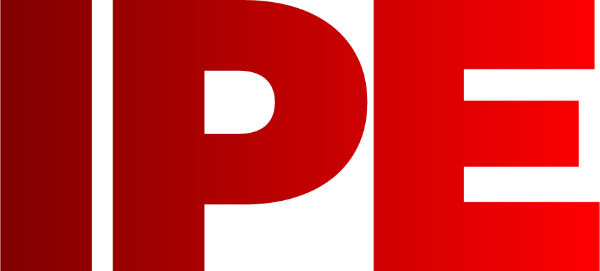
![]() |
Edward Lowton
Editor |
![]() ![]() |
Home> | Production Engineering | >Grinding and abrasives | >Super-size blast-room |
Super-size blast-room
11 October 2016
A 500m³ self-contained blast-room that can accommodate loads of up 60t has been installed by Hodge Clemco at Drax Power Station in Yorkshire as part of a major programme to upgrade on-site maintenance capabilities, simplify logistics and reduce costs.
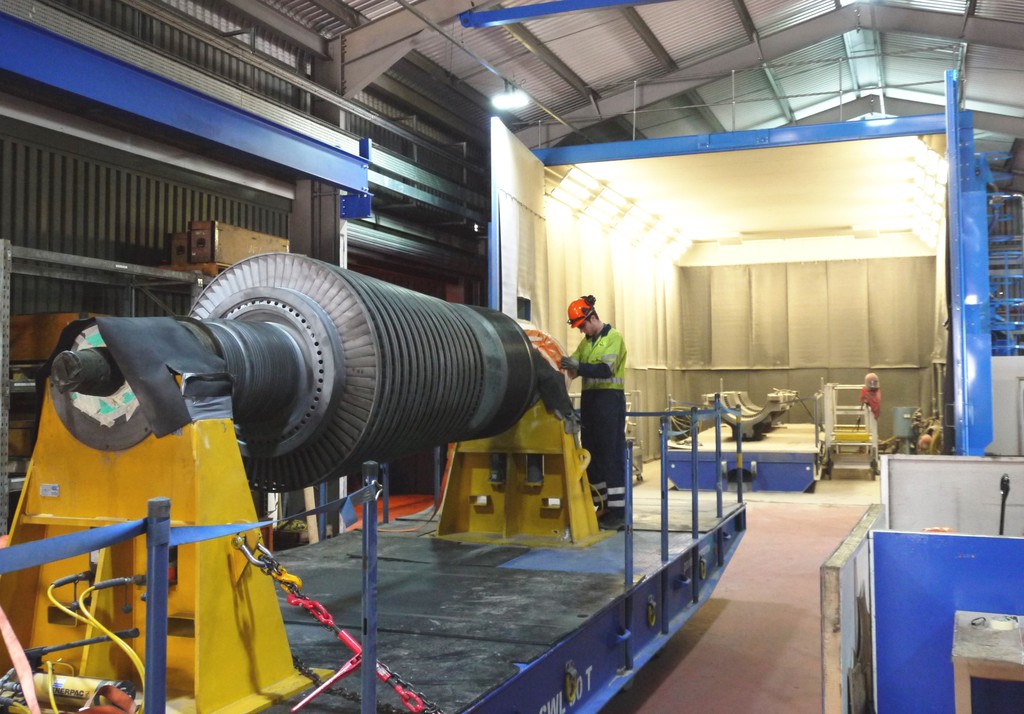
The new blast-room measures 6m high x 7m wide x 12m long and has large double doors to allow items to be driven in on a trailer or lift truck. After cleaning to remove scale and other contaminants, parts are inspected and any remedial work is carried out before glass bead abrasive is used to produce a final surface finish.
Constructed from double-skinned panels filled with 100mm thick acoustic insulation to reduce noise levels externally by up to 30dBA, the blast-room has a welded steel floor. Walls are protected by rubber curtains.
The air ventilation and dust extraction system is rated at 14,000 cfm and provides a linear airflow the length of the room. Large particles fall to the floor, while dust is collected on filter cartridges and then automatically deposited in bulk bags for collection by lift truck. Air inlets and extraction points have been designed and positioned to ensure good visibility for operators.
Staff sweep used abrasive to the input end of a separator system where contaminants, fines and dust are removed. Large contaminants are removed by a rotary screen, while finer materials are removed by an air wash system. Suitable clean abrasive falls into a storage hopper for use as required. A magnetic separator has been included to remove ferrous material. Clean abrasive is returned to a 10t-capacity double-outlet storage hopper that feeds the blasting equipment, providing complete recycling of recovered abrasive.