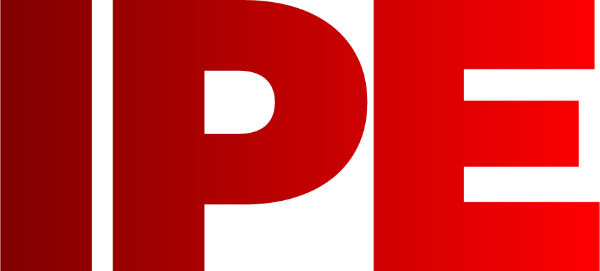
![]() |
Edward Lowton
Editor |
![]() ![]() |
Home> | Handling and Storing | >Lift trucks & ancillaries | >Spotlight falls on retrofit options |
ARTICLE
Spotlight falls on retrofit options
25 January 2013
Before investing in a new lighting installation to save energy, it makes sense to take a look at what the latest lamp and control gear technologies can offer as a retrofit, according to Clive Riddell of Venture Lighting
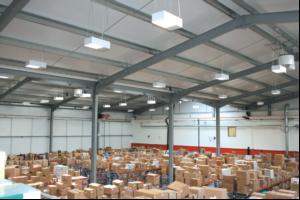
Before investing in a new lighting installation to save
energy, it makes sense to take a look at what the latest lamp
and control gear technologies can offer as a retrofit,
according to Clive Riddell of Venture Lighting
Acombination of economic pressures, energy legislation and sustainability commitment is leading many companies to look for quick, cost-effective ways to reduce energy consumption and carbon emissions. And if they can improve the quality of the workplace at the same time, then so much the better.
To that end, lighting offers a 'quick win' opportunity that can make a significant difference to energy consumption at relatively low cost and with a sensible payback. In this respect, taking advantage of recent advances in lamp and control gear technology - often simply by replacing existing lamps with more efficient ones - offers a cost-effective option.
For instance, if a particular project requires a 35,000 lumen package to meet design requirements; this can be achieved by using an older technology 400W metal halide lamp using cheap control gear.
Taking ballast losses into account, that's a potential electrical load of 445W per lamp.
Or, the same lumen package could be achieved with a higher quality 350W lamp with better control gear that provides just 25W ballast losses - giving a saving of 70W per lamp without compromising on lighting quality. In fact, newer lamps have a longer life and will also maintain their light output for longer, so lighting quality will be improved through the life of the lamps.
Similarly, there are now 200W metal halide lamps that can directly replace older style 250W metal halide lamps to save 60 circuit watts, or 22% energy consumption per fitting (including control gear losses).
Taking this principle a step further, even greater savings can be achieved when high pressure sodium or mercury vapour lamps are replaced with metal halide. For example, a modern 200W metal halide lamp will give the same light output as a 400W mercury vapour lamp, resulting in a 49.6% energy saving.
These examples also serve to highlight a major source of energy consumption of which many building operators may be unaware - namely the significant variation in losses from different ballasts. Here, price often plays a key role because there is a direct correlation between the quality of the product and the quality of the materials used. Furthermore, this correlation has become more marked recently due to considerable increases in the price of copper and steel.
The result is that lower priced ballasts can usually only retain their low cost status by skimping on materials. This, in turn, has a direct impact on the efficiency of the control gear. Thus, a ballast that costs less than a higher quality model could add as much as 55W electrical load to each light fitting.
Consequently, opting for the cheapest ballast is often a false economy.
Another important factor to take account of is controllability - as the maximum efficiency of a lighting installation will only be achieved by ensuring that no light is wasted. In offices using fluorescent lighting, for example, it's common practice to dim lighting when there is plenty of natural daylight, or when areas are unoccupied. In warehouses and factories using traditional high intensity discharge (HID) lighting such as metal halide this has not been possible because older style HID lamps could not be dimmed and they take a while to come back on once switched off.
This situation has now changed with the introduction of advanced electronic ballasts that allow these lamps to be dimmed so that more sophisticated control strategies can be put in place. For example, in a warehouse the lighting in unused aisles can be dimmed to a minimum light output and then be immediately ramped up when someone enters the aisle. Similarly, where daylight is entering the space the lighting can be dimmed while still ensuring the design illuminance is maintained.
For any building operator who is looking to improve the efficiency of their lighting, the first thing is to take a look at how lamps and control gear have changed since the lighting was installed. In many cases, using new lamps and/or gear will prove to be a highly effective solution, with minimum disruption to the workplace and a fast return on investment.
Acombination of economic pressures, energy legislation and sustainability commitment is leading many companies to look for quick, cost-effective ways to reduce energy consumption and carbon emissions. And if they can improve the quality of the workplace at the same time, then so much the better.
To that end, lighting offers a 'quick win' opportunity that can make a significant difference to energy consumption at relatively low cost and with a sensible payback. In this respect, taking advantage of recent advances in lamp and control gear technology - often simply by replacing existing lamps with more efficient ones - offers a cost-effective option.
For instance, if a particular project requires a 35,000 lumen package to meet design requirements; this can be achieved by using an older technology 400W metal halide lamp using cheap control gear.
Taking ballast losses into account, that's a potential electrical load of 445W per lamp.
Or, the same lumen package could be achieved with a higher quality 350W lamp with better control gear that provides just 25W ballast losses - giving a saving of 70W per lamp without compromising on lighting quality. In fact, newer lamps have a longer life and will also maintain their light output for longer, so lighting quality will be improved through the life of the lamps.
Similarly, there are now 200W metal halide lamps that can directly replace older style 250W metal halide lamps to save 60 circuit watts, or 22% energy consumption per fitting (including control gear losses).
Taking this principle a step further, even greater savings can be achieved when high pressure sodium or mercury vapour lamps are replaced with metal halide. For example, a modern 200W metal halide lamp will give the same light output as a 400W mercury vapour lamp, resulting in a 49.6% energy saving.
These examples also serve to highlight a major source of energy consumption of which many building operators may be unaware - namely the significant variation in losses from different ballasts. Here, price often plays a key role because there is a direct correlation between the quality of the product and the quality of the materials used. Furthermore, this correlation has become more marked recently due to considerable increases in the price of copper and steel.
The result is that lower priced ballasts can usually only retain their low cost status by skimping on materials. This, in turn, has a direct impact on the efficiency of the control gear. Thus, a ballast that costs less than a higher quality model could add as much as 55W electrical load to each light fitting.
Consequently, opting for the cheapest ballast is often a false economy.
Another important factor to take account of is controllability - as the maximum efficiency of a lighting installation will only be achieved by ensuring that no light is wasted. In offices using fluorescent lighting, for example, it's common practice to dim lighting when there is plenty of natural daylight, or when areas are unoccupied. In warehouses and factories using traditional high intensity discharge (HID) lighting such as metal halide this has not been possible because older style HID lamps could not be dimmed and they take a while to come back on once switched off.
This situation has now changed with the introduction of advanced electronic ballasts that allow these lamps to be dimmed so that more sophisticated control strategies can be put in place. For example, in a warehouse the lighting in unused aisles can be dimmed to a minimum light output and then be immediately ramped up when someone enters the aisle. Similarly, where daylight is entering the space the lighting can be dimmed while still ensuring the design illuminance is maintained.
For any building operator who is looking to improve the efficiency of their lighting, the first thing is to take a look at how lamps and control gear have changed since the lighting was installed. In many cases, using new lamps and/or gear will prove to be a highly effective solution, with minimum disruption to the workplace and a fast return on investment.
MORE FROM THIS COMPANY
OTHER ARTICLES IN THIS SECTION