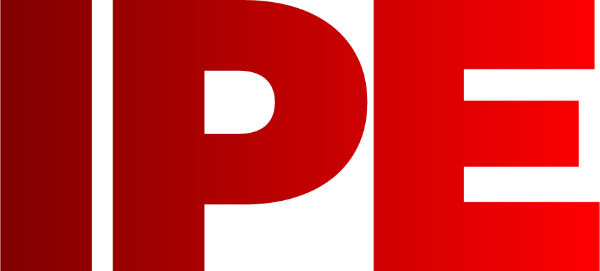
![]() |
Edward Lowton
Editor |
![]() ![]() |
Home> | Production Engineering | >Paints and applicators | >Coatings and paint specs |
Coatings and paint specs
06 December 2019
The world of industrial coatings and paints can be a tricky one to navigate. KTR UK outlines some of the options available.
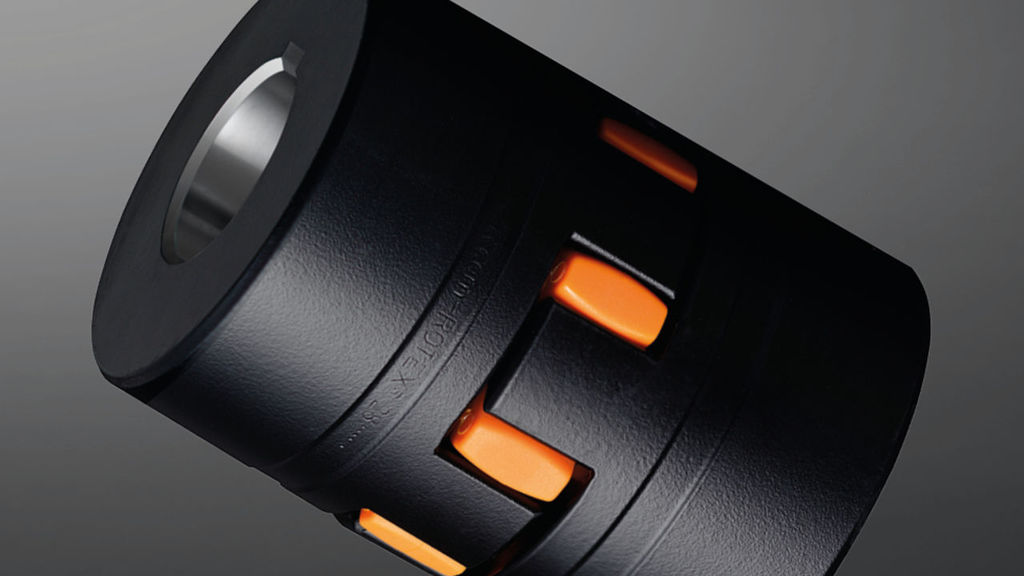
Most people would probably assume that mechanical equipment and structures are robust enough to take on environmental stresses and operational wear and tear. After all, these structures are made to operate in such environments, right? Well, not exactly. In the UK alone, the annual cost associated with the corrosion of major structures and mechanical equipment due to inadequate protection equates to over £10 billion a year (5% of GNP), which is why the UK coatings industry have become experts in creating high-performance coatings made of liquid or heat-curated powder.
Industrial coatings are characterised by their protective properties rather than aesthetic appeal, although some can provide both. Most commonly, industrial coatings are used to protect steel or concrete from corrosion. However, coatings are also used to make materials more resistant to fire and other stressors. Below, we provide a brief rundown on industrial standard coatings as well as the paintings that we offer at KTR.
Industrial Standard Coatings
Tennifer Q: The Tennifer Q coating is used to improve wear resistance, fatigue strength, and corrosion resistance. It is particularly effective when combined with oxidative cooling. This coating is useful for several applications such as those involving water exposure or high-performance two-stroke engines.
Rivolta: The Rivolta Coating is a corrosion-inhibiting wax for effective long-term conservation. It has excellent material compatibility with metals and materials that are stable when in contact with solvents such as paints, plastics, and elastomers. It offers safe corrosion protection, is free of acids and resins, and forms no sticky residues. Additionally, Rivolta coating is free of silicone and according to the German hazardous substance’s ordinance, no classification is necessary.
Safecoat: Safecoat is a premium quality dewatering fluid. Upon evaporation of the solvent, this coating deposits an ultra-thin grease film, which provides effective protection against corrosion and suppresses potential corrosive attacks that result from fingerprints on the couplings.
Standard KTR Paintings
At KTR, we have three standard paintings (C2, C4, and C5), which are classed according to DIN EN ISO 12944. The C3 paint has a layer of thickness of triple 190 micrometres and can be used in explosive environments under ATEX standards. Our C4 and C5 paints have thickness layers of triple 230 micrometres and triple 330 micrometres, respectively, but are not allowed for ATEX applications. As coating thickness increases so does its level of protection. However, it is worth noting that prices generally increase alongside coating thickness/protection.
Additional coatings
Zinc Coating: For certain applications, we use zinc coating on our Radex couplings to prevent rusting.
CDP Coating: The Cathodic Dip Painting (CDP Coating), is a high-quality coating that provides high corrosion protection, UV resistance, and scratch resistance (including resistance against stone chipping and saltwater). It is also an economical and environmentally friendly choice when compared to other types of coatings.
It is important to consult with professionals before selecting or applying any sort of coating. It’s critical for both safety and operational purposes to select the correct coating for your application as types of protection vary.