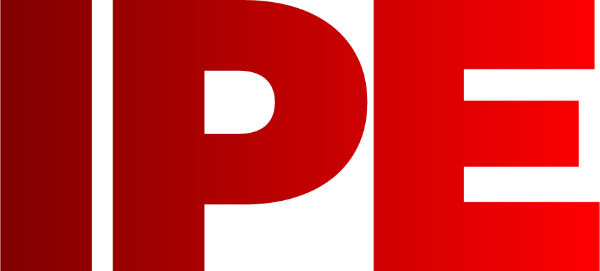
![]() |
Edward Lowton
Editor |
![]() ![]() |
Home> | Handling and Storing | >Lift trucks & ancillaries | >Is robotics the answer to warehouse labour shortages? |
Is robotics the answer to warehouse labour shortages?
18 August 2023
Robotic lift trucks can provide both short- and long-term cost savings related to labour, injuries, damage, and manual equipment fleets. However, ROI is not their only appeal, with leaders also choosing robotic solutions to hedge against long-term labour challenges and promote scalability without labour constraints and volatility, says Ron Farr

LABOUR GENERALLY accounts for 50% to 70% of a company’s warehousing budget, so it’s important to use this limited, expensive resource wisely. In today’s environment, a severe labour shortage and high turnover all necessitate higher wages and competitive benefits in order to hire and retain employees. These conditions are driving operations to carefully evaluate how they utilise labour, allocating workers only for responsibilities that make the most productive use of their time and considering alternatives, such as robotic materials handling solutions, for lower-value, repetitive tasks.
In addition to rising wages, the constant cycle of hiring and retraining workers can further swell operating costs. High turnover rates for warehouse workers and the cost of filling newly vacant positions places operations under pressure. And while training periods for new employees vary, one thing remains constant - training inexperienced or unskilled employees is costly.
Increasing efficiency
Robotic trucks allow logistics operations to perform repetitive tasks, such as moving pallets and loading and unloading, in a more cost-effective way - saving valuable time and money.
However, implementing robotic equipment is not about taking high-value jobs away from operators. Instead, using automated solutions can help managers address the labour shortage and help curb turnover by freeing up employees to advance to more engaging, meaningful positions.
While not every situation is right for robotics, the technology has advanced to accommodate a range of horizontal transportation and vertical storage tasks in many environments. Robotic lift trucks are especially well suited to handle repetitive tasks and long runs, a valuable characteristic warehouses can use in strategies to help curb operator turnover.
Robotic trucks can be used for moving finished goods from the production line to storage/shipping, for transporting goods from receiving to put-away in racking, and for carrying raw goods to the production line. Also, for picking tunnel replenishment, cross docking operations. To realise the greatest benefit, warehouses should evaluate which of their facility’s applications are the best fit for automation.
Freeing up employees
The Yale MC-10-15 counterbalance stacker offers cost efficient transfer and a regular, sustained constant flow, taking care of stock replenishment and transporting goods.
This interconnectivity expands to the wider warehouse infrastructure too - sensors on conveyors can detect pallets at the end of the line and call for the robotic solution to collect the pallet and transport it to its next location.
Warehouses are increasingly using robotic lift trucks to improve productivity. For example, based on existing manual equipment, the Yale robotics portfolio includes the MO50-70T tow tractor, and the MC10-15 counterbalance truck featuring Balyo technology, which are suitable for a wide range of applications, and designed to reduce operating costs and increase efficiency.
Removing hurdles to introducing robotics
Robotics solutions from Yale can be more accessible and flexible than you might expect. After consulting with clients, Yale Lift Truck Technologies recognised that a major hurdle to introducing robotics in warehouses and production lines is the installation of dedicated infrastructure.
By collaborating with Balyo, Yale has been able to produce a range of trucks that use existing structural features to generate their own map, enabling them to self-locate and navigate in real-time. There’s no need to bury wires in the floor or mount reflectors on walls, which reduces the cost of installation and virtually eliminates ongoing structural maintenance. The solution is fully connected to the customer environment and can be integrated into current processes quickly and easily.
Converting to a semi-autonomous labour force frees up workers and resources while fostering a predictable and productive operation. With the operational benefits and savings achieved through robotics, companies can focus on business growth and innovation
Ron Farr is director, warehouse sales - EMEA at Yale Lift Truck Technologies
For more information: