gases, boiler exhaust gases, industrial exhaust and flue gases.
Scraped surface heat exchangers
Scraped surface heat exchangers (SSHEs) are the preferred choice for difficult heat transfer applications; for example, those with high viscosities and where fouling can become a problem.
The patented Unicus Series is based on a traditional shell and tube heat exchanger, but with scraping elements inside each tube. The reciprocating movement of the scrapers mix the fluid whilst cleaning the heat exchange surface. This keeps heat transfer high and reduces downtime. The Unicus Series is ideal for the evaporation of digestate and sludges.
Wherever you require heat transfer in your AD or energy application, whether heating digesters, cleaning biogas or pasteurising digestate, HRS have the ideal heat exchanger for you, and the expert staff to help you find it.
Matt Hale is international sales and marketing director at HRS Heat Exchangers
For more information:
Tel: +44 (0)1923 545 625
- Scraped surface heat exchangers deliver superior heat transfer
- HRS offers stand-alone Cleaning-in-Place systems
- The environmental benefits of aseptic filling
- Heat exchangers: Selection matters
- Heat exchanger specification and product identity
- More demand for complete system solutions
- Exploring the potential of process controls
- New crusher allows full juice solutions
- Heat exchangers help produce Spain’s iconic soup
- 9 questions to ask your heat exchanger supplier