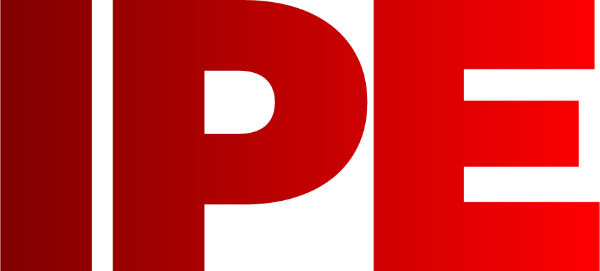
![]() |
Edward Lowton
Editor |
![]() ![]() |
Home> | Efficient Maintenance | >Maintenance products | >Beware winter is on its way |
ARTICLE
Beware winter is on its way
25 January 2013
With autumn upon us,Michael Povey of steam specialist TLV Euro Engineering takes a timely look at what companies can do to ensure that the pipes and pipeline components of their steam systems do not become frozen The
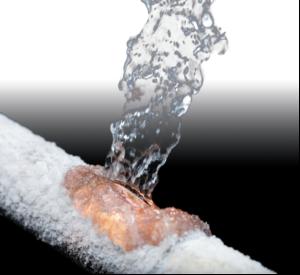
With autumn upon us,Michael Povey of steam specialist TLV
Euro Engineering takes a timely look at what companies
can do to ensure that the pipes and pipeline components of
their steam systems do not become frozen
The summer months are a distant memory and while some of us may still be thinking back to our holidays, is anyone thinking ahead to the long winter months? Most users of industrial process steam shut down office heating systems during the spring/summer months to reduce boiler loading. However, with autumn now upon us, the demand for office heating returns and it's also not unusual to experience an early chill or frost. If you have an extra boiler installed, its services and all the other systems that have been unused during the summer, may be required simply to spread the load.
Over the summer months, cold and possibly more acidic condensate has been slowly corroding pipes and pipeline equipment, and when steam is raised, leaks are discovered where you haven't previously had problems - which is something you don't need when the temperature is barely above the legal minimum.
We know that steam systems will experience heat losses in the depths of winter if exposed pipes aren't insulated, which is why we lag them. However, there are reported instances where the cladding itself is intact but, due to water penetration or birds stealing insulation for their nests, lagging has disintegrated or been removed, increasing the likelihood of freezing on the coldest of days. So how do you check the efficiency of your plant's lagging and cladding? Autumn is a good time to employ a thermographic survey to identify high heat-flux zones that are radiating expensive heat to the atmosphere, costing significant amounts of money and increasing CO2 emissions into the environment.
Be aware too, that pipes are not the only cause of heat loss. Components and fittings are also potential heat sinks. For example, a flange has a greater diameter and mass than the one metre of pipeline fitted either side of it, and should therefore be insulated wherever possible*. And don't forget the steelwork that pipes, fittings and components are attached to. This can also act as a heat sink radiating expensive heat energy to atmosphere, and should therefore be insulated.
Prevention is always better than the cure so at the planning and installation stage of a steam system, pipelines should be either covered or re-routed to reduce the condensation rate in the pipeline system and minimise heat losses from cold winds or water quenching of cladding surfaces.
A final tip: You may think that today's strict environmental regimes would eliminate any chance of pipework not being insulated; however, cladding can be damaged during routine plant activities or even removed and not replaced during summer maintenance. If not noted or reported, the resultant heat losses may not be discovered until costs increase or system performance reduces.
Actions to take Drain off any condensate systems not in use Conduct professional thermographic and steam trap surveys on steam process pipework Ensure that insulation is continuous over the whole system and adequately waterproofed Insulate pipes and fittings from the supporting steel work* Survey and ensure that strainers/traps are clean and operating correctly If you have already experienced freezeups, examine the design and layout of your system and its condensate return pipework and seek advice and assistance if necessary Where possible, install condensate drain and anti-freeze valves at low points on the system and in trap bodies to enable cold condensate to drain before it freezes. This will also avoid problems if the system is shut down for long periods.
To sum up, be prepared and don't be caught out this winter. If in doubt, seek advice from a steam specialist or talk to your component manufacturer.
*Important note. Certain designs of steam traps must not be insulated so contact your steam trap manufacturer for advice.
The summer months are a distant memory and while some of us may still be thinking back to our holidays, is anyone thinking ahead to the long winter months? Most users of industrial process steam shut down office heating systems during the spring/summer months to reduce boiler loading. However, with autumn now upon us, the demand for office heating returns and it's also not unusual to experience an early chill or frost. If you have an extra boiler installed, its services and all the other systems that have been unused during the summer, may be required simply to spread the load.
Over the summer months, cold and possibly more acidic condensate has been slowly corroding pipes and pipeline equipment, and when steam is raised, leaks are discovered where you haven't previously had problems - which is something you don't need when the temperature is barely above the legal minimum.
We know that steam systems will experience heat losses in the depths of winter if exposed pipes aren't insulated, which is why we lag them. However, there are reported instances where the cladding itself is intact but, due to water penetration or birds stealing insulation for their nests, lagging has disintegrated or been removed, increasing the likelihood of freezing on the coldest of days. So how do you check the efficiency of your plant's lagging and cladding? Autumn is a good time to employ a thermographic survey to identify high heat-flux zones that are radiating expensive heat to the atmosphere, costing significant amounts of money and increasing CO2 emissions into the environment.
Be aware too, that pipes are not the only cause of heat loss. Components and fittings are also potential heat sinks. For example, a flange has a greater diameter and mass than the one metre of pipeline fitted either side of it, and should therefore be insulated wherever possible*. And don't forget the steelwork that pipes, fittings and components are attached to. This can also act as a heat sink radiating expensive heat energy to atmosphere, and should therefore be insulated.
Prevention is always better than the cure so at the planning and installation stage of a steam system, pipelines should be either covered or re-routed to reduce the condensation rate in the pipeline system and minimise heat losses from cold winds or water quenching of cladding surfaces.
A final tip: You may think that today's strict environmental regimes would eliminate any chance of pipework not being insulated; however, cladding can be damaged during routine plant activities or even removed and not replaced during summer maintenance. If not noted or reported, the resultant heat losses may not be discovered until costs increase or system performance reduces.
Actions to take Drain off any condensate systems not in use Conduct professional thermographic and steam trap surveys on steam process pipework Ensure that insulation is continuous over the whole system and adequately waterproofed Insulate pipes and fittings from the supporting steel work* Survey and ensure that strainers/traps are clean and operating correctly If you have already experienced freezeups, examine the design and layout of your system and its condensate return pipework and seek advice and assistance if necessary Where possible, install condensate drain and anti-freeze valves at low points on the system and in trap bodies to enable cold condensate to drain before it freezes. This will also avoid problems if the system is shut down for long periods.
To sum up, be prepared and don't be caught out this winter. If in doubt, seek advice from a steam specialist or talk to your component manufacturer.
*Important note. Certain designs of steam traps must not be insulated so contact your steam trap manufacturer for advice.
MORE FROM THIS COMPANY
OTHER ARTICLES IN THIS SECTION