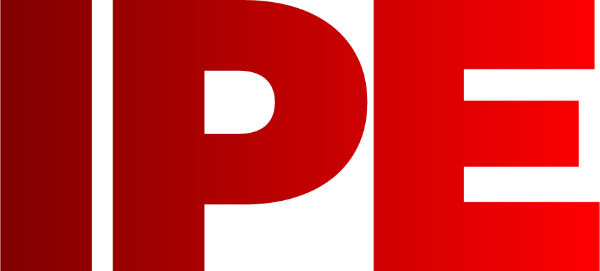
![]() |
Edward Lowton
Editor |
![]() ![]() |
Home> | Energy Management | >Boilers and burners | >Waste not, want not |
Waste not, want not
24 March 2022
Chris Horsley looks at the innovative development of supercritical CO2 technologies in industrial waste heat recovery and the challenges faced when designing a heater for it
HEAT RECOVERY has become increasingly popular within industry, driven by high energy prices, environmental regulations, and a desire to reduce carbon footprint. However, heat recovery systems are rarely a straightforward ‘plug and play’ option in industry.
Industrial Waste Heat Recovery: the challenges
No two sites or process are the same, with industrial waste heat coming from multiple sources and with a wildly varying temperature range. As a result, heat recovery systems are frequently bespoke in nature or, at the very least, require extensive modification of existing equipment and expert installation to achieve the best results. This clearly comes at a premium and can also be disruptive and result in site downtime, adding to the overall cost and ROI time.
To truly make heat recovery appealing to users, the energy efficiency of these systems needs to be improved to reduce ROI time, and installation made far simpler.
The EC Horizon 2020 grant funded I-ThERM project, coordinated by Brunel University London, set out to do just this. The project was divided into three areas, with Babcock Wanson involved in the recovery of heat from temperatures above 300°C using a Supercritical Carbon Dioxide System.
Supercritical carbon dioxide
When Carbon Dioxide is held at, or above, its critical temperature (31°C) and critical pressure (73.8 bar) it turns into a fluid state, known as Supercritical Carbon Dioxide (sCO2).
sCO2’s thermal stability and non-flammability, makes direct heat exchange from high temperature sources ranging between 350°C - 800°C possible. Furthermore, its physical footprint is simple and compact, and it has a low toxicity and environmental impact. All of which make it potentially appealing when it comes to heat recovery systems.
As with any new technological development there were hurdles to overcome, not least of all characterising the behaviour of sCO2, but also the design and operation of the turbomachinery components and heat exchangers.
Heating up
Designing and building a Supercritical Carbon Dioxide Heater presented a host of new challenges, as not only does the heater have to contend with very high temperatures, it would also be used for testing so needed to be adaptable.
Following several briefings and learning more about the process and the testing regime, we built a specialist Direct Process Air Heater, using our MIXBLOC Heater as the starting point as it is designed to provide high temperature air with no flue gas losses. MIXBLOC can operate using the process air flow as the source of combustion air, or an independent combustion air fan. Burners are constructed from multiple “V” elements assembled in differing configurations to suit the required heat input and process ductwork design, thus making it ideal for the I-ThERM sCO2 project.
The heater was designed for operation at up to 780°C air temperature with heater lockout set at 800°C. Burner turndown ratio was retained at 5:1. The process fan size was specifically selected to account for the higher head loss associated with operation at higher working temperatures and with a heat exchanger located close to the heater outlet.
A final discharge cooling system was included, comprising of air cooler with variable speed fan to allow the final exhaust to be cooled to around 350°C irrespective of the heat absorbed into the sCO2.
Both fans are VSD controlled with the primary fan speed being automatically compensated for back pressure and against the design flowrate using an inlet air flow meter, thereby allowing the air flow and final discharge cooled air temperature to be preset on the control system HMI and via the remote function using the Ethernet connection.
As the heater was being designed for a test site, we manufactured and supplied a 2m “dummy” section between the combustor and cooler to allow the system to be fully commissioned and operated without the very specialist heat recovery unit being in place. This means the system can be tested at varying heat load/temperature and air flow settings without the heat recovery unit being present to allow for the test protocol to be formalised and proved without risk to the heater battery.
A further adaptation to accommodate the test conditions included the mounting of the combustion chamber section on roller type feet to allow it to be moved back up to 20mm to ease the installation of the differing heat exchanger sections and to help form a good, gas tight seal during site tests.
Both the heater and cooler unit are made of carbon steel construction throughout and are fully ceramic lined (including the dummy section) to cope with the high operating temperatures involved in heating CO2 to its supercritical state. The system is natural gas fired and we also supplied a gas booster to provide up to 70 mbar of lift, plus a suitable in-line gas meter with analogue input to the MIXBLOC heater control system to display and re-transmit the gas consumption under test conditions.
The final unit consisted of a fully packaged plant complete with all controls and interfaces for both local and remote monitoring plus remote adjustment of set parameters prewired and mounted to the heater. Control is via Siemens PLC with touch screen HMI for simple and clear operator interface. Because of the specialist nature of this equipment and the project, one of our engineers attended on site to advise on installation requirements and our team undertook process commissioning/trials as part of the equipment handover.
Waste no more
The I-ThERM project is still ongoing and has led to further funding from the EC and UK Research and Innovation to develop advanced heat exchanger and controls for full scale industrial sCO2 heat to power systems. Three of the four technologies it presented (two covering heat recovery technologies for operating temperatures of 200 - 1,350°C, and two heat-to-power technologies with operating temperatures of 70 - 1,000 °C) have been recognised by the EC’s Innovation Radar, which identifies the most promising innovations. The sCO2 technology, which is completely new, is one of those, as Professor Savvas Tassou, I-ThERM project coordinator and director of the Institute of Energy Futures, Brunel University London, states: “The supercritical CO2 waste heat-to-power cycle is a unique technology and the first complete system to be operational in Europe.”
With an electrical power output of 50 kilowatt-electric (kWe), the sCO2 system is expected to deliver energy and GHG emission savings in excess of 15% and ROI of under three years. A technology that works with high-temperature waste heat (350-1 000°C), it is ideally suited to the steel, cement, glass and petrochemical industries. According to Savvas, it has already received significant interest across Europe for such industrial organisations looking to reduce their energy consumption and emissions whilst also increasing their global competitiveness.
Chris Horsley is process engineering director at Babcock Wanson
www.babcock-wanson.com
020 8953 7111
- Building sustainability into a process
- Babcock Wanson extends Modulo+ range
- Recuperative Oxidisers
- Rental service
- Energy efficient process heating
- Regenerative Oxidisers
- Steam raising system on skid or in container
- Steam generator
- Babcock Wanson Group joins the United Nations Global Compact
- Thermal fluid system