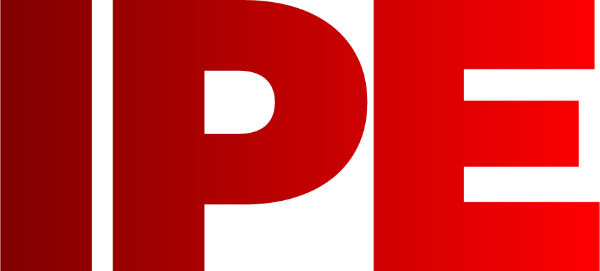
![]() |
Edward Lowton
Editor |
![]() ![]() |
Home> | Production Engineering | >Cutting systems | >Kerf takes centre stage |
Kerf takes centre stage
22 September 2022
TO FULFIL an exponential rise in demand, Somerset manufacturer Serious Stages has invested in an UltraSharp plasma cutting machine from Kerf Developments.
"Before the pandemic, we were considering a laser or plasma machine, as we were subbing-out over £500,000 of laser cutting each year," said Serious Stages fabrication workshop manager Rob Watts.
"The pandemic halted the decision process, but back in March 2021 the movie industry got back to production and we won a substantial order for the next Mission Impossible movie. This gave us the confidence to move forward. We looked at several options and then an industry contact suggested we spoke to Kerf.
"As a company with a complete range of plasma, waterjet and oxy-fuel cutting machines, Kerf recommended its RUR2500 UltraSharp plasma cutting machine with a Lincoln Electric Fineline 170, 170 amp plasma cutting system," he added.
Reducing lead times
At that time, Serious Stages was sending more than £500,000 of work out for laser cutting and the lead time was typically three to five weeks. With the 500+ annual structures requiring thousands of parts to be manufactured and shipped around the UK to complete a 150 to 180 tonne structure, the process is a logistical minefield. Serious Stages wanted to manage its inventory, reduce costs and cut lead times to less than a week whilst also having full control over the process. Kerf delivered the solution.
“We produce tens of thousands of cleats, fixtures, clamps and other components for our structures and they are all made from 3 to 20mm thick mild steel with a typical tolerance band of +/- 0.5 mm. Taking these factors into account, Craig Walsh from Kerf recommended the UltraSharp plasma machine over a laser and it is perfect for our business," Watts continued.
"It is running 10-11 hours a day and 6 hours a day on weekends. The surface and edge finish are comparable to laser-cut parts but more importantly, we have wiped out the long lead times and we can make parts immediately for our fabricating team to weld. Deadlines are critical to our business. You cannot be overdue on a festival – the structure has to be safely installed and assembled to the event deadline.”
Looking at the attributes of the 4m by 2m Kerf RUR2500 machine, Watts explained: "The Fineline 170HD, 170amp plasma unit gives us exceptional cut quality and we can comfortably cut material up to 50mm thick, even though we rarely go above 20mm. The cutting head is extremely efficient and we can conduct more than 3,000 piercings before we have to change the nozzle heads.
"Additionally, the Burny 10LCD control system is extremely easy to operate and if we have any issues, the Kerf engineers can remotely log into the machine to immediately resolve any technical issues. The Kerf support is the best we have encountered from any machine supplier so far."
Designed for manufacturing
With the installation of the Kerf RUR2500, Serious Stages has greater design freedom to develop new parts, enhance its existing portfolio of products and design parts for both manufacture and assembly.
"When we were subcontracting out laser cutting, our design freedom was limited. If our designers wanted to change a drawing, alter dimensions or move features – we would have to create a new drawing, send it to the subcontract supplier and wait for them to produce the part and send it to us," Watts stated.
"We could be waiting weeks for the part; and if the design change wasn’t feasible, we would have to start again. The time constraints on our business limited this exercise. Now, a designer can create a new CAD file, use the Lantek software to convert the DXF file to a CAM file and then fire it straight to the Kerf RUR2500.
“We can edit existing programmes in minutes and create new part drawings and send them straight to the Kerf machine – giving our designers complete autonomy with production. This will enable us to expand our current capabilities and flexibility and as we re-design parts, we will see manufacturing and fabrication times throughout the facility reduced.
"This design freedom will also reduce construction time for our on-site building teams. One example that has already benefitted us is the design change to our railings. Where the on-site team had to bolt sections of railings together, now we have added location pins and each section can rapidly be dropped into place to connect with the next. This is just one area where we are already using design for assembly to speed up our construction phase."
Supplying the film industry
With the company winning an order from the Mission Impossible franchise and orders rapidly coming in from other film studios, the subcontract laser cutting cost was rapidly heading from £500,000 to £750,000 which made the decision to invest in the Kerf machine more pertinent.
"As soon as studios realised that we could design, manufacture, deliver and construct a temporary building in a matter of weeks and not months and then remove the structure upon completion of filming, the movie studios were intent on securing our services," said Watts. "We have just delivered a 20,000sq/ft Netflix building in less than 10 weeks. At the Shinfield studios in Reading, they had a six-month head start on us and now we are 18 months ahead of their schedule - this is the speed of delivery we can now offer with the help of the Kerf RUR2500."
At present, the 150-employee business is producing two 150-tonne 40,000 sqft steel buildings for the Mission Impossible franchise and it is manufacturing two buildings for Walt Disney, another two for Netflix and also structures for the renowned Longcross studios. Recent projects also include Kenneth Branagh films such as Death on the Nile and Murder on the Orient Express as well as Bohemian Rhapsody and Empire of Lights.
"This industry was a very small percentage of our business and it has rapidly exploded to almost 80% of our turnover. We have rapidly gone from four fabricators to 18 and we are using more than 20 tonnes of welding wire a year. Without the Kerf RUR2500 plasma machine and a small bending machine we acquired, we wouldn’t be able to cope with the workload," explained Watts.
"With previous subcontract laser cut parts, there was always an issue and this could be anything from burrs and sharp edges on parts, missing parts and incorrect batch supply, varying quality and precision of parts and more - now we have complete control of the process. Previously, our supplier would charge us £3 to cut and bend a steel cleat. Now, we can put a steel sheet on the Kerf and cut hundreds of cleats in a few hours and then bend them on our bending machine – the cost saving is huge and there is no three to five-week lead time. If we are short of parts, need spares or extras, we can cut them in minutes," he concluded.
- Kerf Will Be a Cut Above at Metals Expo
- UltraSharp technology
- Interest grows in new and second-hand machines
- Profiling and cutting machine
- Kerf to present 'one-stop-shop' at MACH
- Sub-contract costs slashed
- Plasma, waterjet and oxy-fuel cutting
- Plasma cutting machines support Irish architectural steel company
- High definition plasma cutting
- Latest plasma cutting machine