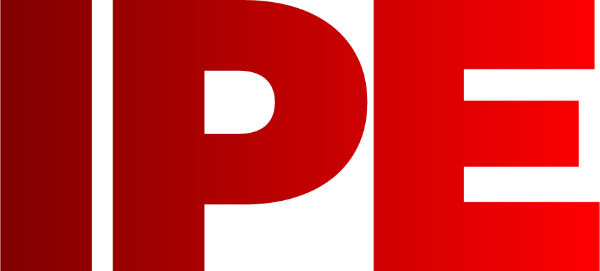
![]() |
Edward Lowton
Editor |
![]() ![]() |
Home> | Plant, Process & Control | >Valves and actuators | >The evolution of the valve island |
The evolution of the valve island
22 August 2022
The recent rise in energy prices underlines the importance of ensuring optimal operational efficiencies. Reflecting this, innovative, robust, and emerging digital valve island technology solutions can deliver flexibility and drive connectivity, while reducing system complexity and building reliable pneumatic system performance, says Chris Patient

COMPONENTS THAT contribute to successful industrial pneumatic production lines must meet critical criteria around reliability, cost, and operational efficiencies.
With it widely acknowledged that reducing the operating pressure within a compressed air system by one bar can equate to an impressive 7% reduction of the energy needed, it’s clear to see why users continue to demand improvements to the system performance of machines and production lines to create competitive advantage.
This entails avoiding unplanned downtime incidents that impact production scheduling, let down customers, and increase costs, by building effective maintenance strategies that prevent incidents occurring in the first place, or can get machines and processes up and running without excessive delay.
It also means having access to, and visibility of, essential performance-linked indicators that, for example, can detect compressed air inefficiencies across the entire pneumatic system. This will help to avoid waste, help prevent leaks occurring, and make a positive contribution to overall energy saving and carbon reduction objectives. And, when you consider the cost to generate the compressed air needed in a production line amount to around 20% of a business’ total monthly energy bill, the case for identifying and avoiding leakages is an easy one to make.
A valve island is an integral component solution that can support efficiency strategies for OEMs and across production settings by enhancing the flexibility, reliability, and long-life performance of pneumatic system solutions.
Modular valve islands are increasingly being specified for automation applications across a wide range of industrial sectors including food & beverage, machine tools, mechanical, packaging, material handling, and paper industries.
Valve islands – sometimes referred to as valve manifolds – are commonly used on machine installations to reduce assembly complexity and downtime, optimise system designs, and allow for the adoption of modern control protocols. Mounted together with a single air supply and common exhaust, they help to reduce pipework, electrical connections, and overall system complexity, as well as provide tangible operational and space saving benefits for users when compared with standalone valve specification.
Connected valve island solutions
It is estimated that the average amount of air lost within a system due to leakages and inefficiencies is a staggering 20%. It therefore makes good business sense to explore the ways in which smart technology which cannot only reduce this figure, but by identifying and mitigating future air leaks, engineering businesses can also reduce the amount of compressed air generated, unlocking significant reductions on their carbon emissions too.
Innovative and emerging smart valve island technology is now taking potential solutions into a new era; one where digital connectivity will drive pneumatic management system benefits that go beyond the traditional valve island.
The connectivity gains include access via IO-Link to built-in intelligence and processing power that allows users to view essential performance data, and on which accurate and robust operational decision-making can be based.
On board displays on the PLC, existing HMIs, or remotely via a PC or mobile phone, puts real time visibility and status information into the hands of the user. Connected valve island solutions can identify what, when, and why a fault is happening on the pneumatic system both on the island and downstream, providing clear insight on how the fault can be quickly resolved.
Practical benefits of smart valve island technology
Among others, there are three key areas where the use of smart valve island technology can add value and support operational efficiency objectives. They are minimising process downtime, tackling complexity in machine build and design, and aiding industrial automation system integration.
Machine breakdowns are inconvenient, impact production targets and are costly. Such incidents mean maintenance teams have limited timespans to identify an issue and resolve it. One answer is the ability to receive proactive alerts if a component is at increased risk of failure and then being able to predict errors. This provides much needed time to respond and the opportunity to prevent the machine failing in the first place.
Connected valve island options deliver data-driven performance insight that maintenance teams can use to underpin operational efficiencies and enhanced productivity goals. IO-Link technology provides predictive maintenance messaging that, for example, a solenoid coil on a valve island should be changed before it fails. This enables proactive action to be taken. Smart valve islands simplify maintenance tasks, provide diagnostic information and support team efforts to keep production running.
Likewise for OEMs who want to create machines quickly, simply, and cost-effectively, build times are critical, whilst technicians’ time is expensive and hardware costs are rising.
Minimising the pneumatic system space required and providing mounting flexibility so the system is easy to add, remove or reposition, can help installation and set-up timescales, especially where machines have multiple customisation options.
The need for customisable solutions
The modularity and flexibility of a valve island answers a practical and operational need for the design of customised machines tailored towards the specifics of a customer. Wide ranging configuration options, valve functions and reduced connections and pipework remove complex wiring arrangements and minimises the potential for errors and leakage in the field.
Finally, integrators specialising in system design and motion control are challenged to integrate multiple products and sensing technologies into a single solution. This adds complexity and creates varied technology platform coordination demands across multiple manufacturers, resulting in time issues and cost pressures.
IO-Link technology on a valve island solution helps to seamlessly integrate hardware and software into a single system, regardless of the technology deployed.
Regardless of the PLC origin, specifying an IO-Link valve island, together with other IO-Link products, means a user can quickly and confidently integrate and add numerous devices into a system via a ‘plug and play’ approach.
Norgren offers an extensive valve island portfolio as a one-stop-shop answer to operational efficiency, preventative maintenance, and cost reduction challenges. The firm's range includes IO-Link technologies that provide data-driven and real time insight on the performance and condition of critical component and pneumatic systems. The company is helping to create powerful infrastructures that are enabling industrial users to better understand, manage, and use their manufacturing processes.
Work continues on future developments, with the objective of making the valve island the core hardware that can consolidate all pneumatic system datapoints. This supports the ultimate intention of building a complete picture of the entire compressed air system across the industrial application and is the next step in the ongoing evolution of the valve island.
Chris Patient is engineering director at Norgren
For more information:
Tel: 0161 655 7300
- Autonomous forklift roll out
- HyperPort wins iF Design Award
- Vibration control facilitates chip production
- Make UK expands online training and learning services to help manufacturers through Covid 19 crisis
- Three reasons why CHP makes sense for industry
- Hard wearing, rapid drying floor screed
- Machine overspeed protection
- Irish manufacturer wins Investment of the Year award
- Welcome
- Industry chief warns ‘no deal’ catastrophic for manufacturing