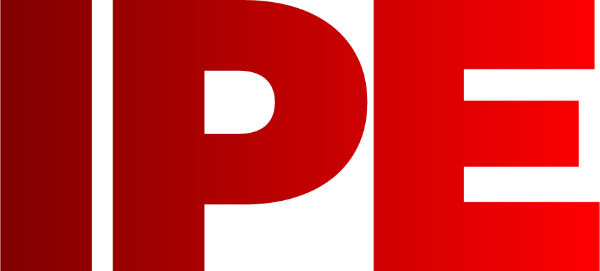
![]() |
Edward Lowton
Editor |
![]() ![]() |
Home> | Plant, Process & Control | >Automation | >Relish the rise of the machines |
Relish the rise of the machines
18 May 2022
The adoption of robotics and automation is increasing in UK manufacturing, but still lags behind the global average. Made Smarter is helping SMEs to leverage these machines to solve the productivity puzzle and unlock people-potential, explains Will Kinghorn

IT'S NO secret that the UK industry’s failure to embrace advanced technologies and continued reliance on human workers to do repetitive unskilled tasks, has meant it hasn’t kept pace with other nations, and seen productivity plummet.
Take robotics. According to the International Federation of Robotics, the UK’s 'robot density', or the number of robots per 10,000 workers, is 101, below the global average of 126, and significantly lower than Germany (371) and South Korea (932).
The positive news is that robotics adoption in the UK is forecast to rise. Five years ago, UK robot density was 71 per 10,000 workers, so there has been a significant increase. And more is to come. The exodus of foreign labour after Brexit has increased the demand for robots. Add to the mix the reduction in cost and massive tax incentives such as the ‘super-deduction’ - enabling companies to claim 130% capital allowance on qualifying plant and machinery investments - and robotics is now much more accessible to SMEs, the backbone of UK industry, providing an opportunity to unlock the productivity problem.
Helping drive digitalisation among SMEs is the Made Smarter North West Adoption Programme, a collaboration between UK government and industry designed to support the increased use of digital technologies among small and medium sized manufacturers and engineering companies.
By providing businesses with specialist, impartial technology advice, grant funding for projects, digital transformation workshops, a leadership programme and broader skills development, we are helping them select the right approach and the appropriate level of investment and tools for their business.
Since 2019 we have helped hundreds of businesses invest in a range of technologies and digital tools. This includes 45 robotics and automation projects worth £2M investment, combining £883k in grant funding and leveraging £1.1M of private finance.
Powering productivity
It has resulted in a raft of benefits for these manufacturers, starting with an increase in productivity. That is because robot systems can have a shorter cycle time than humans. Plus, they can do something that people would struggle with: working 24/7. The result is a substantial rise in how much can be made. They can be used for line resilience as well. If there’s a spike in demand, it’s a simple case of increasing their shifts.
Bloom-in-Box, a manufacturer of eco-friendly plastic products, based in Lancashire, invested in a Fanuc Roboshot electrical injection moulding machine which increases production speed and quality, enabling the business to increase production capacity by between 25-40%.
The technology will improve quality control, reliability and repeatability when moulding components, reducing the number of rejects and waste. This will increase profit and better customer service, improving the likelihood of repeat business. Meanwhile, the automation and remote monitoring features means Bloom can work towards 24/7 production.
Enhanced product quality is another major benefit. Robots are highly precise. This means there is a much lower chance of errors and mistakes, so you can guarantee the quality and consistency of output.
Derek Rose is a British lifestyle brand specialising in luxury nightwear, loungewear, leisurewear, resortwear and underwear, based in Cheshire. It is introducing an auto-cutter to the production process which will integrate with digital design software.
The project is forecast to increase the efficiency and accuracy of the cutting process, reduce waste by at least 10% and improve the planning process by calculating cutting time upfront.
Robotics also reduces operational costs by taking on repetitive, low-value work. This saves some of the costs associated with the particular operation, allowing these savings to be redistributed elsewhere. As a result, manufacturers can boost the quality of other, higher-value areas.
Firstplay Dietary Foods, a manufacturer of foods for special medical purposes, based in Stockport, implemented an automated weighing and packing machine for their pasta and powder product lines.
This was the first investment in automation, which allowed packets to be processed 10 times faster than the manual process. The machine fuelled growth through increasing productivity, capacity, and efficiency. The staff were upskilled in the use of the machine, while also broadening their skill sets allowing them to spend more time on sales and promotion packaging.
Similarly, ammunition manufacturer Empire Cartridges, based in Preston, invested in a six-axis cobot and process control technology which increased manufacturing output of shotgun cartridge shells by at least 50%, increased quality control, reduce manual handling, and upskilled its workforce from box fillers to cobot programmers.
Improving health and safety
Robotics also offers the advantage of better health and safety. Poor work environments and highly repetitive tasks are sometimes harmful to humans, and it is here where robots are best placed. As they don’t suffer fatigue, they’re less likely to make mistakes or experience accidents.
Despite other advantages including better data capture and process oversight, integration with ERP and MRP systems, improved compliance, reduced downtime, and higher space utilisation, some manufacturers believe that this type of technology simply isn’t an option for them. And that’s all down to the challenges that can arise, such as the capital cost of these solutions, and the investment in the skills needed to programme and maintain this new technology.
The key to the success stories I have mentioned is that all these businesses have taken the right approach to implementing the technology. This can be whittled down to four key areas: map your process to identify the best operation to automate, build the business case including specific requirements, speak to suppliers or integrators for proposals, and then select the option which best meets your requirements.
But even if you get all of this right, at the heart of any change are the people. Team members need to be open to it. This is no mean feat, especially with the fear around robots taking people’s jobs. Involving everybody throughout the process will help to create a positive culture for embracing technology, which will focus on how technology can improve their jobs.
Creating employment
Robotics are creating more jobs than they are displacing in the North West, where the 45 projects Made Smarter North West has supported so far are forecast to create 183 new jobs and upskill a further 234 existing workers. Furthermore, the cumulative gross value added to these businesses from their investment is expected to be £137.4m over the next three years.
The ROI on the use of robots is startlingly clear. The next step is for Made Smarter to continue being rolled out to other areas of the UK. And with programmes in the North East, Yorkshire and the Humber, and the West Midlands underway, more manufacturers are now accessing the support they need to adopt technology and digital tools to increase growth, productivity, and efficiency, simultaneously enjoying a long sought-after benefit: the ability to free human workers from the dangers and drudgery of manual work.
Human workers are now being elevated to roles where their individual skills and cognitive abilities can be better utilised, and that is when a business can truly thrive.
Will Kinghorn is robotics and automation specialist for the Made Smarter Adoption Programme in the North West
For more information:
- How SME manufacturers are upskilling workers to create the teams of tomorrow
- Cake-making engineer inspires a new generation of women in industry
- Why North East manufacturers should consider the Made Smarter programme
- Innovative leadership helping SME manufacturers take on toughest test
- Improving maintenance processes through MSIN partnerships
- Emerging technologies used to navigate COVID-19
- Robotics and automation create manufacturing jobs
- New fund to develop digital innovation
- Digital spare parts: innovation to solve supply chain woes
- Helping SME manufacturers make the most of cobots
- Latest software
- Compact robot controller
- Standard machine elements from Elesa
- test baner
- Baking automation
- Higher payload
- Power supplies controlled via web
- New Eiger freezer door installed as business heats up at leading meat packaging company
- Linear and rotary combination
- High temperature chain fluid