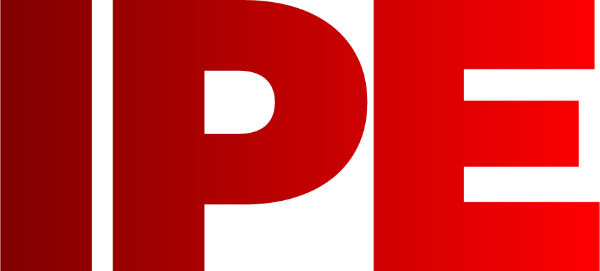
![]() |
Edward Lowton
Editor |
![]() ![]() |
Home> | Production Engineering | >Machine centres and tools | >Anotronic expands precision machining with Sodi-Tech EDM technology |
Anotronic expands precision machining with Sodi-Tech EDM technology
04 February 2025
Known for tackling challenging projects, Anotronic now leverages advanced Sodick machines to meet increasing production demands and tackle complex part geometries with efficiency

ANOTRONIC HAS continually expanded its factory footprint, services, and range of machines over the years.
The Bedfordshire manufacturer currently operates three Sodick machines, with the latest ALC600G Premium wire EDM with linear motor drive technology arriving recently.
A growing partnership
The reliability and performance of the Sodick AQ35L meant that when Anotronic was in the market for another EDM machine, it once again turned to the Sodick brand. "We bought a Sodick AG 600LH around seven years ago. That machine enables us to do tool work up to 500mm high, which we regularly do. We have a large bobbin on this machine, enabling us to run 70 to 80 hours unmanned," explained Anotronic MD Martin White.
The remarkably high level of lights-out machining with the Sodick AG600LH, together with its reliability persuaded Anotronic to invest in its latest EDM machine, the Sodick ALC600G Premium with linear motor drive technology.
Scaling up to meet new production challenges
"We bought this latest machine because we had a project with a sister part. The project typically consists of 40 parts that would maybe take us three months to complete," White continued.
"We suddenly had an order placed on us last year for 300 parts. We couldn’t have done this without another machine, as we knew we would have had to have been machining 24 hours a day to get the parts done."
Specialised machining for unique applications
Sodi-Tech UK sales manager Richard Bailey notes that Martin and Anotronic don’t just take on run-of-the-mill CNC jobs.
“This company tackles the higher end of the industry and often the parts that companies don’t want to tackle themselves. Anotronic looks at jobs from an application perspective rather than a ‘machining time’ point of view,” he stated.
"With the Sodick technology and the special characteristics within the machine, Anotronic can utilise this to run all of its applications and do jobs that are unique and out of the norm."
In this instance, the application that Martin has been working on requires some very steep table angles. The ALC600G Premium has very large U and V-axis travel, allowing the processing of tapered angles up to 45°. So, when it comes to machining this part, it can be done in situ with the integration of a fourth and fifth axis.
"We are using a very complex 4-axis programme to cut a rotary part with 45° slots in it. The only way we could do that was to use the software we currently use, and without it, we couldn’t manage to do the part. So, we used the on-board software within the CNC control of the Sodick machine to take control and create a 3D model and a tool path to cut the part," said White.
For more information:
Tel: +44 (0)1926 695 777
- No related articles listed