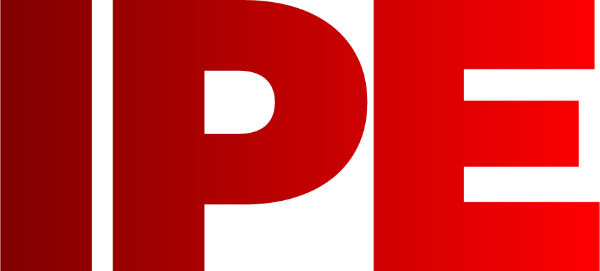
![]() |
Edward Lowton
Editor |
![]() ![]() |
Home> | Production Engineering | >Component cleaning | >Automated finishing system |
Home> | Production Engineering | >Deburring equipment | >Automated finishing system |
Automated finishing system
26 September 2014
Installation of an automated surface-finishing system with a pair of custom-built Hodge Clemco blast cabinets is reported to have significantly improved production of rotor coils for turbo-generators at the Loughborough factory of Brush Electrical Machines.
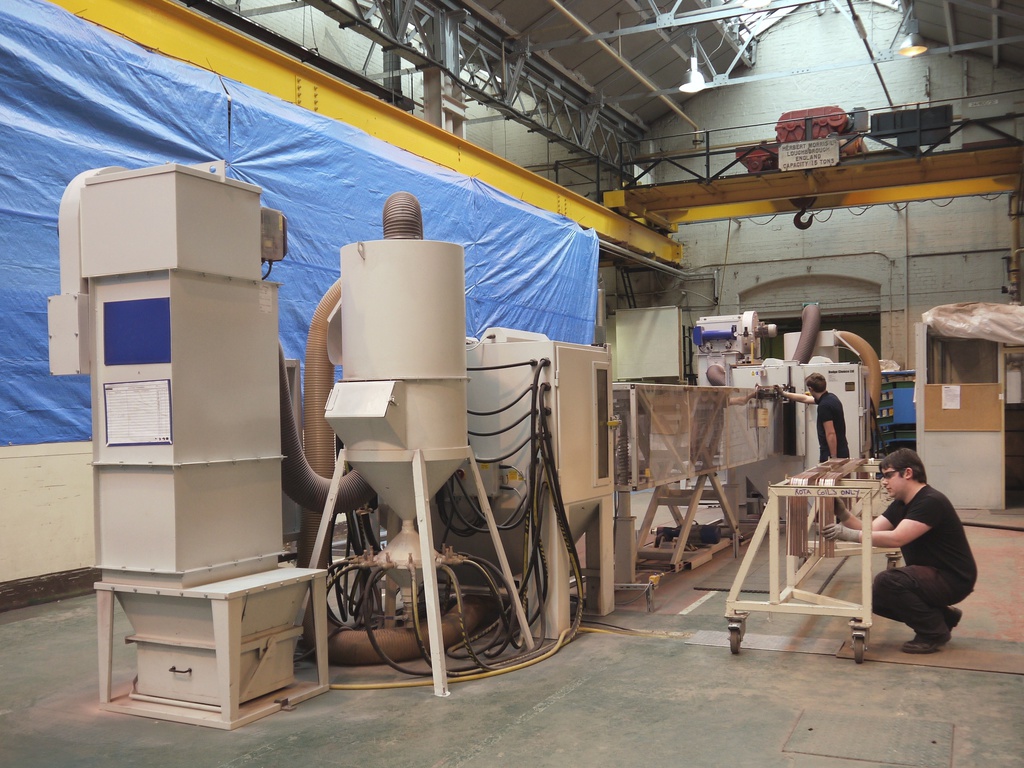
Brush manufacture generators for gas and steam turbine drive. The UK factory produces air-cooled DAX two-pole turbo-generators up to 120MVA output.
The Hodge Clemco blast cabinets are linked to an automatic feed system designed by Rotary Engineering, which has tripled throughput, improved working conditions and resulted in a better and more consistent finish.
As well as the blast cabinets and feed conveyor, the system incorporates abrasive hopper, abrasive cleaning and dust collection equipment in a single integrated unit.
- Bespoke blast cabinets
- Finishing plant boosts production
- Blast room boost to finishing standards
- Upgrade to finishing facilities
- Giant blast-room installed
- Giant blast room
- Tipper body manufacturer upgrades finish quality
- Self-contained production rooms
- Super-size blast-room
- New blast room installed