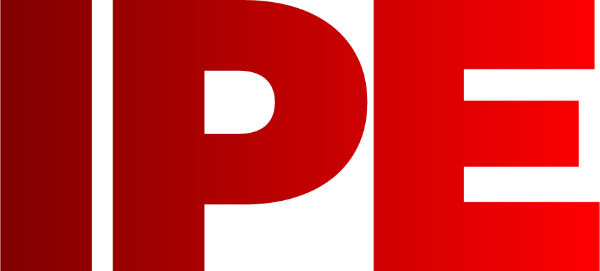
![]() |
Edward Lowton
Editor |
![]() ![]() |
Home> | Plant, Process & Control | >Motors and drives | >Driving out stoppages |
Home> | Energy Management | >Motors and drives | >Driving out stoppages |
Driving out stoppages
18 July 2017
Samuel Taylor, manufacturer of bimetallic strips, has improved the reliability of its production line by retrofitting two applications with ABB variable speed drives (VSDs).
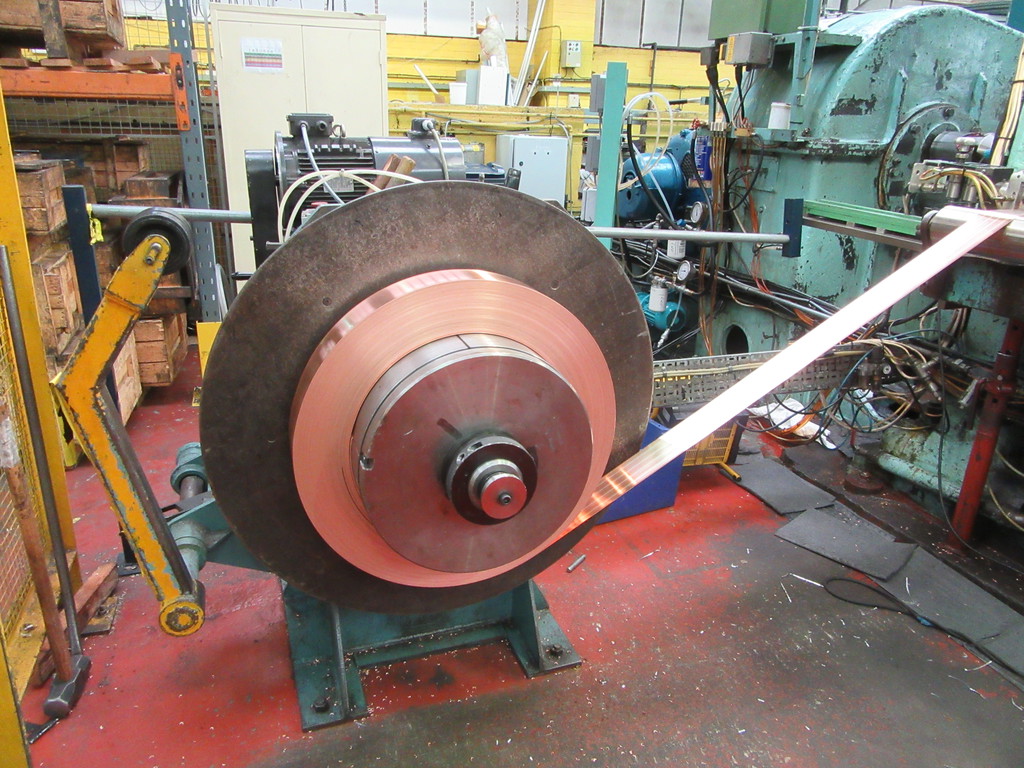
The production line consists of a leveler, grooving and inlay machines, a bonder and a recoiler. The recoiler originally used a DC motor but the need to replace the commutator brush gear meant the motor was often in for repair.
Adford CNC, a specialist in CNC machine tool servicing and repair, refitted the recoiler with a 5.5kW AC motor, controlled by a 7.5kW ABB general purpose drive, ACS580.
Alan Bolton, proprietor of Adford CNC, which worked with ABB authorised value provider, Sentridge Control, on the project, says: “As a modern, digital AC drive, the ACS580 offers many parameters to precisely set or adjust the drive to suit the motor and application.”
A second ABB general purpose drive was installed on the motor on the bonder.
“The direct-on-line (DOL) motor was prone to blowing fuses because of the high initial mechanical resistance. We fitted a 15kW ABB general purpose drive to control the maximum current drawn when starting the motor and overcoming the inertia of the drive train. The client is very satisfied as this has completely cured the problem,” says Bolton.
- Robot demonstration cell
- Bot on the chain gang
- Sweet win for ABB's robotic business
- Transform precision & repeatability
- ABB's robot training masterclasses now available online
- Robotic innovations
- Seminar shows how to get ahead through a switch to robots
- Time to take the mystery out of making a switch to robotic automation
- Seminar and workshop
- ABB launches IRB 930 SCARA robot