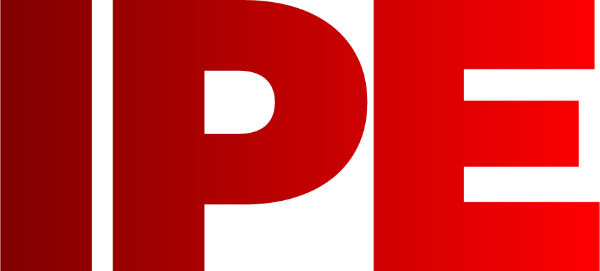
![]() |
Edward Lowton
Editor |
![]() ![]() |
Home> | Plant, Process & Control | >Pumps | >A shift towards actuated valves |
ARTICLE
A shift towards actuated valves
04 March 2013
Valves are integral to the efficient operation of many manufacturing and process plants, but the type of valves being installed is rapidly changing. Here, James Roper, industrial brand manager for Durapipe UK, discusses the industry shift in valve specifications
Valves are integral to the efficient operation of many
manufacturing and process plants, but the type of valves
being installed is rapidly changing. Here, James Roper,
industrial brand manager for Durapipe UK, discusses the
industry shift in valve specifications
With plant managers under rising pressure to increase productivity while reducing costs, more and more processes are being automated, sparking an industry shift over the last 12 months towards installing actuated valves.
The demand for automated procedures has increased rapidly over recent years as plant managers look to achieve a greater accuracy of control and efficiency within the plant, while reducing costs. Moving processes away from manual actions to automated procedures means less manual labour is required, reducing costs and increasing the speed and accuracy of systems.
Plant managers can benefit from automating systems that are required to perform an action and those that purely monitor processes. When an action is required, such as chemical dosing or isolation, if this can be programmed to be undertaken automatically and controlled remotely, it can completely eradicate the need for any personnel on-site, significantly reducing plant running costs.
When it comes to monitoring plant processes, if this is conducted by an operative who needs to manually patrol the plant and check all the processes are performing correctly, human error can come into play and oversights could occur.
It is impossible for anyone to watch all of the processes all of the time, so any problems may not be detected straight away and a delay could be potentially damaging.
An option is to install sensors that monitor the various processes within an automated system, which can be programmed to shut down certain parts of a plant immediately if a problem is detected.
This ensures the issue is identified straight away and can be quickly and easily fixed with minimum disruption, downtime and danger to the plant.
This shift to automated processes has brought with it a need to move to actuated valves, however Durapipe UK is advising that there are a vast array of options available and plant managers need to be careful not to select valves purely on price.
Durapipe offers two main types of actuators for valves - pneumatic and electric.
While there are pros and cons for each, there is no right or wrong option and the decision should be made largely based on the facilities that the plant has and the various processing requirements.
Pneumatic valves have a lower unit cost but they require a compressed air system on site to provide an air supply to power the actuator. It has only a few moving parts and is simple to operate offering a longer lifespan, however, it can only be used in two positions - open or closed. This type of actuator opens and closes the valve very quickly, which may not be ideal for some dosing applications where a very small amount of chemical needs to be accurately measured into a system.
The other option available is electric actuators, which can be easily installed wherever there is a power supply. The unit cost, however, is higher due to the more complex mechanisms involved. This actuation also allows the valve to be locked into multiple positions between the open and closed settings and operates more slowly, offering greater flow control through a system.
With so many options available, the task of specifying valves and actuators can be complex, so it is always recommended to seek expert advice.
Durapipe UK offers a dedicated in-house valve department with technical support staff who can offer specialist advice on the specification and installation of valves and actuators, as well as provide on-site training.
With projects so time critical, prompt delivery is crucial to the smooth-running of installations. The company is able to deliver valves direct to site within 24h of receiving an order in most cases.
Actuated valves are only a small part of an automated system; automated flow/chemical control and measurement solutions are integral to the efficient running of an automated plant. Therefore it is important that all of these products are considered together at the outset so that a fully matched solution, that best meets the requirements of the plant, is installed.
With plant managers under rising pressure to increase productivity while reducing costs, more and more processes are being automated, sparking an industry shift over the last 12 months towards installing actuated valves.
The demand for automated procedures has increased rapidly over recent years as plant managers look to achieve a greater accuracy of control and efficiency within the plant, while reducing costs. Moving processes away from manual actions to automated procedures means less manual labour is required, reducing costs and increasing the speed and accuracy of systems.
Plant managers can benefit from automating systems that are required to perform an action and those that purely monitor processes. When an action is required, such as chemical dosing or isolation, if this can be programmed to be undertaken automatically and controlled remotely, it can completely eradicate the need for any personnel on-site, significantly reducing plant running costs.
When it comes to monitoring plant processes, if this is conducted by an operative who needs to manually patrol the plant and check all the processes are performing correctly, human error can come into play and oversights could occur.
It is impossible for anyone to watch all of the processes all of the time, so any problems may not be detected straight away and a delay could be potentially damaging.
An option is to install sensors that monitor the various processes within an automated system, which can be programmed to shut down certain parts of a plant immediately if a problem is detected.
This ensures the issue is identified straight away and can be quickly and easily fixed with minimum disruption, downtime and danger to the plant.
This shift to automated processes has brought with it a need to move to actuated valves, however Durapipe UK is advising that there are a vast array of options available and plant managers need to be careful not to select valves purely on price.
Durapipe offers two main types of actuators for valves - pneumatic and electric.
While there are pros and cons for each, there is no right or wrong option and the decision should be made largely based on the facilities that the plant has and the various processing requirements.
Pneumatic valves have a lower unit cost but they require a compressed air system on site to provide an air supply to power the actuator. It has only a few moving parts and is simple to operate offering a longer lifespan, however, it can only be used in two positions - open or closed. This type of actuator opens and closes the valve very quickly, which may not be ideal for some dosing applications where a very small amount of chemical needs to be accurately measured into a system.
The other option available is electric actuators, which can be easily installed wherever there is a power supply. The unit cost, however, is higher due to the more complex mechanisms involved. This actuation also allows the valve to be locked into multiple positions between the open and closed settings and operates more slowly, offering greater flow control through a system.
With so many options available, the task of specifying valves and actuators can be complex, so it is always recommended to seek expert advice.
Durapipe UK offers a dedicated in-house valve department with technical support staff who can offer specialist advice on the specification and installation of valves and actuators, as well as provide on-site training.
With projects so time critical, prompt delivery is crucial to the smooth-running of installations. The company is able to deliver valves direct to site within 24h of receiving an order in most cases.
Actuated valves are only a small part of an automated system; automated flow/chemical control and measurement solutions are integral to the efficient running of an automated plant. Therefore it is important that all of these products are considered together at the outset so that a fully matched solution, that best meets the requirements of the plant, is installed.
MORE FROM THIS COMPANY
OTHER ARTICLES IN THIS SECTION