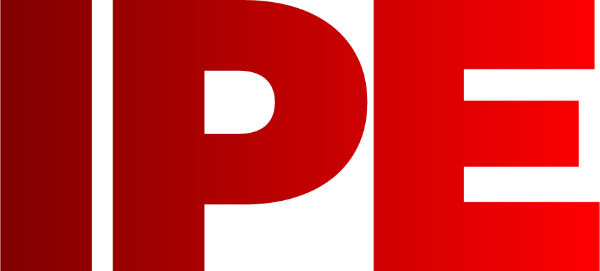
![]() |
Edward Lowton
Editor |
![]() ![]() |
Home> | Handling and Storing | >Conveyors | >Belting solutions |
ARTICLE
Belting solutions
25 January 2013
The latest developments in conveying solutions technology can deliver tangible improvements for the materials handling industry, according to Richard Cole, materials handling industry sector manager at Habasit Rossi I
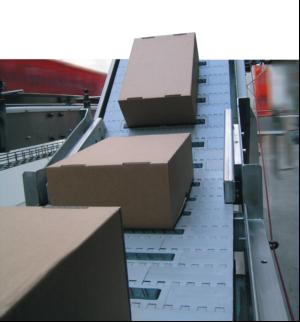
The latest developments in conveying solutions technology
can deliver tangible improvements for the materials
handling industry, according to Richard Cole, materials
handling industry sector manager at Habasit Rossi
In order to maximise plant output, industry requires solutions that are durable, reliable and built to withstand the demands of today's demanding manufacturing environments, where systems are often required to run for 24/7, 365 days a year. The performance of conveying systems can make a real difference to the overall efficiency of materials handling plants and as such, the industry as a whole stands to benefit by re-assessing its current systems.
To maximise the potential output of a plant, engineers must ensure that they select the right conveyor belt for the right application. They must look at whole life costs, energy efficiency and maintenance, as well as whether a belt is really suited to the application for which it is intended.
Actual belt cost is always an issue - now more than ever. However, increasingly, the value of reducing whole life costs through reduced maintenance and energy consumption is being recognised. High performance, well specified belts will result in far more efficient production lines and reduce the amount of unplanned production stoppages, minimising losses in productivity and processing waste.
Using their industry specific know-how, application engineers, technicians and joining specialists are able to supply professional consultation and support when it comes to providing belting solutions tailored to specific needs.
Selecting the material Choosing the right technology can ensure that a plant is working at its maximum capabilities.Whether fabric, plastic modular or power transmission, belts must be able to offer reliability, an increase in system speed, low noise operation, a short turnaround time and system flexibility.
A wide range of high performance belting solutions are available. For example, PVCcoated fabric belts come in a wide rage of surface types, structures and belt strengths and offer good cost:value ratio, suitable for ascending, descending and horizontal conveying and merging applications.
There are non-woven belts suitable for rugged conditions, as well as power transmission belts, which are well proven in live power drive applications and can be tailor-made to meet specific needs. These high efficiency flat and tangential belts are suitable for high power transmission. Some solutions provide energy savings of 6 to 8% in certain situations due to their flexible bending properties.
Timing matters Designed for use in general conveying and linear movement applications where exact product placement and precise component positioning is required, timing belts can improve efficiency in a range of applications, such as automotive assembly, furniture manufacture, component assembly and pick and place systems. Some providers offer timing belts that have been designed for applications where traditional belt options are unable to provide performance synchronisation. Precisely formed teeth with accurate tooth tolerance and robust steel and aramide cords, ensure consistent and exact positioning of the product being conveyed.
Recent advances The latest generation of plastic modular belts, which are used in a wide range of belting applications in materials handling and general conveying, have been manufactured with a variety of surface profiles to grip products such as boxes, travel up steep inclines and maintain product orientation.
There are plastic modular belts which reduce product damage, downtime and overall maintenance, which in turn provides increased belt life and increased throughput.
The all- plastic design of these belts promotes long life and efficient performance in many applications.Multiple widths are achieved by using a 'bricklayed' pattern, which promotes lateral and diagonal belt strength and stiffness.
Friction plastic modular belts can be used in distribution centres, airports, general conveyor systems, packaging end-lines and checkouts. They have also been developed with a variety of surface profiles to grip products, such as boxes travelling up steep inclines, to maintain product orientation.
Looking ahead The UK materials handling industry faces a real challenge to ensure it stays cost effective and achieves high levels of sustained productivity. Leading belt manufacturers have developed products that will help ensure production facilities run at optimum efficiency to control costs, minimise downtime and maximise productivity.
In order to maximise plant output, industry requires solutions that are durable, reliable and built to withstand the demands of today's demanding manufacturing environments, where systems are often required to run for 24/7, 365 days a year. The performance of conveying systems can make a real difference to the overall efficiency of materials handling plants and as such, the industry as a whole stands to benefit by re-assessing its current systems.
To maximise the potential output of a plant, engineers must ensure that they select the right conveyor belt for the right application. They must look at whole life costs, energy efficiency and maintenance, as well as whether a belt is really suited to the application for which it is intended.
Actual belt cost is always an issue - now more than ever. However, increasingly, the value of reducing whole life costs through reduced maintenance and energy consumption is being recognised. High performance, well specified belts will result in far more efficient production lines and reduce the amount of unplanned production stoppages, minimising losses in productivity and processing waste.
Using their industry specific know-how, application engineers, technicians and joining specialists are able to supply professional consultation and support when it comes to providing belting solutions tailored to specific needs.
Selecting the material Choosing the right technology can ensure that a plant is working at its maximum capabilities.Whether fabric, plastic modular or power transmission, belts must be able to offer reliability, an increase in system speed, low noise operation, a short turnaround time and system flexibility.
A wide range of high performance belting solutions are available. For example, PVCcoated fabric belts come in a wide rage of surface types, structures and belt strengths and offer good cost:value ratio, suitable for ascending, descending and horizontal conveying and merging applications.
There are non-woven belts suitable for rugged conditions, as well as power transmission belts, which are well proven in live power drive applications and can be tailor-made to meet specific needs. These high efficiency flat and tangential belts are suitable for high power transmission. Some solutions provide energy savings of 6 to 8% in certain situations due to their flexible bending properties.
Timing matters Designed for use in general conveying and linear movement applications where exact product placement and precise component positioning is required, timing belts can improve efficiency in a range of applications, such as automotive assembly, furniture manufacture, component assembly and pick and place systems. Some providers offer timing belts that have been designed for applications where traditional belt options are unable to provide performance synchronisation. Precisely formed teeth with accurate tooth tolerance and robust steel and aramide cords, ensure consistent and exact positioning of the product being conveyed.
Recent advances The latest generation of plastic modular belts, which are used in a wide range of belting applications in materials handling and general conveying, have been manufactured with a variety of surface profiles to grip products such as boxes, travel up steep inclines and maintain product orientation.
There are plastic modular belts which reduce product damage, downtime and overall maintenance, which in turn provides increased belt life and increased throughput.
The all- plastic design of these belts promotes long life and efficient performance in many applications.Multiple widths are achieved by using a 'bricklayed' pattern, which promotes lateral and diagonal belt strength and stiffness.
Friction plastic modular belts can be used in distribution centres, airports, general conveyor systems, packaging end-lines and checkouts. They have also been developed with a variety of surface profiles to grip products, such as boxes travelling up steep inclines, to maintain product orientation.
Looking ahead The UK materials handling industry faces a real challenge to ensure it stays cost effective and achieves high levels of sustained productivity. Leading belt manufacturers have developed products that will help ensure production facilities run at optimum efficiency to control costs, minimise downtime and maximise productivity.
MORE FROM THIS COMPANY
OTHER ARTICLES IN THIS SECTION