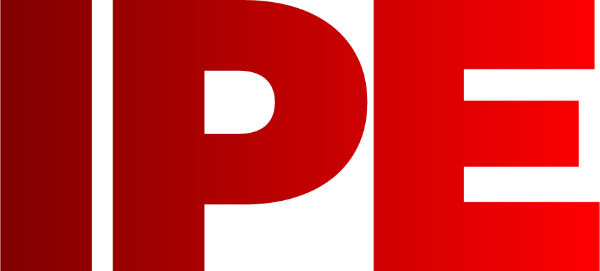
![]() |
Edward Lowton
Editor |
![]() ![]() |
Home> | Handbooks | >AirUser | >Ensuring that safety is paramount |
Home> | Plant, Process & Control | >Compressors and ancillary equipment | >Ensuring that safety is paramount |
Ensuring that safety is paramount
19 July 2013
With so many regulations governing health and safety and compressed air systems, Greg Bordiak, technical officer at BCAS (British Compressed Air Society), believes it's extremely difficult to stay abreast of the latest legislation. Here, he outlines some of the issues and explains how BCAS can help
Hearing loss continues to be a significant occupational disease in the UK with some 17,000 people suffering from deafness, tinnitus or other ear conditions as a result of exposure to excessive noise at work*.
Hand-arm vibration syndrome (HAVS) too can be a significant health risk wherever powered hand tools are used for significant lengths of time. More than 2 million people are at risk of HAVS* in the UK and once the damage is done, it can be permanent.
Pneumatic powered hand-held tools have long been the subject of improved design to reduce vibration at source. These tools can only maintain their reduced vibration performance if the operators are trained in their correct use. To preserve reduced vibration, pneumatic tools should also be maintained correctly.
BCAS provides extensive information and advice to its members on the latest legislation, standards and other health and safety matters. Customers can, therefore, have peace of mind that the installation, upgrade or maintenance of their compressed air system is carried out safely when conducted by a BCAS member.
BCAS is a member of the Noise and Hand-arm Vibration Programme. Introduced by the HSE, the aim of the group is to promote good practice and increase awareness of the risks associated with noise and vibration within the energy, extraction, manufacturing and construction industries.
In partnership with leading stakeholders, the programme aims to eliminate new cases of noise-induced hearing damage in the workplace by 2030.
By 2015, the group aims to control new cases of hand-arm vibration syndrome (HAVS) sufficiently, to enable workers to remain employed without disability.
The partnership group works with supplier stakeholders, such as machinery and equipment manufacturers, to help and influence them in developing noise and hand-arm vibration (HAV) control technology in their products and in providing sufficient information to enable employers to carry out risk assessments.
It also works with industry stakeholders, such as construction, heavy fabrication and foundries, focusing on the development and take up of controls for noise and HAV. Worker awareness and involvement in noise and HAV control is encouraged through the use of toolbox talks and case studies.
Cheap and cheerful?
The use of non-genuine parts in this type of equipment has real hidden dangers. The effects of vibration-related disorders on workers are well known, but such disorders take time to appear.
Pneumatic tool manufacturers go to great lengths to design vibration-reducing solutions. Some of these may not be immediately apparent, but are none-the-less very effective.
An example of where non-genuine spares can have a serious effect on the health of a worker is with needle scalers. On the face of it, this is a simple tool which is barrel loaded with steel needles for removing blemishes from various surfaces. Using non-genuine spare needles to replace the worn, genuine items can result in a five-fold increase in vibration levels, leading to dangerously high levels for the worker.
Taking the cheap option may keep the accountant happy today, but what is the price of using non-genuine parts compared to the cost of injury for a worker who develops a vibration-related disorder?
*Source – www.hse.gov.uk
- Appointments, plenary plans and membership news
- Setting the standard for compressed air quality
- Interaction and communication
- Tackling the skills gap
- Compressed air systems: The need for appropriate training
- 'Uniform needs' – EU law
- BCAS apprenticeship standard coming soon
- BCAS: GB/UK legislation update
- BCAS signs Armed Forces Covenant in industry-wide commitment
- Lowering compressed air cost of ownership through maintenance
- MAT - Modular Air Trolley
- Belt drive compressors
- Monitors compressors
- Plugging the skills gap
- Compressor range
- Modular dryer design
- Accurate diagnosis
- Plant complies with latest medical standards
- Hertz Kompressoren UK launches HSC D direct drive air compressor range
- Filter elements tested to ensure air quality