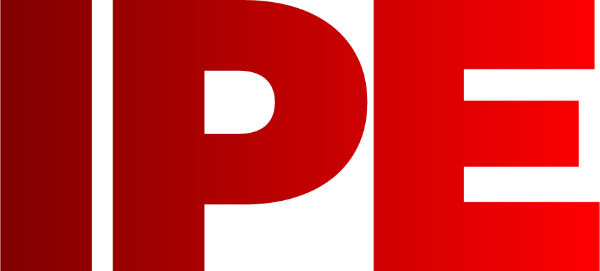
![]() |
Edward Lowton
Editor |
![]() ![]() |
Home> | Plant, Process & Control | >Data capture | >ComoNeoPREDICT adds intelligence to injection moulding monitoring & control |
Home> | Handbooks | >Manufacturing Matters Ireland | >ComoNeoPREDICT adds intelligence to injection moulding monitoring & control |
Home> | Production Engineering | >Quality and tolerance testing | >ComoNeoPREDICT adds intelligence to injection moulding monitoring & control |
ComoNeoPREDICT adds intelligence to injection moulding monitoring & control
21 May 2020
ComoNeo, Kistler’s cavity pressure monitoring and control system, has been made even more effective with the integration of ComoNeoPREDICT, a DoE (Design of Experiments) model based system that enables injection moulders to achieve zero defect production.

The entire injection moulding process can be sustainably optimised to eliminate scrap and pseudo scrap to enhance plant productivity.
With ComoNeoPREDICT, machine settings can be improved to the point where quality, cycle time and process reliability are all optimised. Based on the cavity pressure curve, ComoNeoPREDICT generates reliable statements about each manufactured part in advance.
The quality predictions are based on DoE models that calculate the characteristics of each injection-moulded part. This cutting-edge technology makes use of supervised machine learning algorithms based on neural networks. The first step is to generate a statistical test plan (DoE) which is worked through with ComoNeo on the machine. ComoNeoPREDICT then uses the parameters obtained (such as pressure and temperature curves) and the measured quality characteristics of the part to create a prediction model that serves as a reference for subsequent production runs. If a part is outside of the defined tolerance band limits, it can be separated out automatically. Custom PC software is provided to generate the DoE and the prediction model.
ComoNeoPREDICT adds a range of practical benefits to the ComoNeo system including:
- Accurate scrap separation method from complete quality records
- Users acquire know-how from direct monitoring of predicted quality characteristics
- Pseudoscrap is minimized
- Tolerances and scrap criteria are easily defined
- Relevant curve points for calculation are selected automatically
- No special knowledge of maths or statistics is needed to operate the software
- Ongoing training of models results in continuous improvement
- Significant reduction of manual measuring operations in production.
This standardised and documented procedure means that tests and model calculations can be performed regardless of who is operating the system. The transparency of the method gives users a detailed understanding of the whole process. Kistler believes injection moulders producing precision components for medical technology and other critical high-calibre sectors will value the capability of ComoPREDICT to deliver extensive control of all quality parameters of the moulding process.