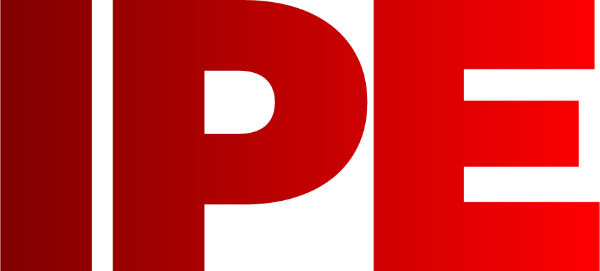
![]() |
Edward Lowton
Editor |
![]() ![]() |
Home> | Energy Management | >Compressors & ancillary equipment | >Lowering compressed air cost of ownership through maintenance |
Lowering compressed air cost of ownership through maintenance
08 January 2024
COMPRESSED AIR is often referred to as the fourth utility, with the electrical energy used to drive air compressors equating to approximately 10% of all the electricity used in the UK.

When it comes to the cost of owning a compressed air system, operators will be well aware that energy accounts for the biggest ongoing outlay. But, maintaining the compressor over a potential 10-15-year lifespan will also represent a significant investment - making it of prime importance that the installation is serviced regularly by a competent maintenance professional. There are a range of key areas to consider when planning a compressed air maintenance regime.
As many as 90% of all manufacturing plants use compressed air and in process plants, it is used extensively across the entire production process. Applications range from operating air tools on production lines, to adjusting roller and feed machinery to finishing and packaging with pneumatic devices.
Compressed air is accepted widely as a highly effective and safe form of power/energy for the process industry. However, generating the high-volumes of air demanded by the application can be energy-intensive.
A key challenge for operators therefore is to improve bottom line productivity by reducing overall cost of ownership - and effective compressed air maintenance can play a key role.
Many end users are now considering the total cost of equipment ownership over its entire life, rather than just its initial capital price. And this is important, because over 80% of this cost base can be in the system’s energy consumption and maintenance in the ten years after the initial purchase.
Maintenance is also a vital part of the overall cost base, to keep both the efficiency and whole life costs of a compressed air system down. End users are realising that moving towards regular routine maintenance rather than reactive maintenance is far more cost effective and will help to reduce unplanned downtime.
Intelligent data
In particular, with the continued emphasis on Industry 4.0 and intelligent data, many operators are benefiting from far greater insight into their compressor performance and are implementing predictive maintenance regimes, preventing potential system faults before they even occur.
Another area to consider is the increased uptake of data logging, with many suppliers now auditing the performance of an existing compressed air system in terms of energy consumption, peaks and troughs in demand and areas of inefficiency. The information obtained can then be used to recommend system improvements - from investing in new, energy-efficient equipment, to heat recovery options or simple upgrades to existing plant.
The current trend towards data exchange and increased automation in manufacturing is a positive move and is providing operators with far greater insight into the performance, and efficiency, of their compressed air system.
Operators are all too aware that electricity accounts for a significant proportion of compressed air cost of ownership and therefore, finding new ways to minimise energy consumption is key.
Typically, this has been achieved by investing in new, energy-efficient machinery but now, with the availability of so much data, operators can realise far greater control over their existing compressor estate; monitoring performance parameters 24/7 if required to ensure the most efficient operation.
Safety first
A vital part of safely and efficiently managing a compressed air system is in the installation, servicing and auditing - all of which have varying amounts of regulation.
Just like other items of industrial equipment, the compressor needs to be installed and maintained correctly to ensure it offers maximum performance and operates safely.
As a result, BCAS continues to remind all compressed air end users to ensure that their employees are fully trained on the requirements of the Pressure Systems’ Safety Regulations 2000 (PSSR), and in particular, the importance of the written scheme of examination
Genuine spare parts
A compressor, like any piece of industrial equipment is a machine and all machines experience wear and tear. At some point component parts will need to either be repaired or replaced.
Therefore, operators should always specify genuine spare parts and avoid the temptation of alternatives which may appear initially to have a lower purchase price, but can affect the running of the machine and its overall efficiency. In the long term, using spare parts that are not designed and tested for the specific machine can result is cost increases in excess of 25%.
It’s also advisable to question the compressor supplier’s policy on spare parts availability and obsolescence, as a compressed air system is a long-term investment and any downtime can be a significant production cost.
End users should therefore take the time to check the credentials of the equipment manufacturer and also of the supplier that will be responsible for maintenance. In addition, the ongoing availability and the longevity of the spare parts as well as the service levels provided by the maintenance provider are key in the decision making process.
The benefits of improved compressed air system maintenance
- Optimise compressed air system efficiency
- Avoid energy losses through downtime and equipment that has been modified from its initial specification with non-genuine components
- Have confidence that your compressed air system is performing as it should – giving you time to concentrate on other energy-saving measures
- Avoid unplanned outages and downtime
- Work with a compressed air service provider to ensure service levels support the business as required
Our top tips
Always use genuine spare parts, rather than alternatives: The time taken to ensure replacement parts are genuine could save thousands in downtime and increased energy consumption.
Include leak detection in the weekly maintenance regime: Fixing just one tiny leak, will stop energy wastage and ultimately save cost.
Monitor and control: Understand how the system is performing, make changes and optimise running hours, for improved electricity consumption.
Use a BCAS member as a professional service provider: The will have invested in their business via their membership subscription and will have the most up to date information to assist their customers.
For further advice on simple ways to improve compressed air system maintenance, download the BCAS guide: tinyurl.com/25h2cy7w
Tel: 0207 935 2464
- BCAS launches industry-first NVQ for skilled compressed air engineers
- Setting the standard - raising the bar
- Safety:Maintain at all times
- Enhancing safety through efficient maintenance
- Compressed air systems: The need for appropriate training
- Ongoing support in times of change
- BCAS: GB/UK legislation update
- Trade associations: Promoting and defending members' interests
- BCAS appoints Terry Collier to further strengthen its training offer
- Evolving to meet members' needs