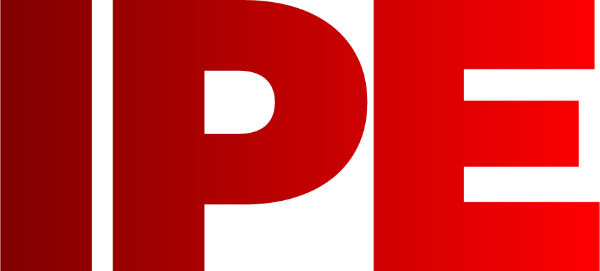
![]() |
Edward Lowton
Editor |
![]() ![]() |
3 Ways to Incorporate Ultrasound Into Lubrication Testing
15 October 2018
When a bearing lacks proper lubrication, damaging friction can occur. Ultrasound equipment allows inspections to read the decibel (dB) levels of under or over-lubricated bearings and alert maintenance personnel to adjust lubrication as needed.
Decibel levels can also indicate when proper lubrication has been achieved (when the dB levels are steady and constant).
Good:
1. Lubricate equipment according to manufacturer’s recommendations
2. Calculate the proper amount of lubricant needed based on bearing type, bearing size and cavity size.
3. Use equipment runtime and operating conditions to determine the proper lubrication frequency schedule.
Better:
1. While continuing on a time-based lube PM schedule, implement ultrasound instruments for more precise lubrication
2. Use ultrasound equipment to let maintenance workers know when to stop applying lubricant
3. Usage of ultrasound instruments may also lead to the discovery of other problems
Best:
1. Combine ultrasound equipment with data collection to compile and compare the recorded history of both decibel levels and sound files
2. Use ultrasound equipment to establish baseline and alarm levels and lubricate equipment once a data point reaches the low alarm or lack of lubrication condition
There are ultrasound instruments available for whatever stage your lubrication program may be in.
From high-end instruments that store data, trend, set baselines and alarm levels, to more cost effective and easier to use instruments that lubricators can use to let them know when they have applied enough grease.
For more information, please Click Here.
- The Latest Technology Trend in Condition Monitoring
- Shifting focus
- Slow speed bearing inspection with ultrasound
- Ultrasound spectrum analysis
- UltraView - Ultrasound Camera for Leak Detection and Partial Discharge
- Using Ultrasound to Enhance Energy Efficiency
- Monitoring slow speed bearings condition using ultrasound
- Bearing Lubrication Reimagined: Remote and Real Time Friction Monitoring and Lubrication
- Steam traps: Testing with ultrasound
- Ultrasound and Vibration analysis: two key elements of predictive maintenance
- No related articles listed